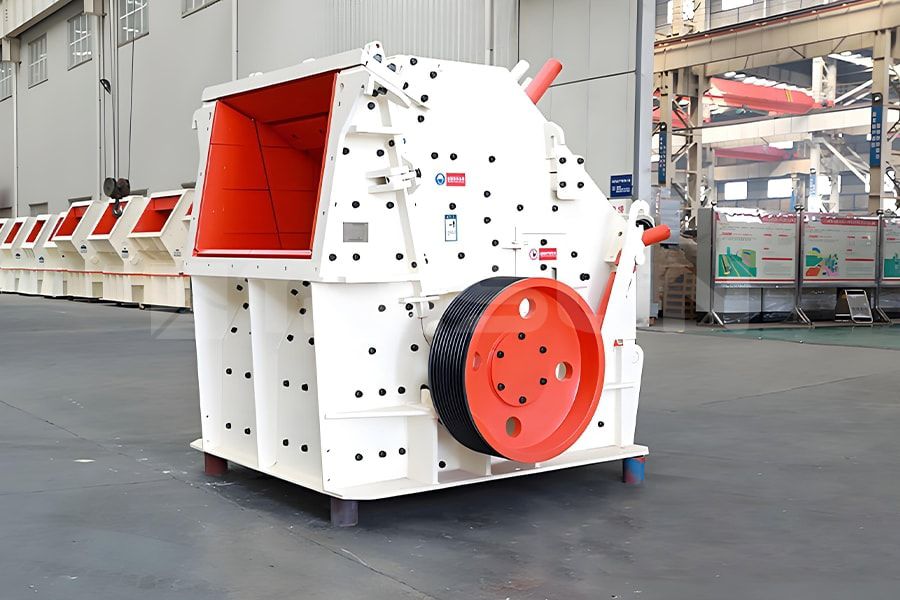
- Features & Properties
- Technical Specification
- Gallery
- Related Products
1. The finely designed rotor and cavity, speed and power are reasonably matched to meet different applications of coarse crushing, medium and fine crushing and material recovery.
2. The sturdy heavy-duty rotor structure improves the crusher's processing capacity and crushing ratio; the high-quality welded structure ensures that the machine can withstand large impact forces and obtain good crushing effects.
3. Ship-shaped hammer, with a reliable locking structure, has good impact resistance and wear resistance and maintains stable discharge particle size.
4. Extensive use of new high-wear-resistant materials reduces the wear of wear parts, extends the replacement cycle, and saves costs.
5. Hydraulic opening and hydraulic auxiliary adjustment of the gap between the impact plate and the hammer reduce labor intensity and shorten downtime.
6. Equipped with a variety of locking devices to improve safety performance and reduce labor intensity.
7. The third impact rack can be optionally installed to make the discharging shape more excellent.
Model | Maximum feeding size (mm) | Capacity (t/h) | Power(kw) | Dimensions (mm) | |
Secondary crushing | CI1110 | 250 | 60-210 | 160 | 2826×2087×2285 |
CI1213 | 300 | 80-280 | 200 | 2903×2530×2411 | |
CI1316 | 300 | 100-350 | 250 | 3320×2770×2535 | |
CI1521 | 350 | 200-600 | 2×(200-250) | 3450×3620×2770 | |
Primary crushing | CI1313 | 600 | 100-480 | 200 | 2972×2560×2937 |
CI1415 | 600 | 120-600 | 250 | 2985×2790×3068 | |
CI1620 | 800 | 220-900 | 2×(200-250) | 4261×3480×3780 | |
CI2023 | 800 | 400-2000 | 2×500 | 5151×4424×4712 |
Note: All features, functionality and other product specifications are subject to change without notice or obligation.
