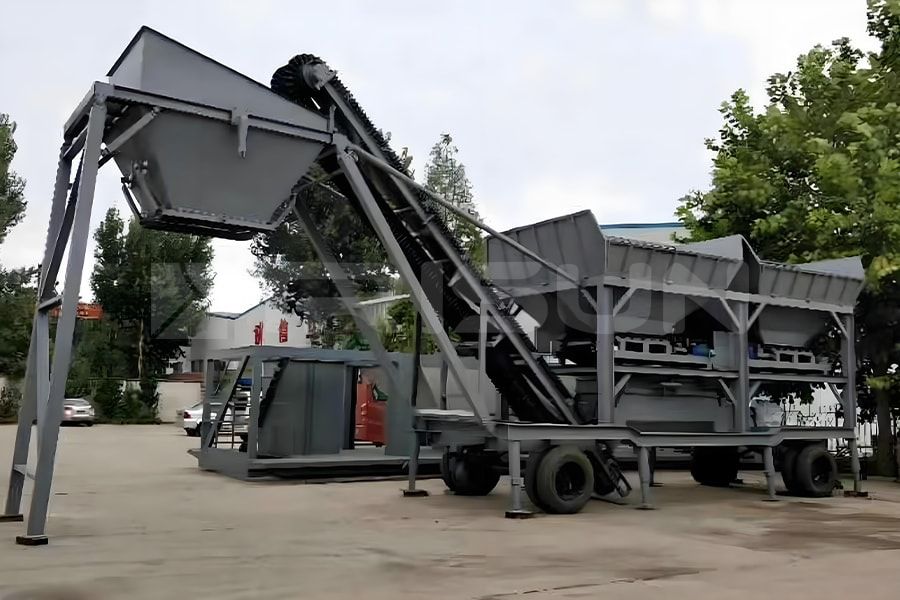
- Features & Properties
- Technical Specification
- Gallery
- Related Products
1. It has manual, semi-automatic and fully automatic control functions, and can realize mutual switching. It adopts centralized control by industrial computer, and the dynamic process operation interface is beautiful and intuitive.
2. The motor is controlled by PLC and can be started and stopped with one click; it has fault detection and alarm functions; each weighing signal is directly input into the PLC to prevent interference and improve response speed; each material can automatically start and stop according to the process sequence to ensure that the material enters the mixer synchronously;
3. The safety of electricity use, production, and maintenance considered, and it takes measures such as repeated grounding of equipment and installation of obvious safety signs to fully ensure equipment and personal safety;
4. The cement silo has batching level display and arch breaking device; the water tank has upper and lower limit alarm indications and has the function of automatically starting and stopping the external water supply pump; the aggregate silos are equipped with wall vibrators and have material shortage alarms and self-starting silo vibrations. A vibrator is installed in the finished product silo to prevent material accumulation in the corners when discharging materials;
5. It has automatic zero calibration point and weighing coefficient; can display and print the set values and actual values of each system parameter; print real-time reports and historical reports (including date, time, accumulated production hours, accumulated material consumption and other production reports);
6. The control room is container-type, spacious and bright, well sealed and has a wide field of vision; it has functions such as moisture-proof, dust-proof, heat insulation, sound insulation, etc.; the room is equipped with air-conditioning of corresponding capabilities; instruments, alarm devices, emergency control devices, keyboards, control display, etc. are arranged reasonably according to process sequence and ergonomic requirements.
Model | Nominal capacity | Control mode | Weighing accuracy | Total power | Total weight | ||
Aggregate | Powder | Water | |||||
YWB120 | 120t/h |
Automatic/manual |
±2% | ±1% | ±1.5% | 65kw | 24t |
YWB200 | 200t/h | 95kw | 30t | ||||
WB300 | 300t/h | 105kw | 32t | ||||
WB400 | 400t/h | 120kw | 34t | ||||
WB500 | 500t/h | 155kw | 42t |
Note: All features, functionality and other product specifications are subject to change without notice or obligation.
