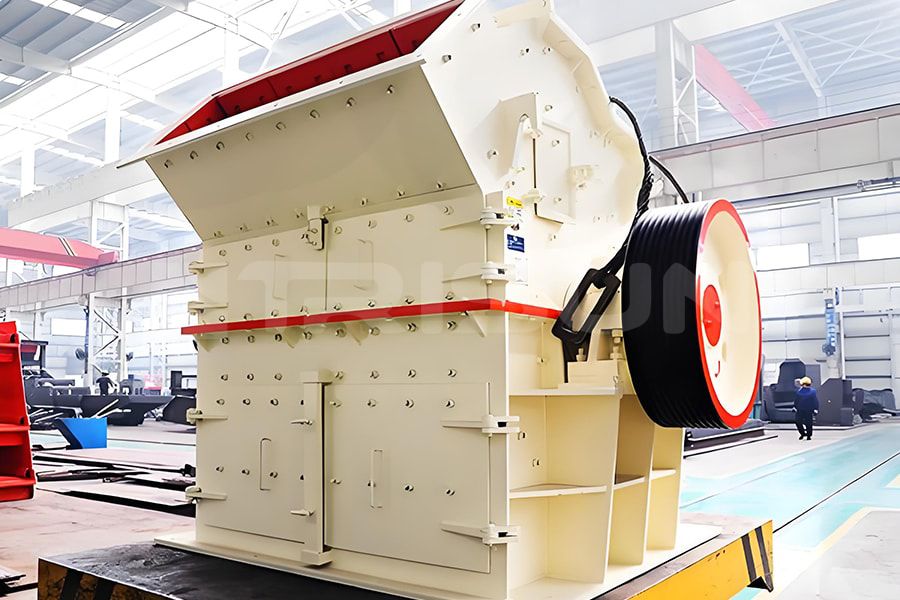
- Features & Properties
- Technical Specification
- Gallery
- Related Products
1. Simplified process, simple structure and easy maintenance.
2. High line speed, excellent fine crushing performance and low power consumption.
3. High wear-resistant hammers, long service life and reduced investment.
4. Stable and reliable operation, controllable discharge particle size.