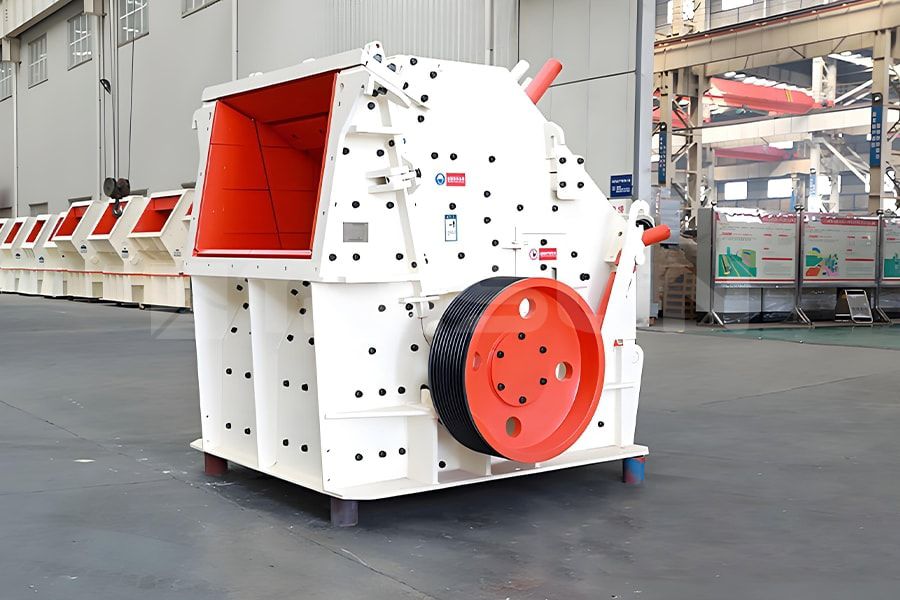
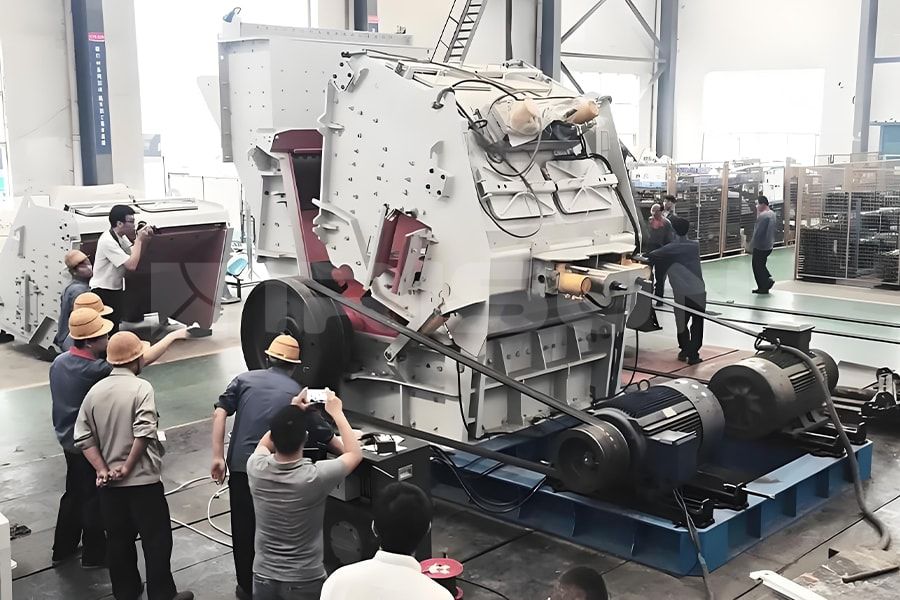
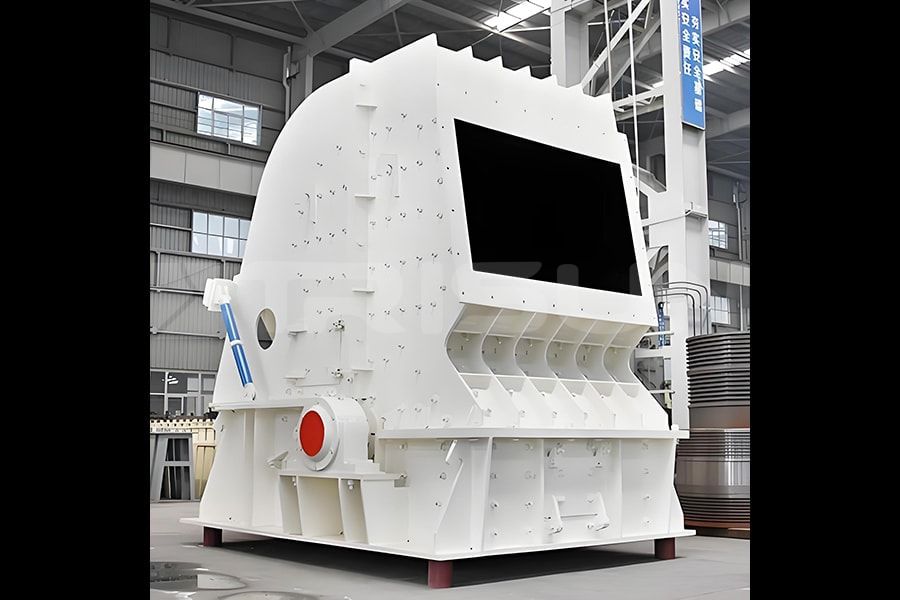
