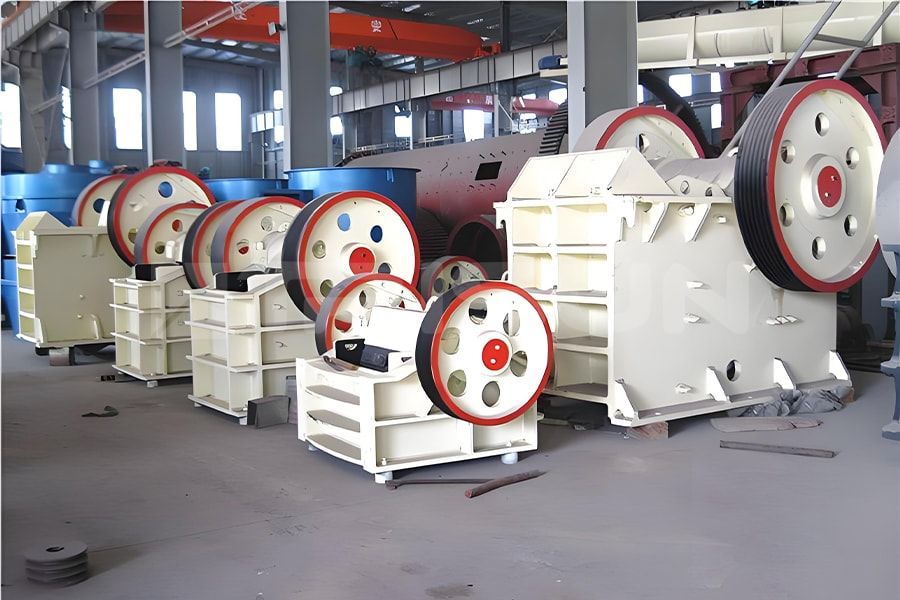
- Features & Properties
- Technical Specification
- Gallery
- Related Products
1. Simple structure and strong impact resistance. It adopts cast steel welded frame, which has simple structure, reliable operation and low use and maintenance costs.
2. Easy to adjust, suitable for different needs. The output can be flexibly adjusted according to needs through gaskets. The adjustment range is large and can meet different output requirements.
3. High-quality materials, precision processing, stable and durable. The jaw plates and lining plates are made of high manganese steel, the toggle plate is made of gray iron, and the eccentric shaft is made of high-strength forged steel. They are made through precise machining, heat treatment and flaw detection. They have sufficient stiffness and strength to ensure the stability and durability of machine operation.
4. Low noise, low dust, energy-saving and environmentally friendly. It adopts high wear-resistant alloy bearings and centralized lubrication system, which has low noise, high efficiency, relatively uniform output size and less dust, which reduces noise pollution and air pollution.
5. Large crushing ratio and large processing capacity. The crushing cavity is deep and has no blind area, which improves the feeding capacity and processing capacity. The optimized crushing cavity can meet larger material feeding requirements, and the extended toothed jaws increase the effective depth of the crushing cavity.
Model | Input size (mm) | Maximum feeding size (mm) | Output adjustable range (mm) | Capacity (t/h) | Power(kw) | Dimensions (mm) |
PE250×400 | 250×400 | 200 | 20-50 | 5-20 | 15 | 1430×1310×1340 |
PE400×600 | 400×600 | 350 | 40-100 | 15-60 | 30-37 | 1700×1732×1650 |
PE500×750 | 500×750 | 425 | 50-100 | 40-110 | 45-55 | 2035×1921×2000 |
PE600×900 | 600×900 | 480 | 65-160 | 90-180 | 55-75 | 2290×2206×2370 |
PE750×1060 | 750×1060 | 630 | 80-140 | 110-320 | 90-110 | 2655×2302×3110 |
PE900×1200 | 900×1200 | 750 | 95-165 | 220-450 | 110-132 | 3800×3166×3045 |
PE1000×1200 | 1000×1200 | 850 | 200-300 | 280-560 | 110-160 | 5350×4280×3050 |
PE1200×1500 | 1200×1500 | 1020 | 150-300 | 400-800 | 160-220 | 6380×5310×3710 |
PE1500×1800 | 1500×1800 | 1200 | 210-360 | 520-1100 | 280 | 7460×6235×4249 |
PEX150×250 | 150×250 | 125 | 10-40 | 1-3 | 5.5 | 896×745×935 |
PEX150×750 | 150×750 | 125 | 18-48 | 5-16 | 15 | 1200×1500×1200 |
PEX250×750 | 250×750 | 210 | 25-60 | 15-30 | 22-30 | 1667×1545×1020 |
PEX250×1000 | 250×1000 | 210 | 25-60 | 15-50 | 30-37 | 1550×1964×1380 |
PEX250×1200 | 250×1200 | 210 | 25-60 | 20-60 | 37-45 | 2192×1900×1950 |
PEX300×1300 | 300×1300 | 250 | 20-90 | 30-90 | 55-75 | 1750×2320×1724 |
Note: All features, functionality and other product specifications are subject to change without notice or obligation.