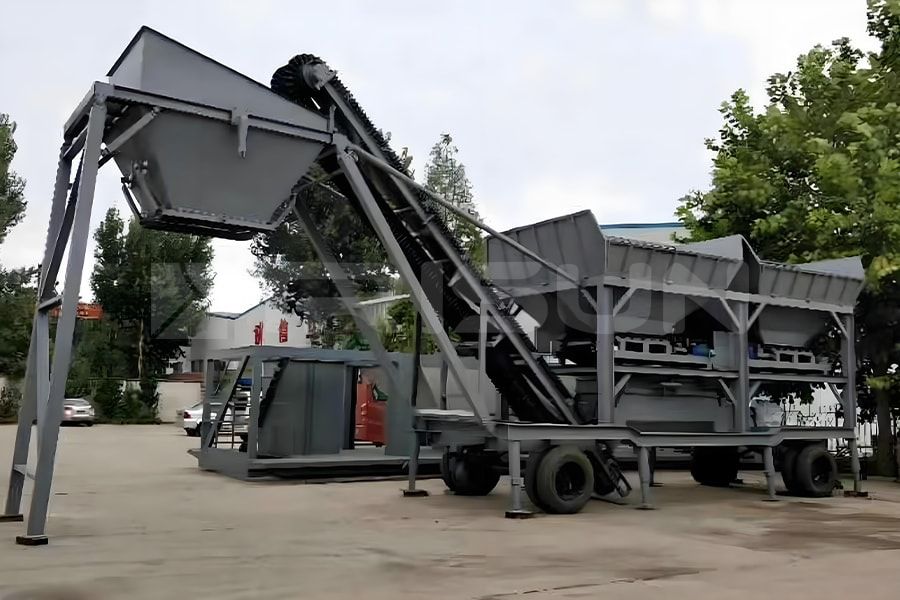
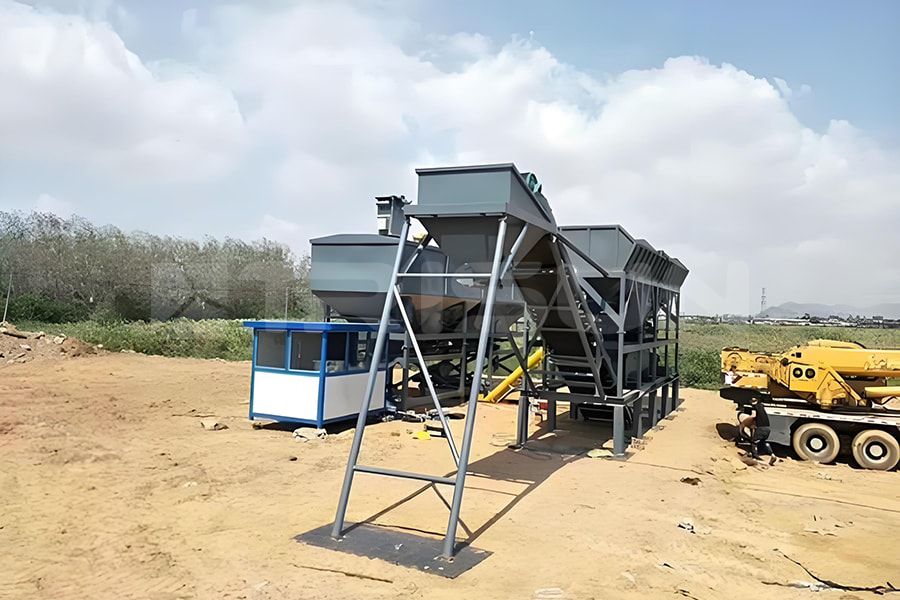
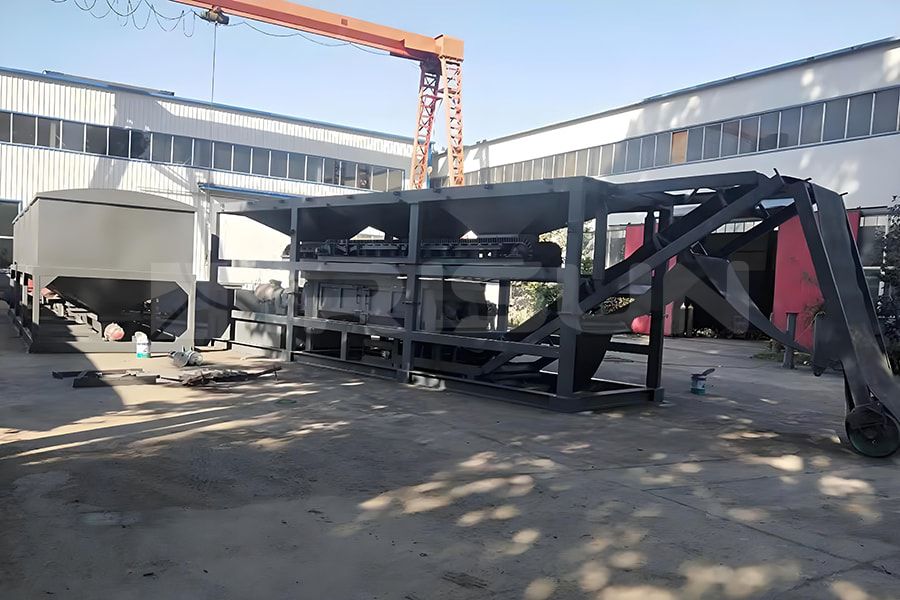