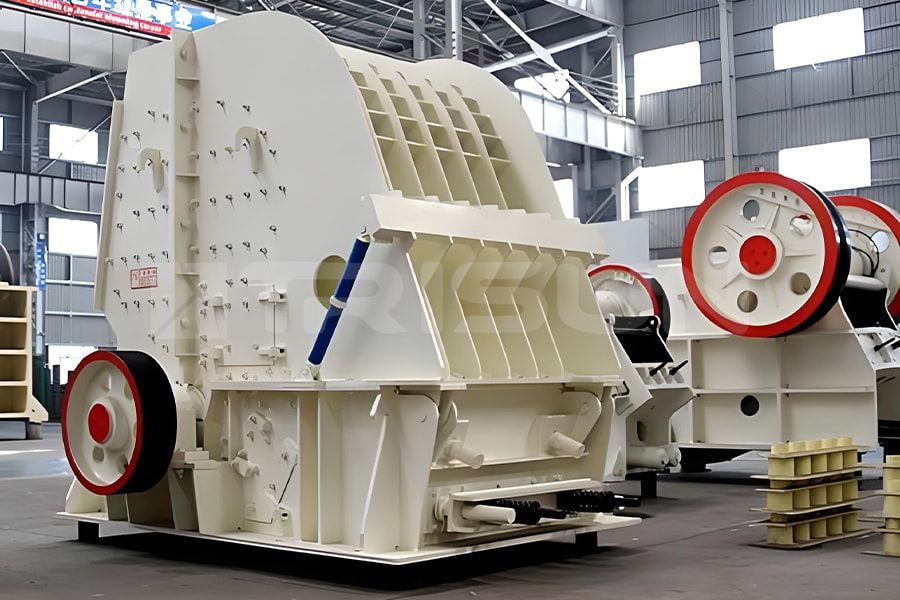
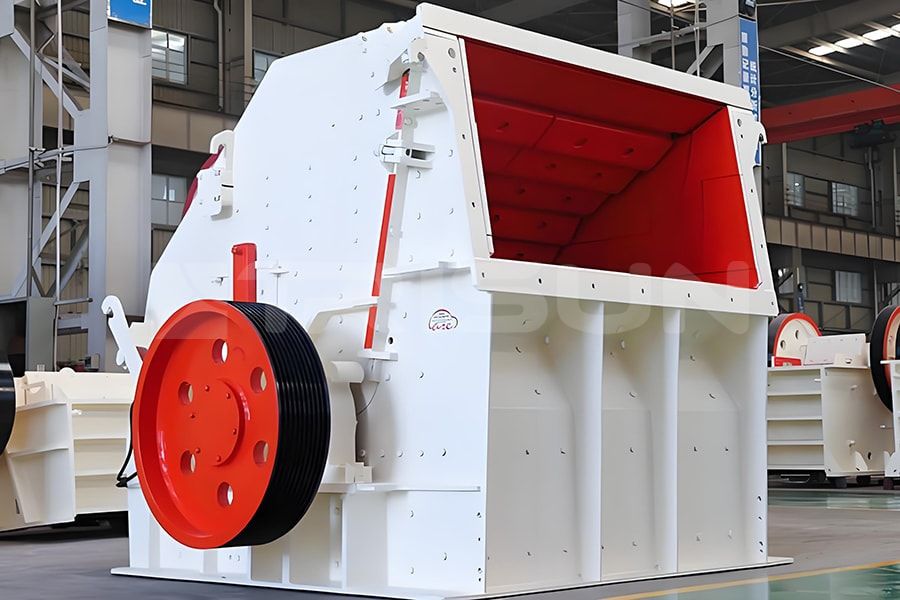
