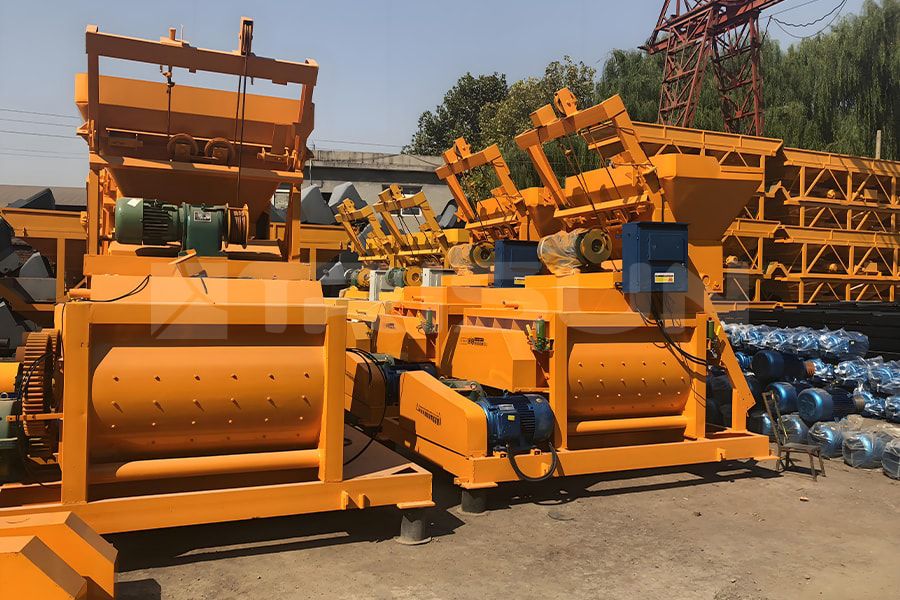
- Features & Properties
- Technical Specification
- Gallery
- Related Products
1. High efficiency: Usually, it is equipped with a JS forced twin-shaft concrete mixer, which can produce plastic, dry-hard concrete and other types of concrete with high production efficiency.
2. Good quality: For key components, better raw materials provided by international manufacturers are selected (such as mixing arms, blades, liners, spindles, etc.).
3. high accuracy: It adopts the latest designed weighing system with buffer device and automatic compensation with microcomputer control, digital display and other control technologies.
4. Low noise: The entire concrete production process, from batching to mixing and discharging, is in a fully enclosed environment with less dust, low noise, and environmentally friendly.
5. Good effect: The liners and blades are made of high-chromium wear-resistant cast iron, with reasonable angle, fast and uniform mixing, long service life, and easy maintenance.
Model | HZ25/30 | HZ35/45 | HZ50/60 | YHZ75/90 | YHZ100/120 | YHZ150/180 |
Theoretical maximum capacity | 30m³/h | 45m³/h | 60m³/h | 90m³/h | 120m³/h | 180m³/h |
Mixer capacity | 0.5m³/batch | 0.75m³/batch | 1m³/batch | 1.5m³/batch | 2m³/batch | 3m³/batch |
Batcher | PLD800 | PLD1200 | PLD1600 | PLD2400 | PLD3200 | PLD4800 |
Total power | 50-60kW | 61-72kW | 84-106kW | 127-145kW | 175-210kW | 215-260kW |
Note: All features, functionality and other product specifications are subject to change without notice or obligation.
