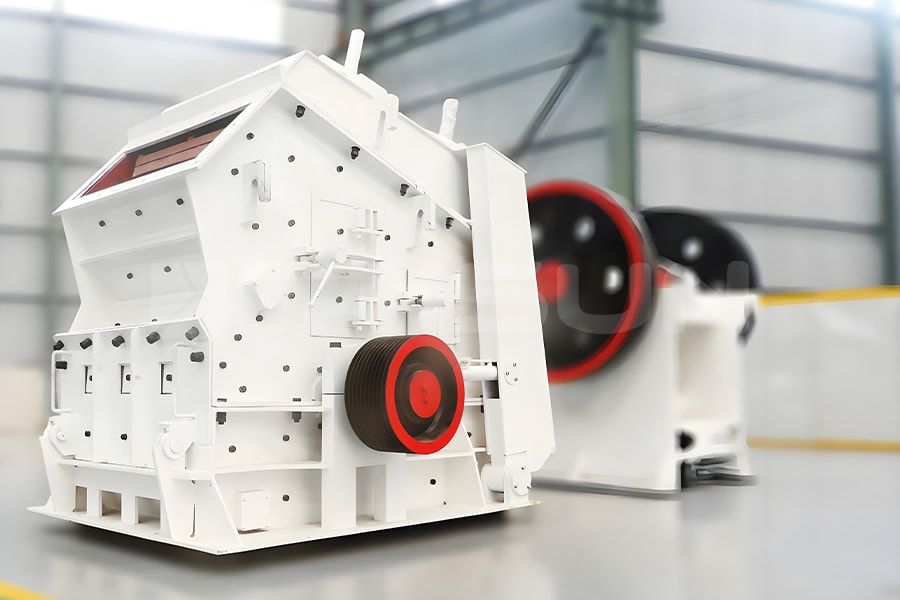
- Features & Properties
- Technical Specification
- Gallery
- Related Products
1. More effective in crushing materials with large moisture content. When the moisture content of the processed materials is too high, the feed chute and impact plate of the impact crusher can be equipped with heating devices to prevent the materials from sticking. The impact crusher does not need to be equipped with a bottom screen plate to effectively prevent clogging.
2. Applicable to materials with a wider range of hardness. The hammers of the impact crusher are firmly fixed on the rotor with mechanical clamping, and have a large moment of inertia when rotating with the rotor. Compared with the hammer crusher, the rotor of the impact crusher has greater momentum, which is suitable for crushing harder materials and consumes less energy.
3. Convenient and flexible to adjust the discharging size. The impact crusher can adjust the discharge size in a variety of ways, such as adjusting the rotor speed, adjusting the gap between the impact plate and the crushing cavity, etc. The gap adjustment can be mechanical or hydraulic, and the hydraulic adjustment can be easily completed through local operation buttons or a stroke control system.
4. Low wear of wearing parts and high metal utilization rate. The wear of the impact crusher's hammer only occurs on the side facing the material. When the rotor speed is normal, the material will fall to the surface of the hammer (the crushing surface), and the back and sides of the hammer will not be worn. The metal utilization rate of the impact crusher's hammer can be as high as 45%-48%.
5. Easier spare parts replacement and lower maintenance costs. Only a few hammers are installed on the rotor of the impact crusher. The hammers can be easily replaced with specially designed tools. It only takes one shift to replace a set of hammers.
Model | Maximum feeding size (mm) | Capacity (t/h) | Power(kw) | Dimensions (mm) |
PF1007 | 300 | 30-70 | 37-45 | 2330×1660×2300 |
CI1010 | 350 | 50-90 | 45-55 | 2370×1700×2390 |
CI1210 | 350 | 70-130 | 110 | 2680×2160×2800 |
CI1214 | 350 | 80-180 | 132 | 2650×2460×2800 |
CI1315 | 500 | 100-280 | 200 | 3180×2720×3120 |
CI1320 | 500 | 140-380 | 250 | 3220×3100×3120 |
CI1520 | 700 | 220-900 | 315-400 | 3959×3564×3330 |
CI1820 | 800 | 300-800 | 630-710 | 4400×3866×4009 |
Note: All features, functionality and other product specifications are subject to change without notice or obligation.