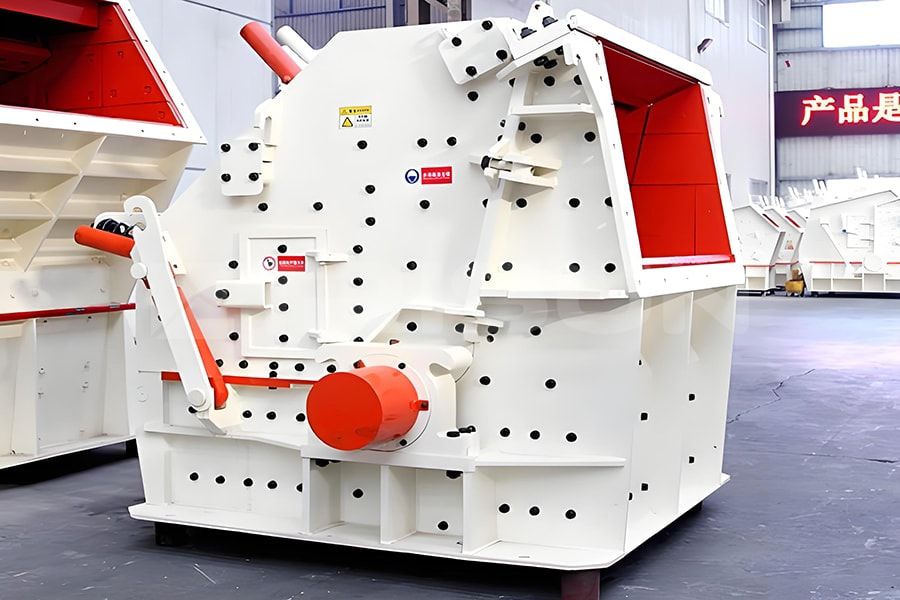
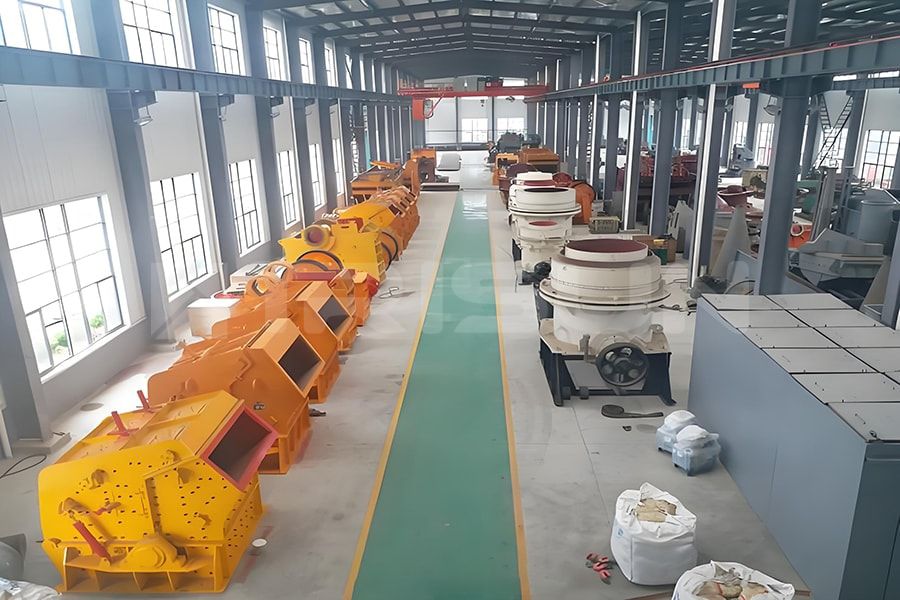
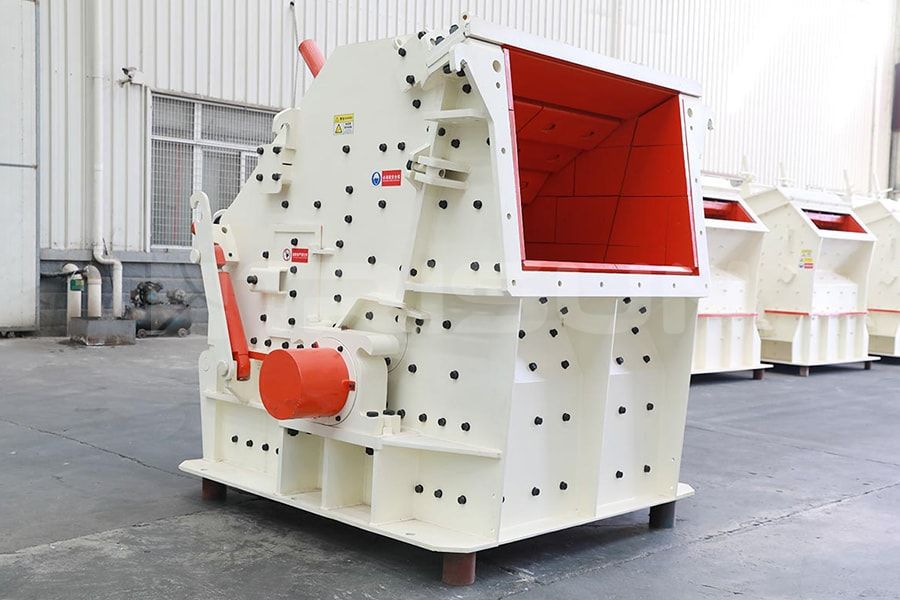