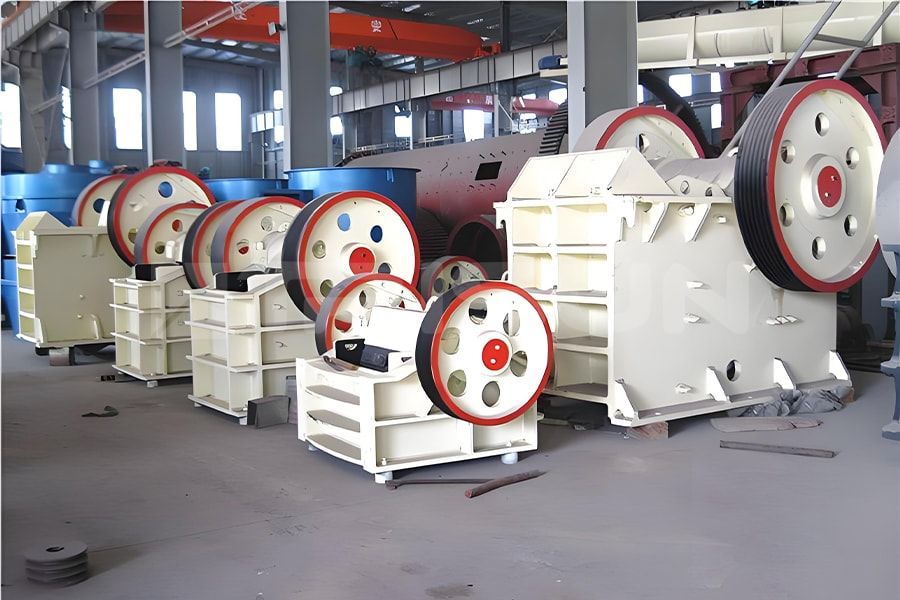
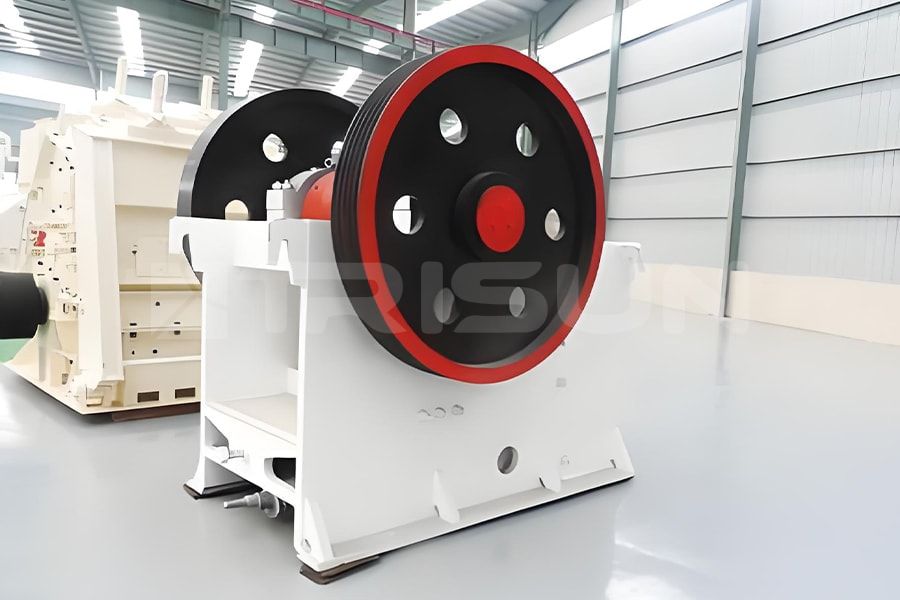
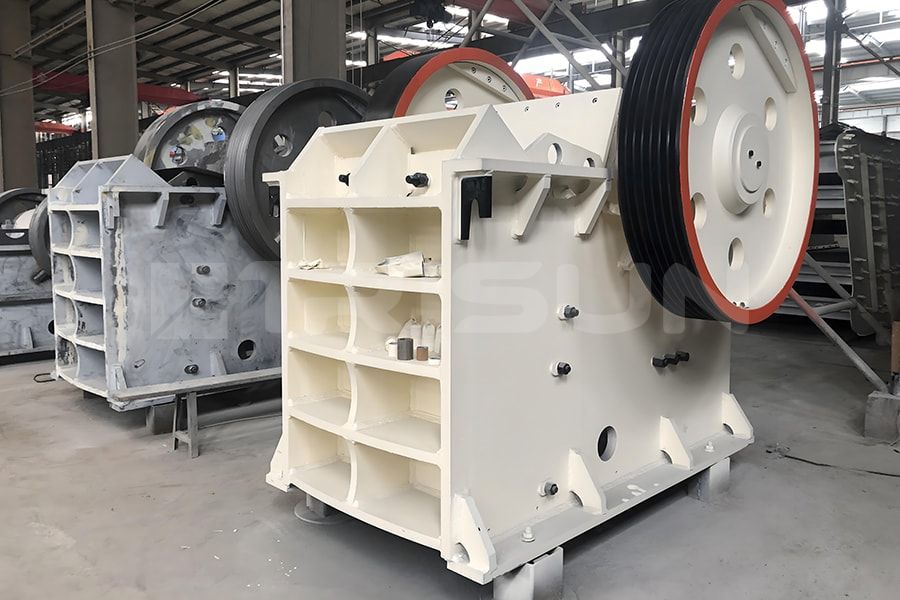
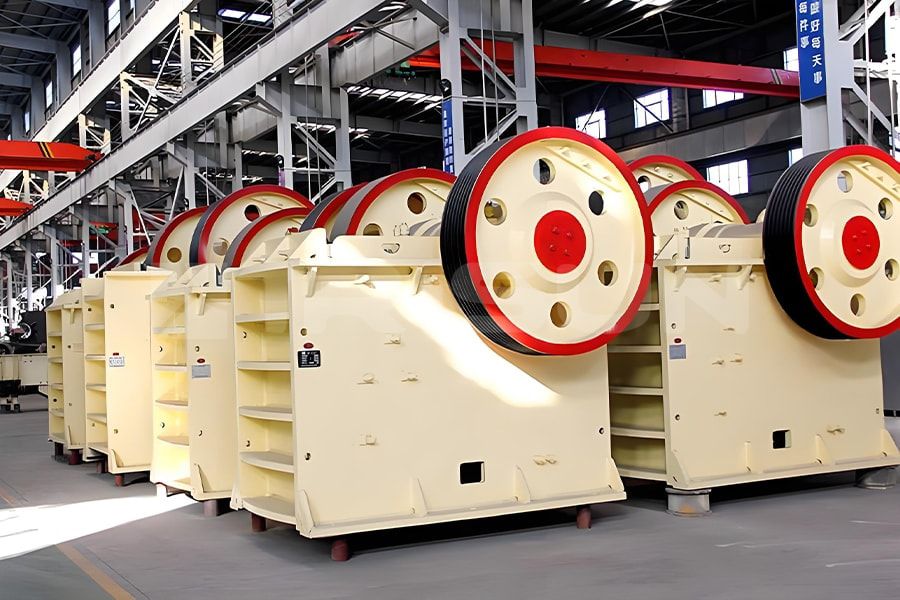
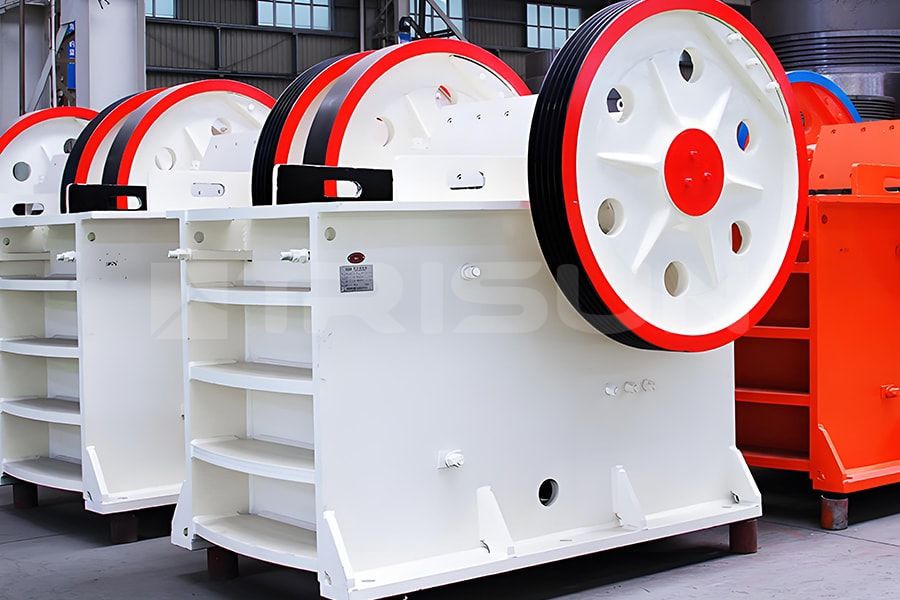
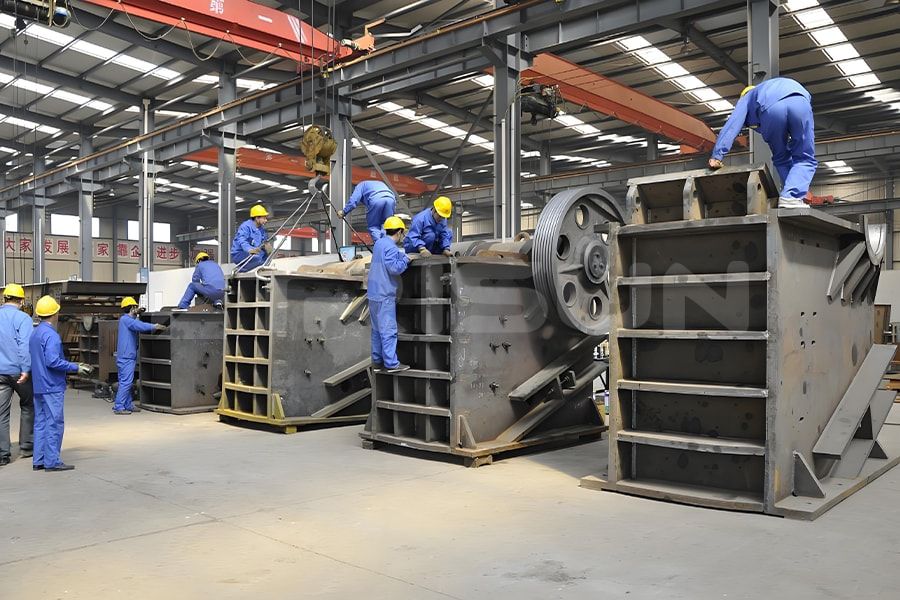
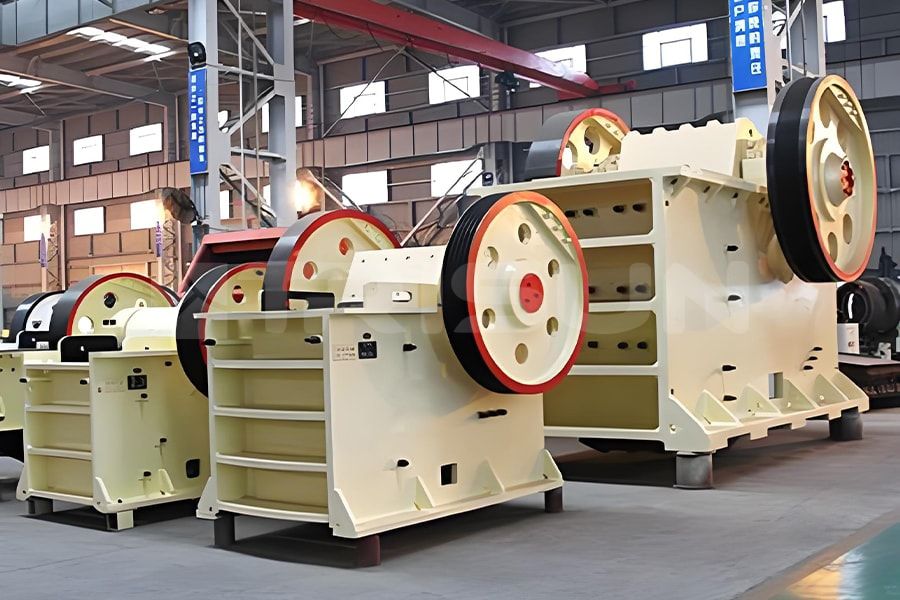
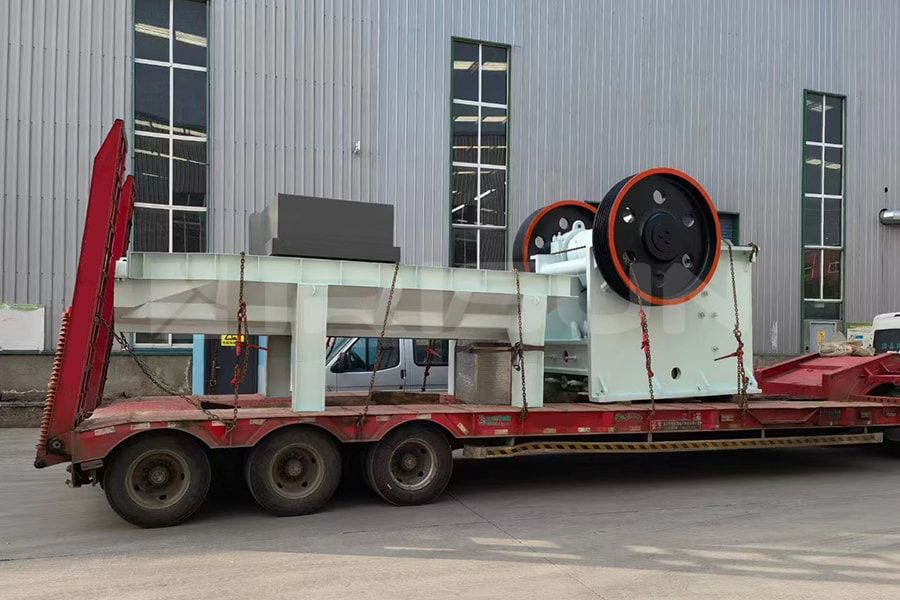
FAQ
Q: What is the structural composition of the PE jaw crusher?
A: PE jaw crusher is mainly composed of frame, eccentric shaft, pulley, flywheel, movable jaw, side plate, toggle plate, toggle plate seat, gap adjustment screw, return spring, fixed jaw plate and movable jaw plate, etc. , in which the toggle plate also acts as a fuse.