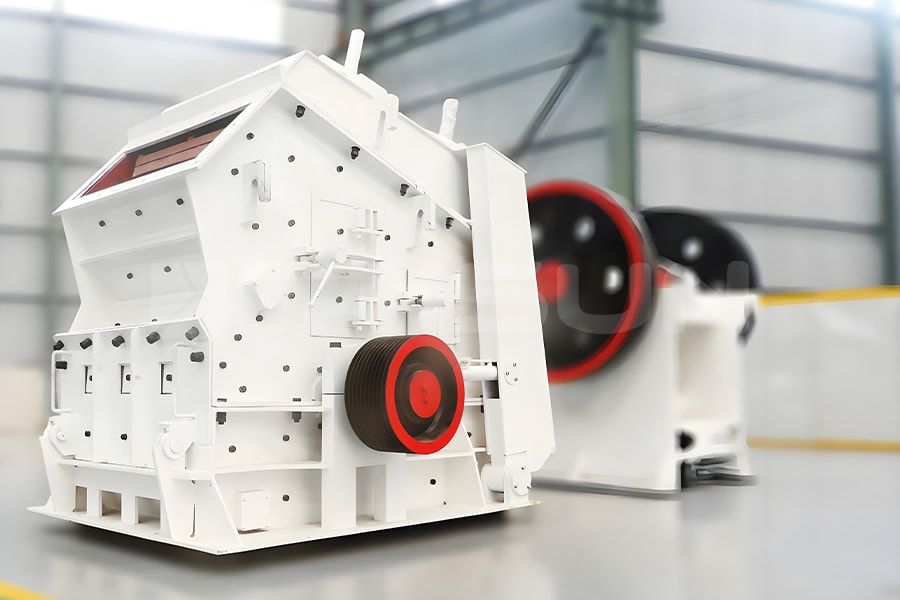
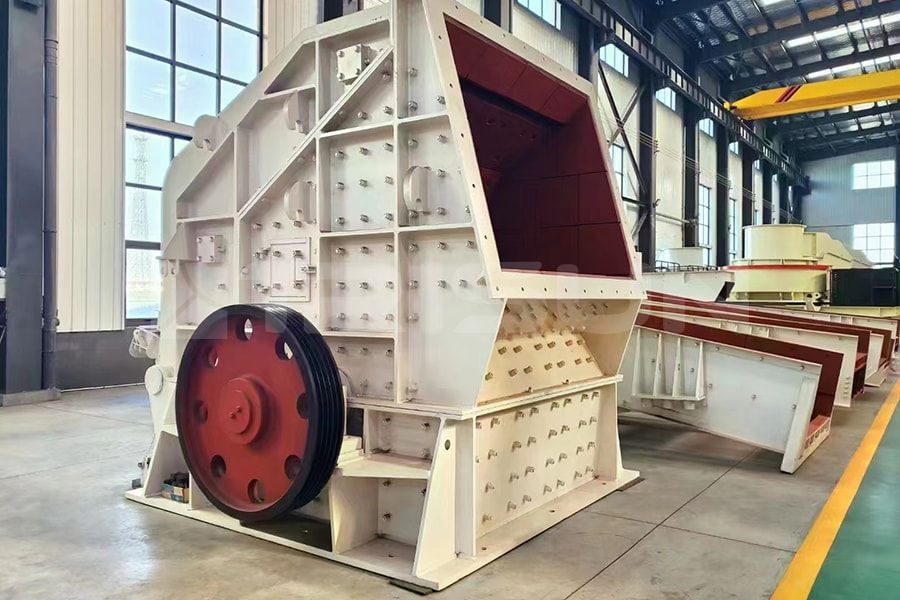
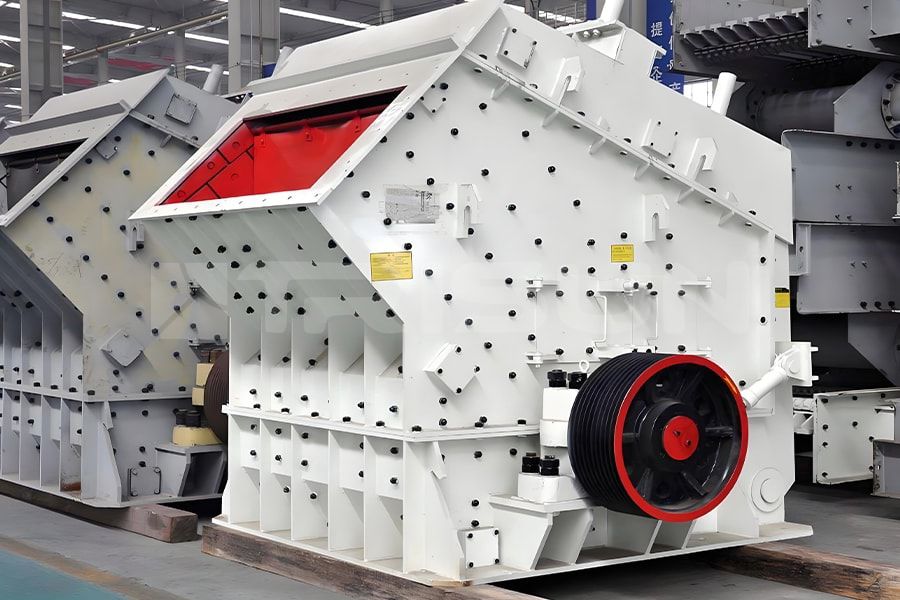
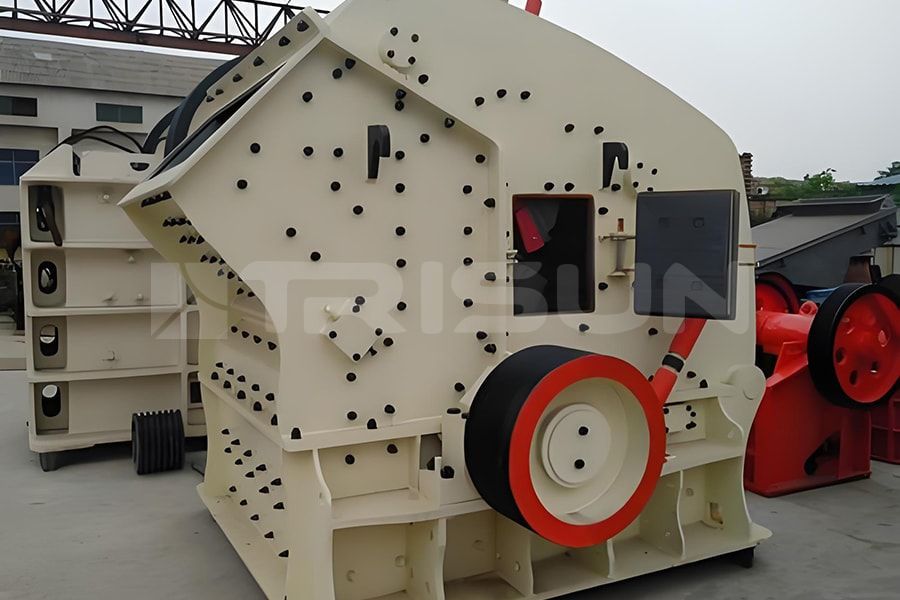
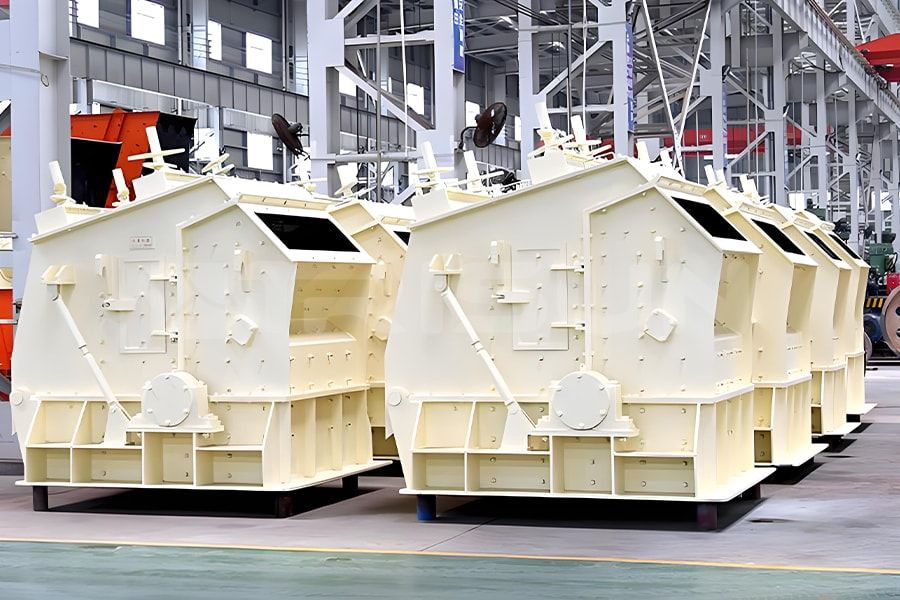
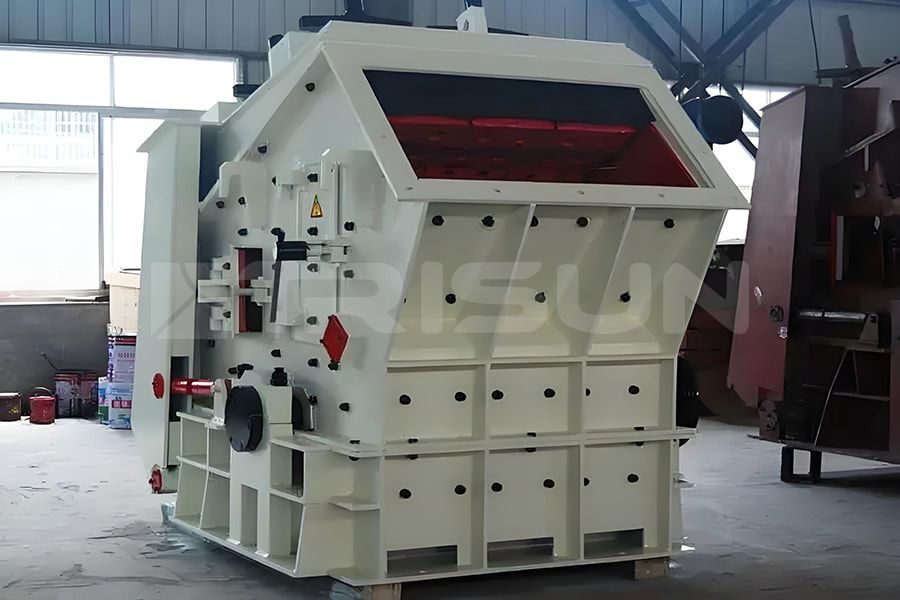
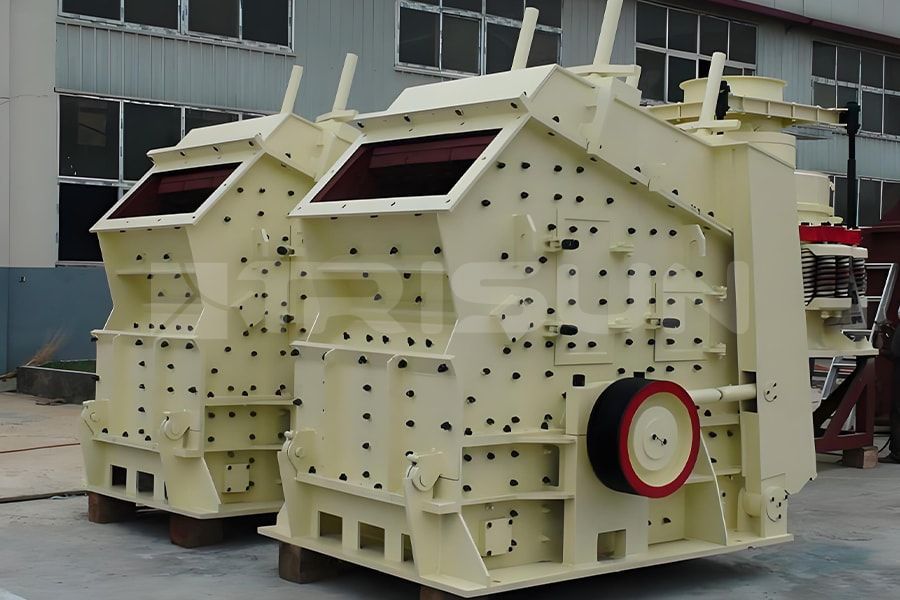
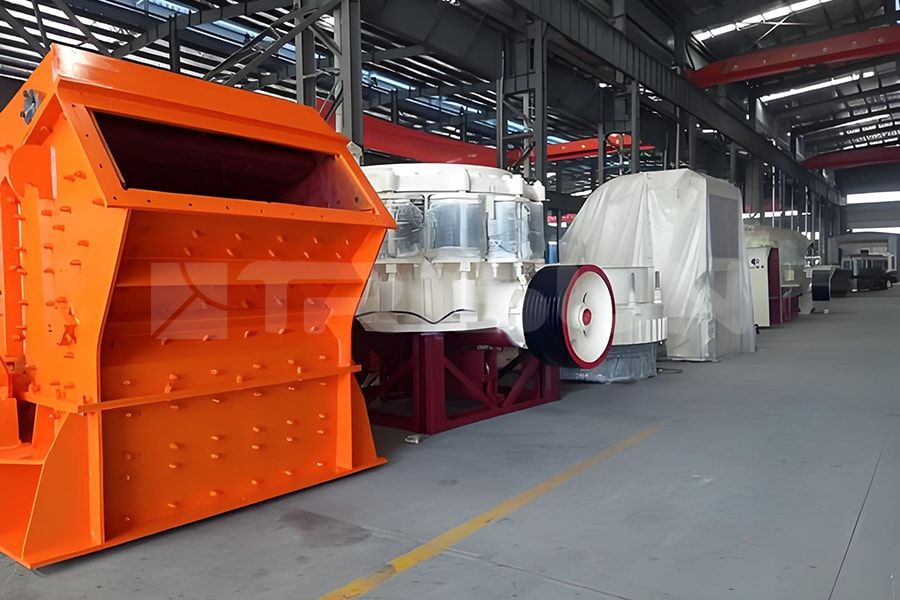
FAQ
Q: What are the safety precautions when working with an impact crusher?
A: 1) In order to protect the crusher while ensuring the productivity of the crusher and prevent wear and tear caused by the crusher during high-speed rotation, it is best to use the matching feeding equipment for continuous feeding. At the same time, the feeding should also be uniform along the length of the rotor.
2) When operating or adjusting the impact plate after installing the crusher, first ensure that the running part is not stuck or collided. The counterattack plate must not be adjusted during