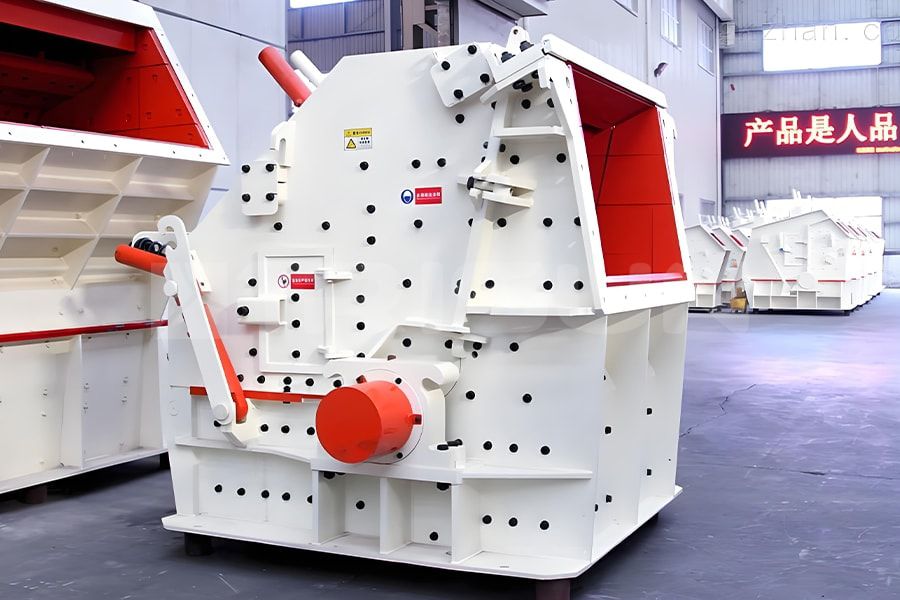
FAQ
What is the difference between jaw crusher and impact crusher?