In the process of crushing huge stones into small, the primary crusher is usually called the main crusher. When feeding the jaw crusher, the material is poured into the crushing cavity containing the teeth from the top. The jaw teeth push out the material with great force and break it into smaller stones. What supports the movement of the movable jaw is an eccentric shaft that runs through the frame. Eccentric motion is usually produced by flywheels and pulleys fixed at both ends of the shaft. The support bearings of flywheels and eccentric shafts often use spherical roller bearings. The working environment of the bearings is extremely harsh and must withstand huge impact loads, abrasive sewage and high temperatures. Despite the extremely harsh working environment, the jaw crusher still needs to work very reliably, which is a key part of ensuring production efficiency.
Q: What does the testing of PE jaw crusher include?
A: After users purchase a PE jaw crusher, in order to ensure its production efficiency, they should regularly inspect and repair the equipment, which mainly includes the following aspects:
1) First, check the flatness of the surface of the PE jaw crusher by hand to see if there are any concavities and convexities. If so, inform the technicians to make modifications.
2) Any substandard parts found should be replaced promptly.
3) Before starting the machine, check whether the crusher is installed properly; during no-load operation, check the sealing, jamming, friction, and impact of the equipment.
4) Check whether the machine has obvious shaking and whether there is excessive noise. Ensure that the shaking does not exceed 0.5mm and the noise is controlled within 85db.
Q: What are the maintenance points of PE jaw crusher?
A: 1) During storage or seasonal shutdown, the crusher should be run at least once in a while to ensure that the bearings are properly lubricated. If necessary, grease the bearings in time.
2) If the flywheel has been removed from the eccentric shaft, the contact surface between the flywheel and the shaft should be coated with anti-corrosion agent.
3) When it is taken out of storage, the painting condition should be checked and repaired according to the situation. Before assembling the crusher, preservatives should be removed from all contact surfaces.
4) The PE jaw crusher and its disassembled parts should be stored on a stable stand to avoid contact with the ground.