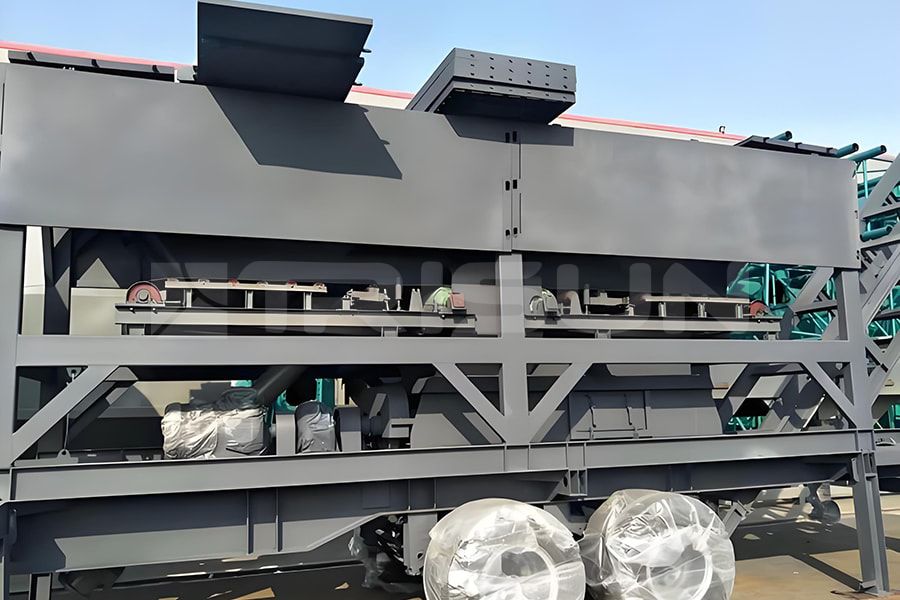
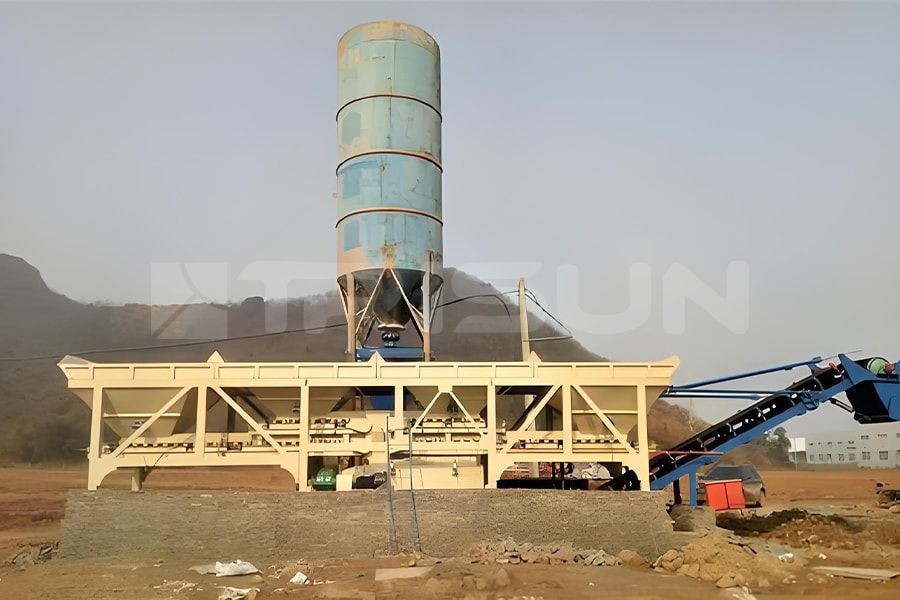
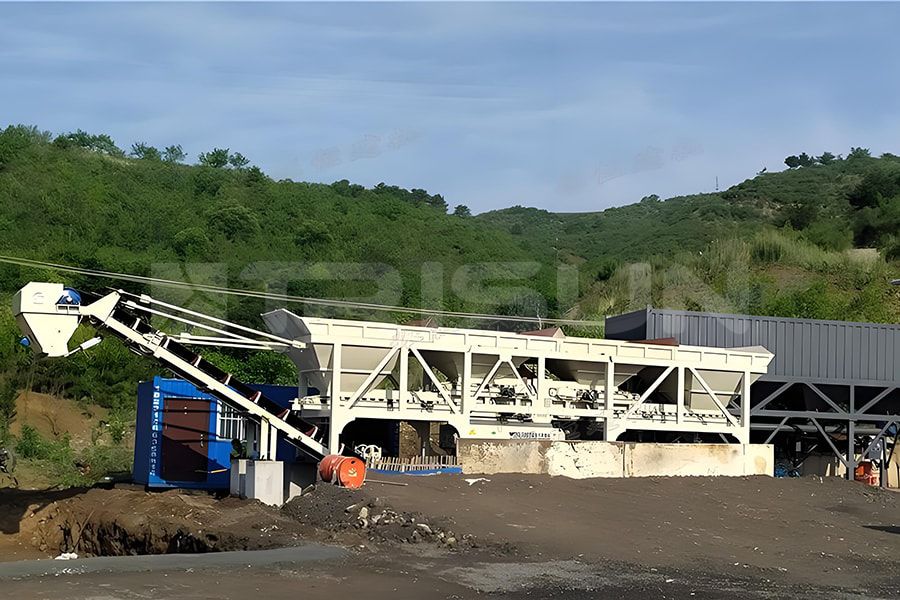