As a primary crusher, the jaw crusher has a larger discharge opening, generally below 300mm (depending on the manufacturer and product model). As a secondary or tertiary crusher, the impact crusher has a smaller discharge size. It should be noted that due to different material properties, the discharge size of the crusher will also be different. The working principles of jaw crusher and impact crusher are different, so the way of crushing materials is different, and the particle shape of the discharged materials is also different. The jaw crusher uses extrusion crushing, and the final material shape is not ideal, but the impact crusher has very obvious advantages in this aspect. The particle shape of the impact crusher is mostly cubic, with less needle and flake content compared to the jaw crusher, and the quality is better.
What is the difference between hammer crusher and impact crusher?
1) Material hardness. Impact crushers can usually only crush materials with medium hardness and below, while hammer crushers can crush materials with higher hardness.
2) Crushing capacity. Although there are many models of hammer crushers and impact crushers, generally speaking, hammer crushers generally have greater processing capacity.
3) Aggregate quality. Although the hammer crusher feeds has a large crushing ratio and is formed at one time, the products have more pin-shaped flakes and are not uniform in size. It is not as good as the aggregates produced by the impact crusher, which are all cubic in shape and uniform in size.
What is the difference between cone crusher and impact crusher?
1) Working principle. The impact crusher is based on the operating principle of impact crushing. During operation, driven by the motor, the rotor in the impact crusher rotates at high speed. After the material enters, it is repeatedly hit and crushed between the hammer and the impact plate until the material is crushed to the required size, and then is discharged from the discharge opening. Cone crushers are based on the operating principle of lamination crushing. During operation, driven by the motor, the transmission shaft of the cone crusher and the cone perform a swing motion around a fixed point under the force of the eccentric sleeve. As a result, the mantle continuously moves toward the concave, and under the combined action of impact, extrusion, bending and other forces, the material is crushed in the crushing cavity.
3) Applicable materials. Impact crusher is mainly used to crush various coarse, fine and medium-hard materials with a side length less than 800mm and a compressive strength not exceeding 350MPa, as well as most mining stones with low iron content, such as: limestone, coal gangue, granite, bluestone, construction waste, cobblestones, river pebbles, basalt, iron ore, quartz stone, calcite, glass, concrete, cement clinker and certain metals ores, etc. Cone crusher is mainly used to crush various ores and rocks with medium and above medium hardness, and the feed size is 65-300mm. For example: calcite, limestone, granite, river pebbles, dolomite, bluestone, quartz stone, iron ore, basalt and other stones, construction waste, glass, cement clinker and some metal ores.
3) Discharge particle shape. The impact crusher not only crushes materials, but also has a certain function of reshaping the discharged particles. After processing, the material particles are cubic in shape, uniform in size, without tension and cracks, with low needle and flake content and high grade. The gradation is reasonable and the shape is beautiful. In comparison, although the crushing effect of the cone crusher is also good, it is still slightly inferior to the impact crusher in terms of shaping the discharged particles.
4) Economy. In sales, different series of impact crushers are sold at different prices, but the overall price is low and the purchase cost is low. The prices of different series of cone crushers are also different, but the overall price is high, and the price is not fixed, and the purchase cost is high. Although the purchase cost of the impact crusher is relatively low, because the impact crusher has many wearing parts, such as hammer, impact plate and other parts need to be replaced frequently, so the equipment wears out and depreciates quickly, and the later operation and maintenance costs are higher. Although the purchase cost of the cone crusher is relatively high, the service life of the wearing parts is relatively long, and there is no need to replace parts frequently. Therefore, the loss and depreciation of the equipment are slow, and the later operation and maintenance costs are low.