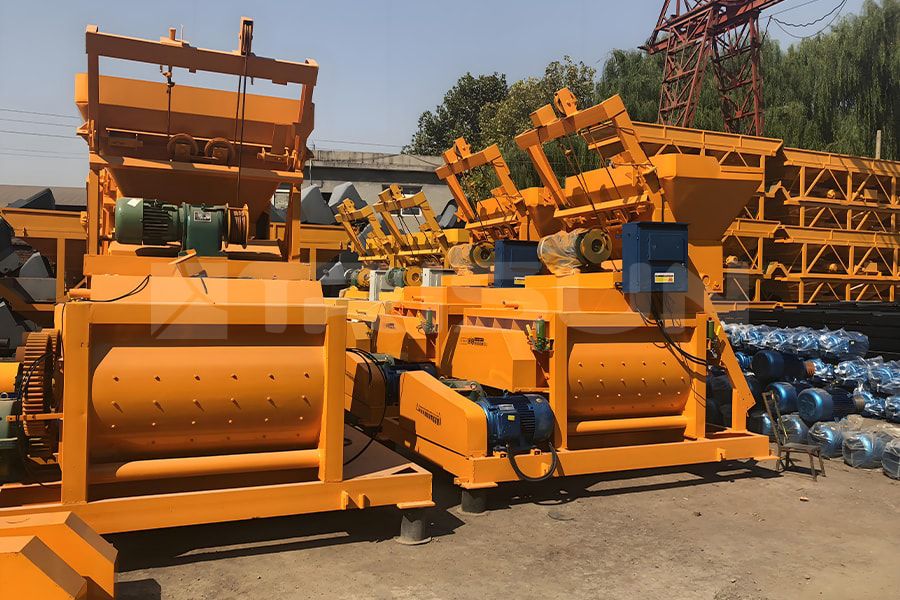
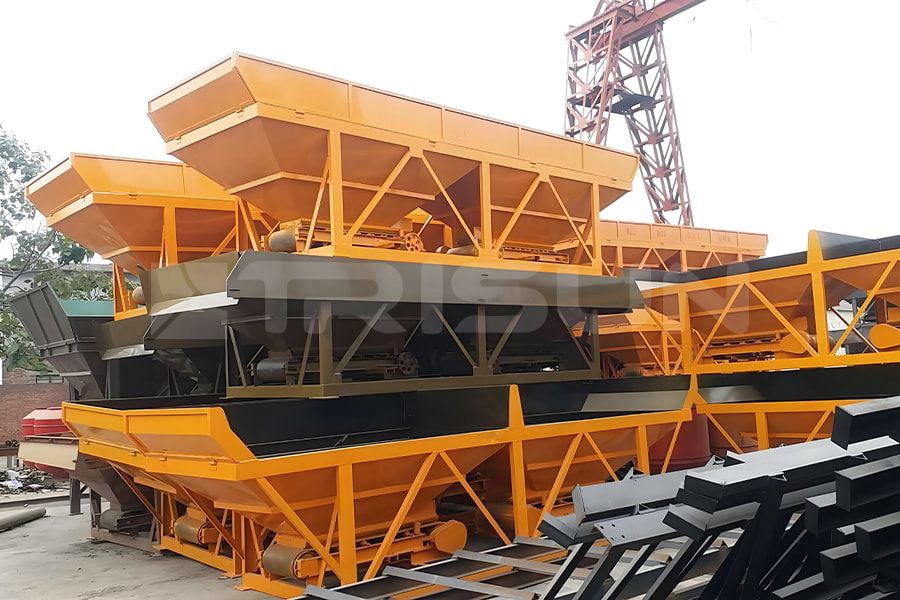
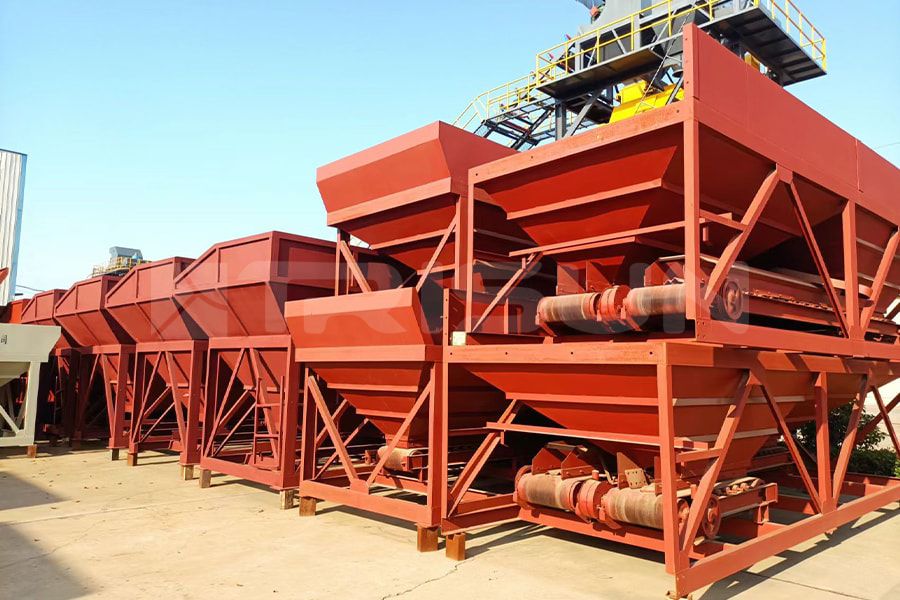
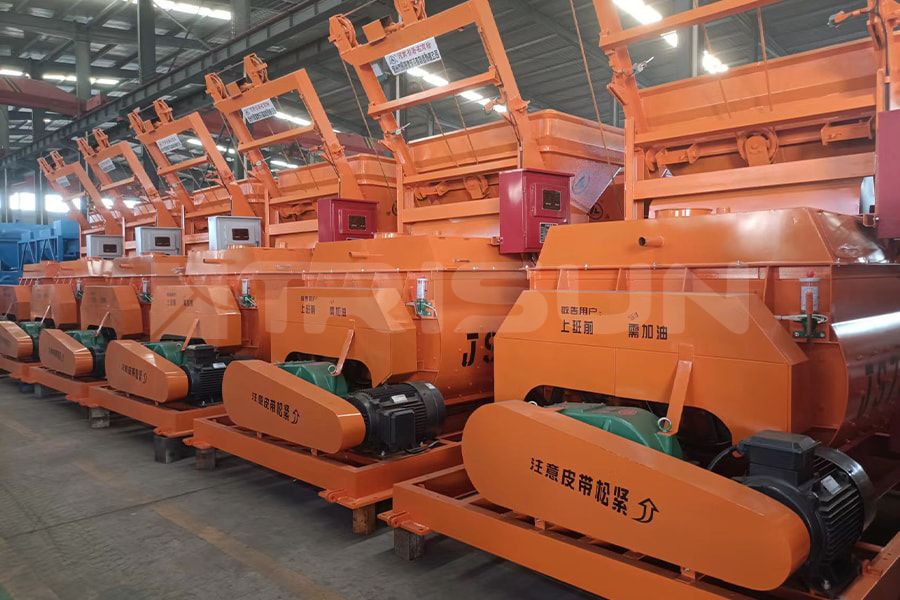
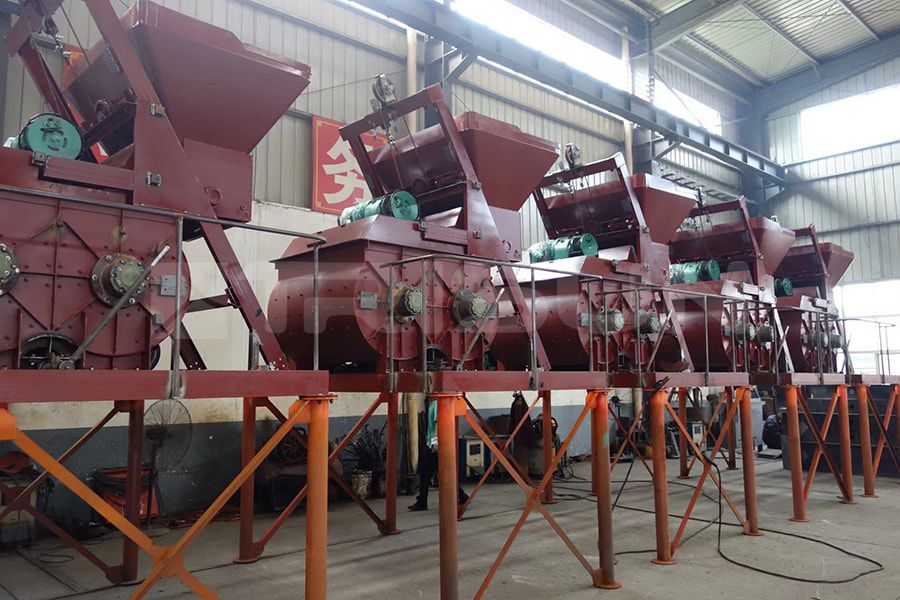
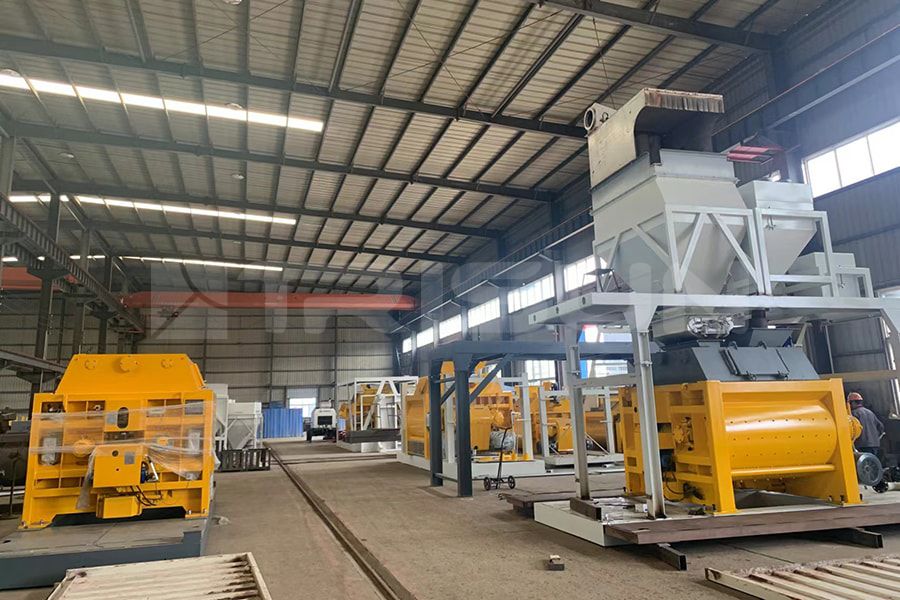
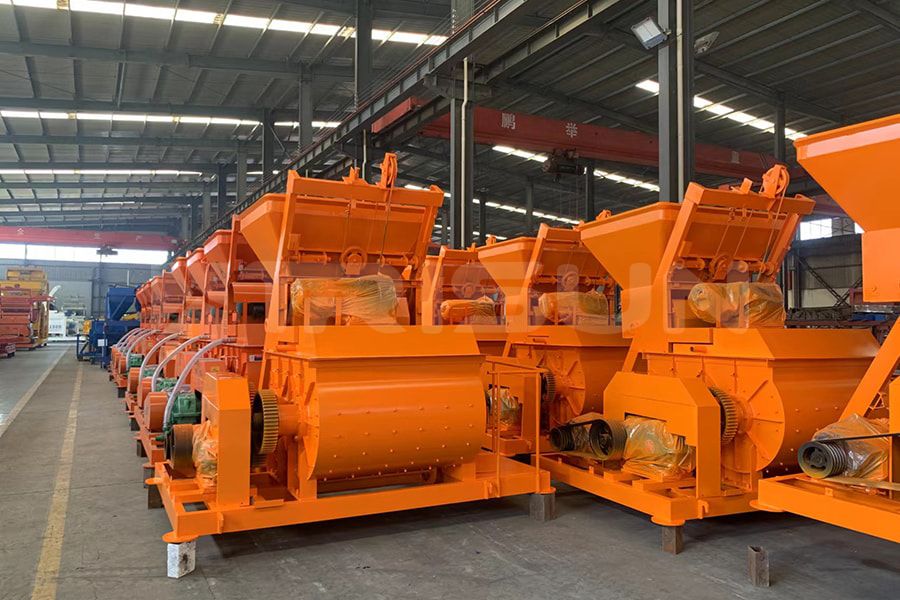
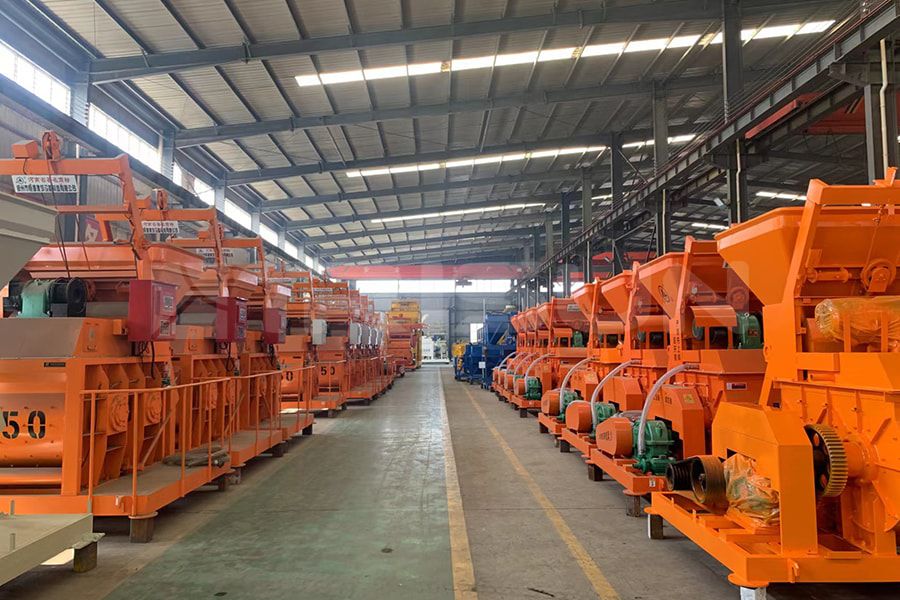
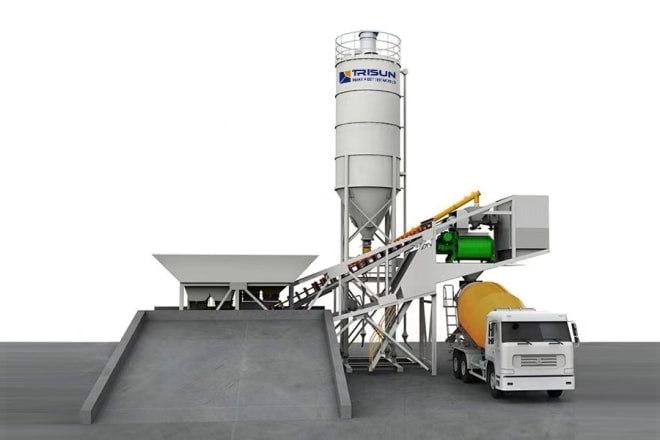
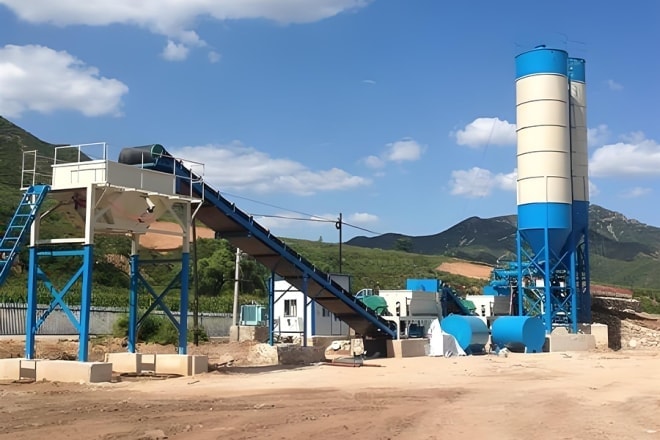
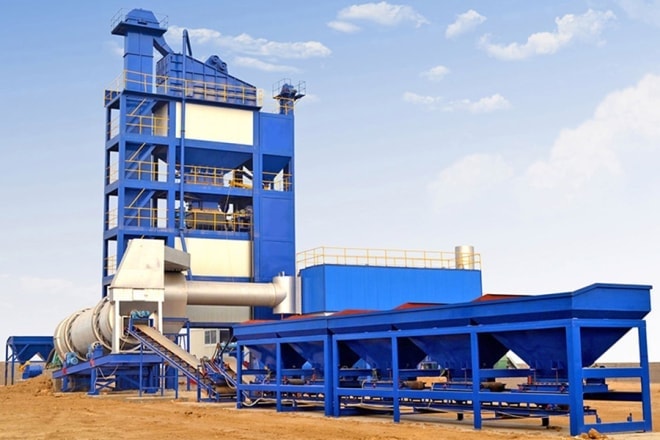
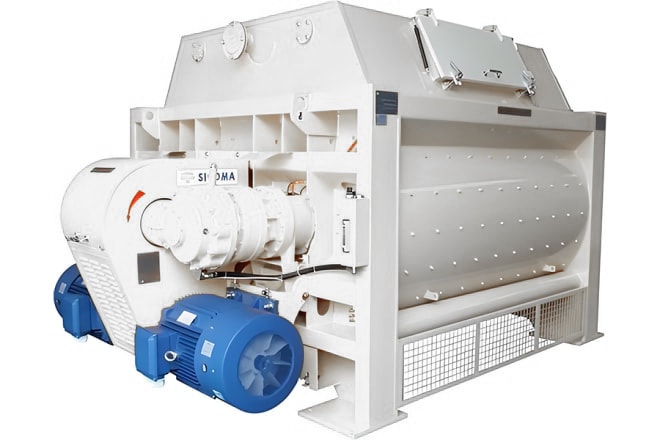
FAQ
Q: What are the operating procedures and precautions for concrete batching plants?
A: 1) It needs to be installed firmly.
2) It should be checked whether it has been commissioned before formal work.
3) During the production process, supporting equipment cannot be overloaded.