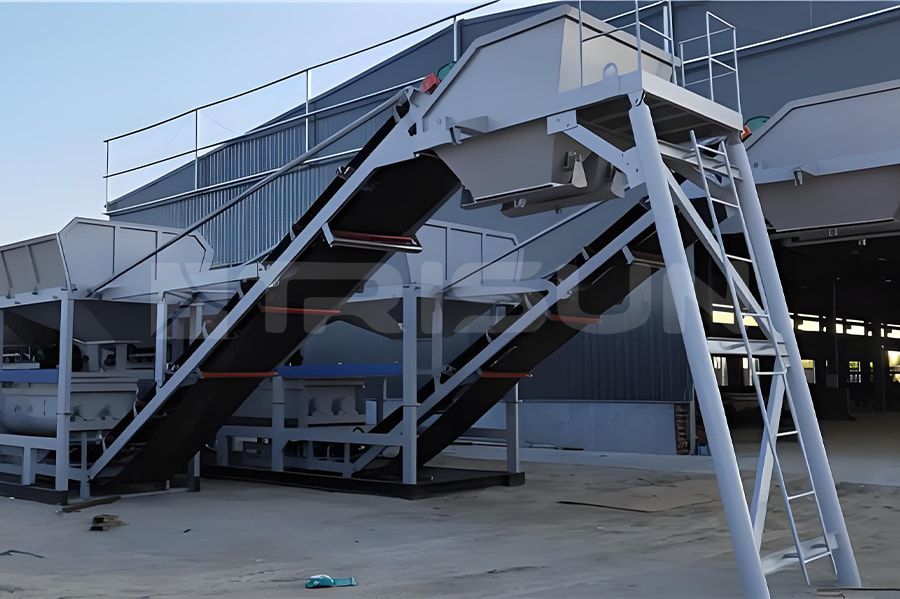
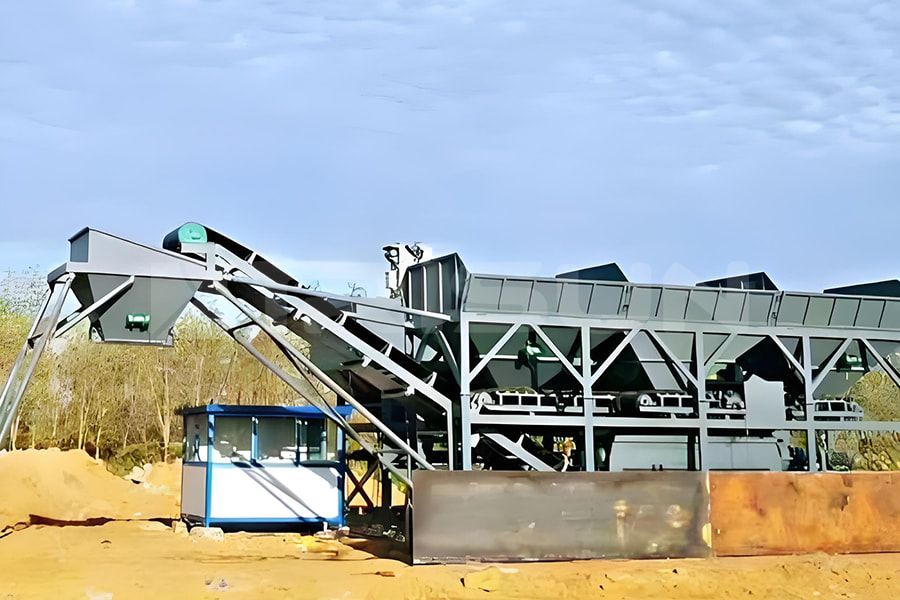
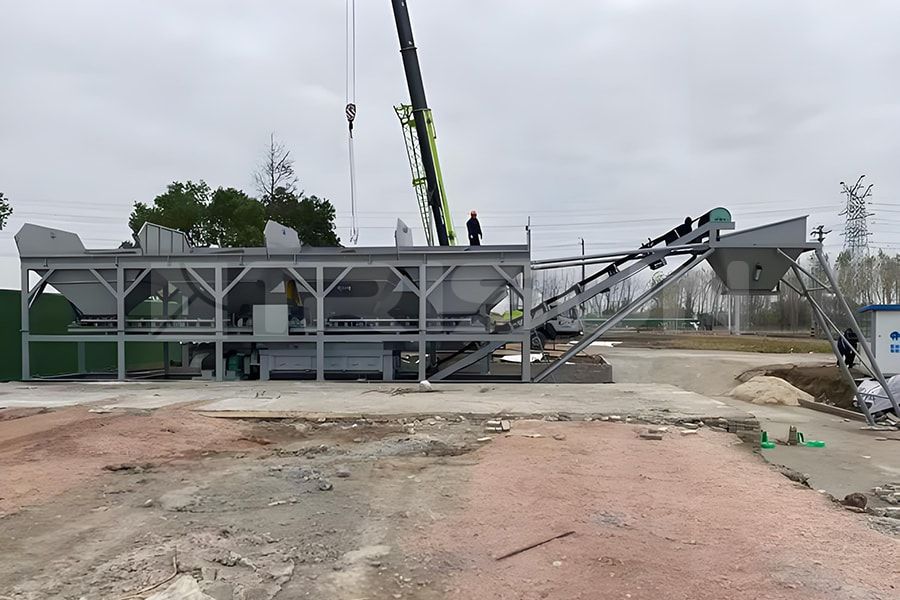