operation to avoid equipment accidents. The impact crusher cannot be used in reverse to avoid equipment damage or accidents such as material flying out.
3) When the machine is running, you should pay attention to the rotor bearings and vibration. If the temperature rise is too high or the machine vibration is too large, you should stop the machine quickly for inspection. The balance of the impact crusher rotor is also very important. During maintenance, attention should be paid to its static balance.
4) When replacing or turning the hammer for use, the quality accuracy of the hammer must meet the standards. Usually, the mass difference between each hammer cannot exceed the standard ±0.5kg. After assembly and charging, check the static balance of the rotor. After stopping at any position, it cannot rotate more than 1/10 of the circle.
Q: What are the preparations before starting the impact crusher?
A: 1) Check whether there is an appropriate amount of lubricating oil (grease) in the bearing;
2) Check whether the movable joints of each accessory are stuck, and if found, apply an appropriate amount of grease in time;
3) Check that all fasteners such as bolts are fully tightened;
4) Check whether there are any debris, iron wire, iron slag, etc. that are not easily crushed inside the crusher.
5) Check whether the gap between the impact plate and the rotor plate hammer meets the crushing requirements;
6) Turn the rotor manually and observe whether the rotation is normal. There should be no bruises on the hammer or other parts.
Q: How to start the impact crusher?
A: After careful inspection, make sure that every component of the equipment is in normal condition before starting the crusher; Once abnormal phenomena are discovered after startup, the power should be turned off immediately. The cause must be identified and eliminated before restarting.
Q: How to feed the impact crusher?
A: The impact crusher must use a feeder to feed materials evenly and continuously, so that the materials can be evenly distributed over the entire length of the working part of the rotor. The benefits are: It ensures production capacity and avoids material clogging, greatly extending the service life of the crusher. The electrical control system of the feeder should be interlocked with the electrical control system of the crusher. The advantage is that when the crusher is overloaded, the feeder can automatically cut off the power supply and stop feeding.
Q: How should the impact crusher be stopped?
A: Before stopping the crusher each time, the material feeding needs to be stopped first. After the materials in the crusher cavity are completely crushed and cleaned, the power supply of the crusher can be cut off to stop it.