4) During operation, if there is a sudden power outage or failure, the materials in the mixing drum should be cleaned manually and then inspected or repaired.
5) If the operator needs to enter the mixer for cleaning or maintenance, the switching power supply should be strictly controlled.
Q: Why does a concrete plant use a forced mixer instead of a gravity mixer?
A: 1) Mixing principles. When the forced concrete mixer is working, the drum remains stationary, the mixing shaft rotates, and the mixing arm drives the mixing blade to continuously forcefully mix the materials in the drum; When the gravity concrete mixer is working, the mixing drum rotates. The mixing blades installed in the mixing drum make the materials continuously rise and lift. After reaching a high place, the materials fall downwards by their own gravity and produce axial movement.
2) Mixing cycle. Comparing these two mixers, the mixing effect of the forced mixer is more intense. It generally only takes 30-60 seconds to mix the materials into homogeneous concrete. For special concrete, the mixing cycle may be longer; However, the mixing cycle of a gravity mixer needs to be doubled or even longer.
3) Energy consumption.
Under the same mixing capacity, the driving power of the forced mixer is greater than that of the gravity mixer, and the corresponding total installed power of the mixer and power distribution facilities need to be increased. However, due to its relatively short mixing cycle, the unit energy consumption of producing concrete has not increased much.
Q: What are the safety production precautions for concrete plants?
A: 1) Before starting work, all fasteners and wire ropes must be inspected and tightened in accordance with the operation manual, and lubricating oil must be added to the parts that need lubrication.
2) When the mixing plant is working, no one is allowed to touch the transmission device, or open the mixer cover and other protective facilities.
3) When the mixing plant is working, no one is allowed to stand in the loading and unloading areas.
4) When the mixer is working, it is strictly prohibited to stop it in the middle. In case of power outage, the discharge door should be opened immediately to drain the concrete in the main mixer to prevent condensation.
5) The reliability of switches, buttons, indicator lights and other electrical equipment should be checked regularly according to the requirements of the operation manual.
6) All electrical pipelines should be properly protected to prevent them from being crushed or bruised during work.
7) It is strictly prohibited to change the working mode while the system is running. If you need to change it, please follow the operating instructions.
8) When the mixing plant is inspected, especially when inspecting the main mixer, the main power supply must be disconnected and a dedicated person must be assigned to take care of it.
9) Both the power system and the control equipment have high requirements for power supply, and the voltage fluctuation of the working power supply should be controlled within the range of ±5%.
10) If an unexpected situation occurs, press the emergency stop button immediately, disconnect the main power supply, and then restart after confirming that the fault has been eliminated.