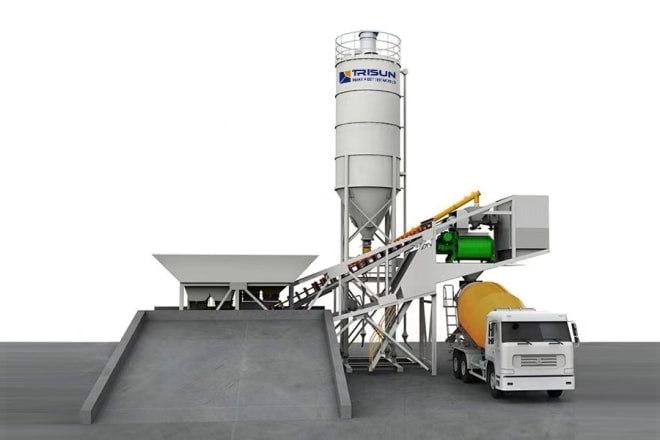
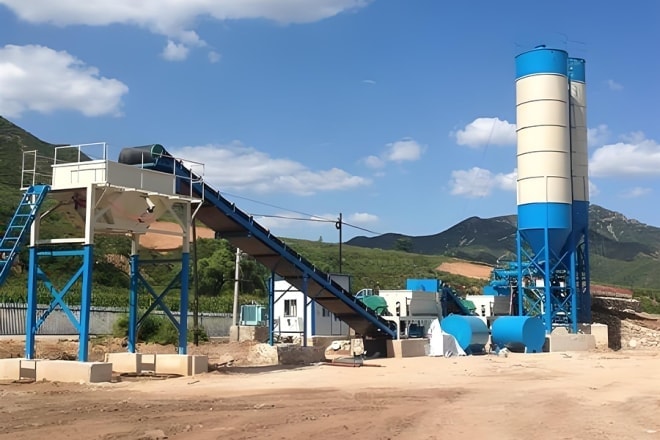
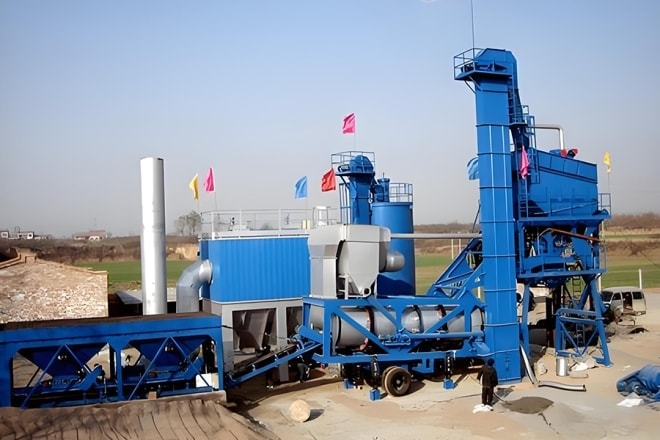
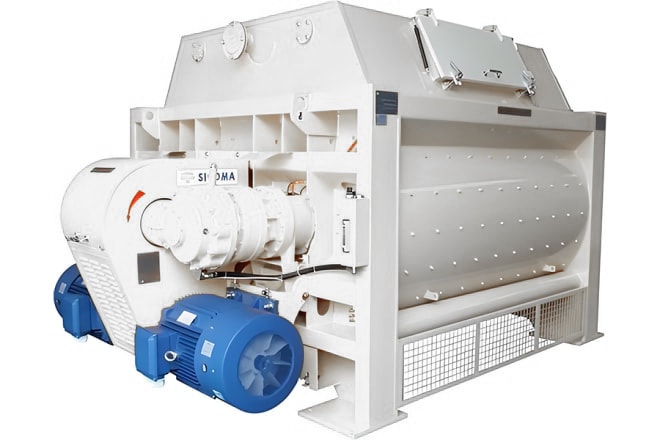
FAQ
Q: How to operate the soil stabilization plant correctly?
A: 1) Security inspection. Routine checks should be made to see if each component is in optimal condition, whether there are any influencing factors in the working environment, and whether the equipment itself has safety issues.
2) Computer startup. Turn on the power and start the computer. The computer first enters the initial screen to display the software program content, etc. At this time, press the Enter key and the system will enter the working parameter screen.
3) Instrument’s power. If the power of the instrument is turned on and there is a power output indication, press twice to perform the zero reset operation. If the power of the instrument is turned on and the power indication is normal, then set various parameters and press the start button to directly enter the working state.
4) Microcomputer’s power. If the soil stabilization plant adopts a microcomputer control, it can be turned on and off directly through a switch. If using the ATX type, you must press and hold the switch until the indicator light goes out and then release it.
In short, once a soil stabilization plant encounters a problem during the production process, the operator needs to pay full attention and shut down the machine for inspection to prevent small mistakes from leading to major accidents.
Q: What are the precautions after the soil stabilization plant is shut down?
A: 1) Be sure to turn off the main power of the mixer before entering the mixer for cleaning. After shutdown, the materials in the mixer should be cleaned in time, and the materials in the final silo should be released in time. The cement tank valve should be closed, and the powder in the screw conveyors should be emptied to avoid clogging of the screw conveyor caused by moisture.
2) The mixer blades should be tightened and the bearings oiled. The sticky material on the belt conveyor rollers should be removed, and the materials scattered on the ground by the belt conveyor should be cleaned up in time.
3) In rainy weather, pay attention to whether there is water accumulation around the control cabinet, and promptly remove the water accumulation around the electrical control cabinet and around the motors of the equipment. On rainy days, the motor reducer, air compressor, vibrator, etc. should be covered to prevent them from being exposed to rain.
4) The whole machine is usually painted once a year, the oil of the whole machine is usually replaced once a year, and the reducer is usually replaced once every six months.
5) Each belt conveyor roller should be checked frequently. If the rollers are not rotating smoothly, they should be refueled and repaired in time. For the lubrication time and the type of refueling, please refer to the equipment manual.
6) It is strictly forbidden to add gear oil to the electric drum when changing the oil, because the gear oil will corrode the enameled wire of the motor. Instead, ordinary bulk engine oil, diesel engine oil or transformer oil should be added, because generally this type of oil is relatively thin, has good insulation properties and good heat dissipation.
Q: How should the soil stabilization plant be properly maintained?
A: High-quality equipment with good maintenance will make a longer service life. Therefore, maintenance of the soil stabilization plant after operation is very important. Many users do not maintain the soil stabilization plant when it is not in use, which can easily reduce the service life of it. The following is a brief introduction to how to maintain the soil stabilization plant after operation.
1) Stop the machine as instructed.
2) Check the wear of the mixer blades and lining plates and replace them if necessary; if the bolts are loose, they should be tightened in time.
3) Check the surface of the belt conveyor. If there is peeling, it should be replaced in time.
4) If the equipment is out of service for a long time, no materials should be stored in the hopper and silo, and they should be cleaned with water.
5) The cement silo must be drained and protected from moisture to prevent the cement from hardening and solidifying.
6) Maintain equipment according to procedures.
7) The operator should close the operating room doors and windows when leaving get off work.