Model | Rotor specifications (mm) | Maximum feeding size (mm) | Discharge opening adjustable range(mm) | Capacity (t/h) | Power(kw) |
PXJ0804 | Ф800×400 | 120 | 5-20 | 5-45 | 37-45 |
PXJ0806 | Ф800×600 | 180 | 5-20 | 7-55 | 45-55 |
PXJ0808 | Ф800×800 | 180 | 5-20 | 10-65 | 45-55 |
PXJ1010 | Ф1000×1000 | 180 | 5-20 | 15-75 | 55-75 |
PXJ1210 | Ф1200×1000 | 180 | 5-20 | 18-90 | 90-110 |
PXJ1212 | Ф1200×1200 | 180 | 5-20 | 20-110 | 100-132 |
PXJ1414 | Ф1400×1400 | 200 | 5-20 | 25-150 | 160 |
PXJ1616 | Ф1600×1600 | 200 | 5-20 | 30-200 | 250 |
PXJ1818 | Ф1800×1800 | 200 | 5-20 | 40-260 | 315 |
Note: All features, functionality and other product specifications are subject to change without notice or obligation.
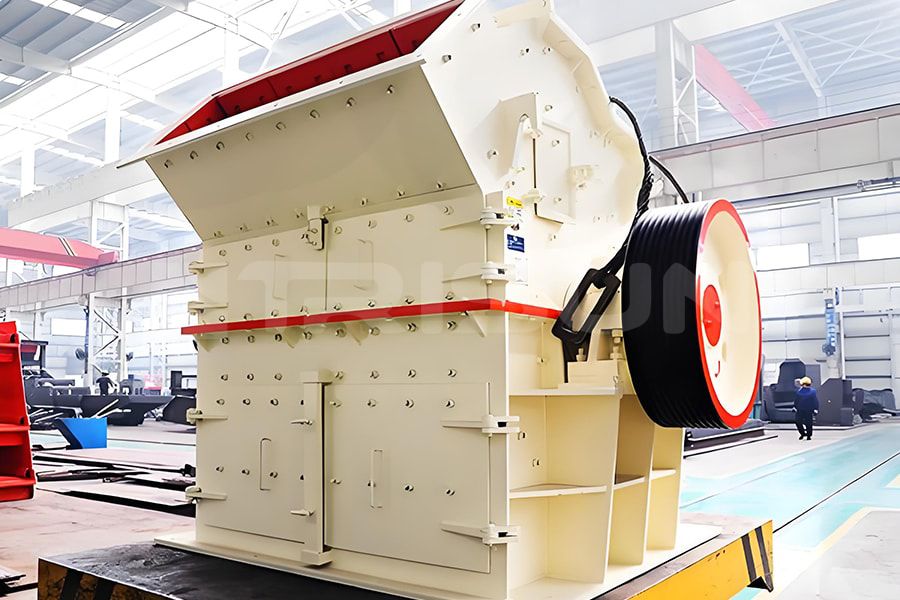
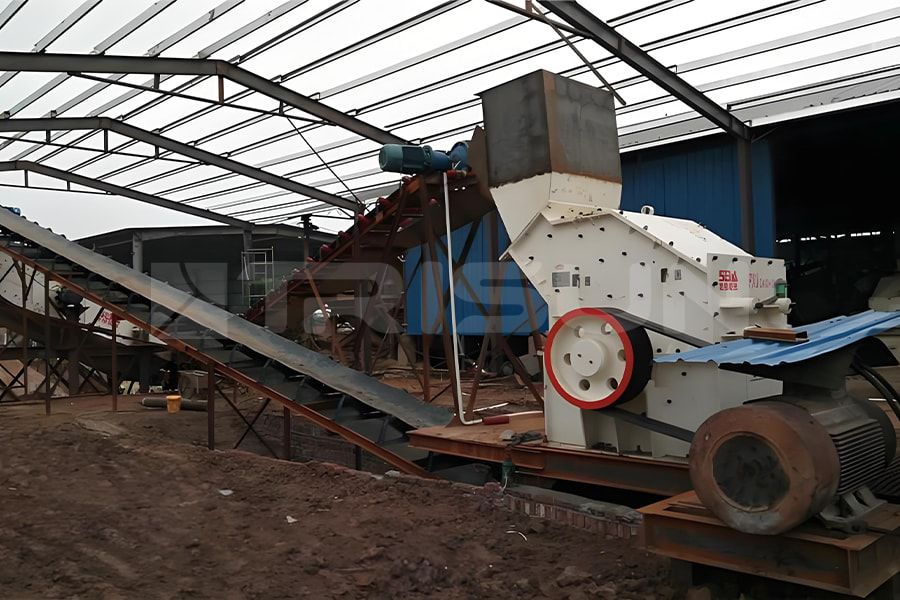
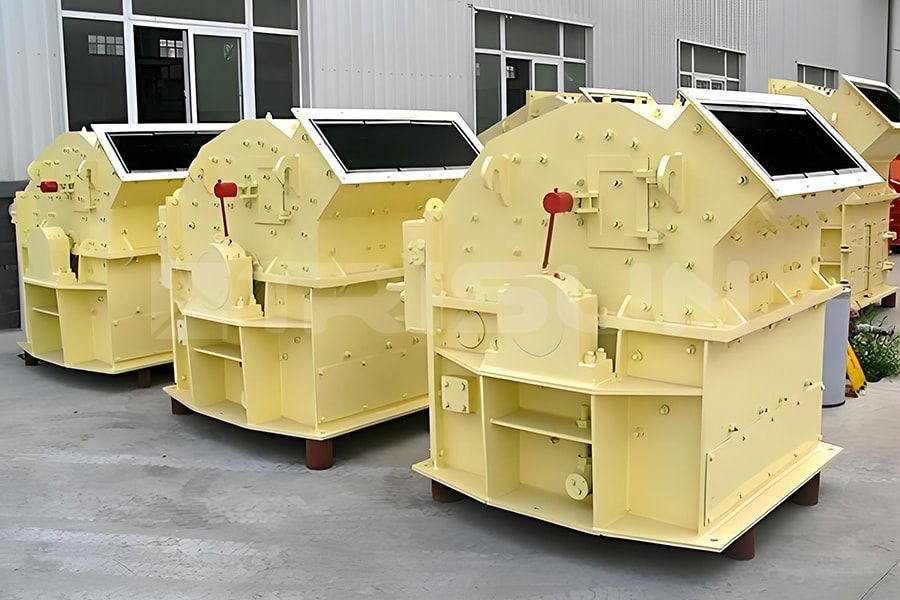
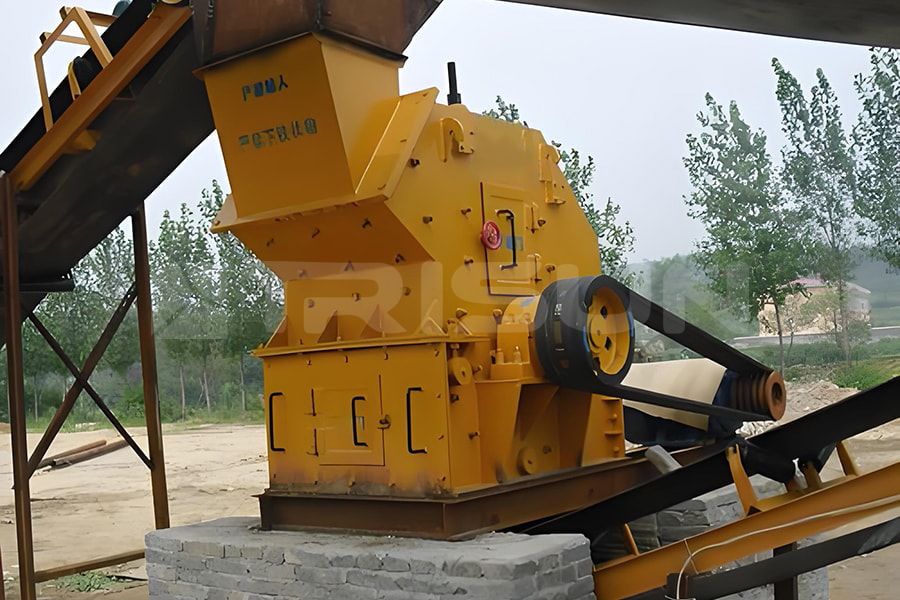
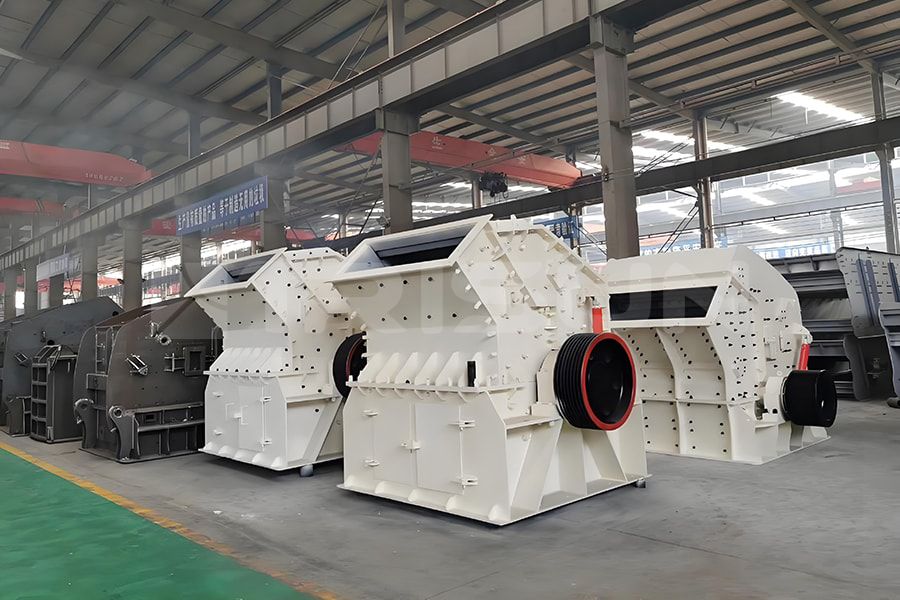
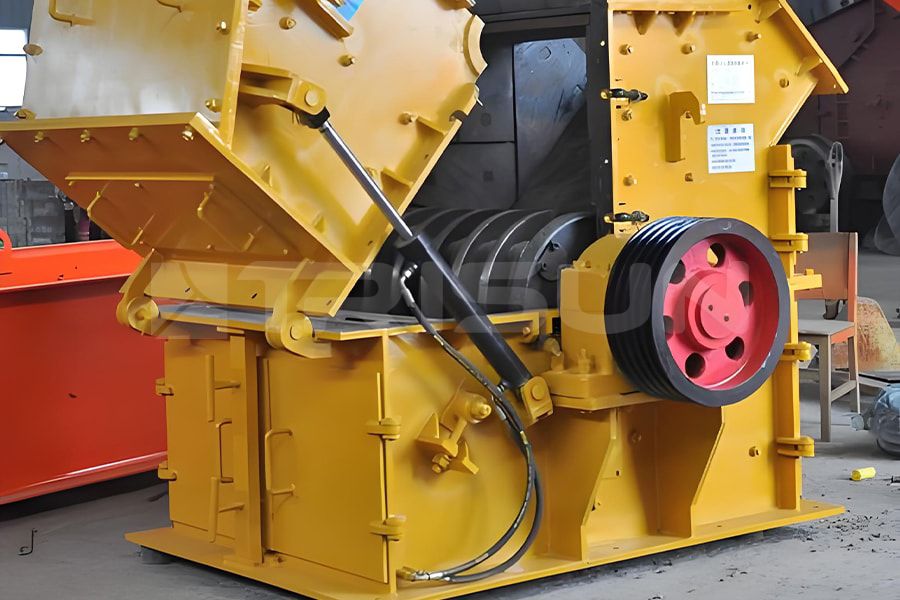
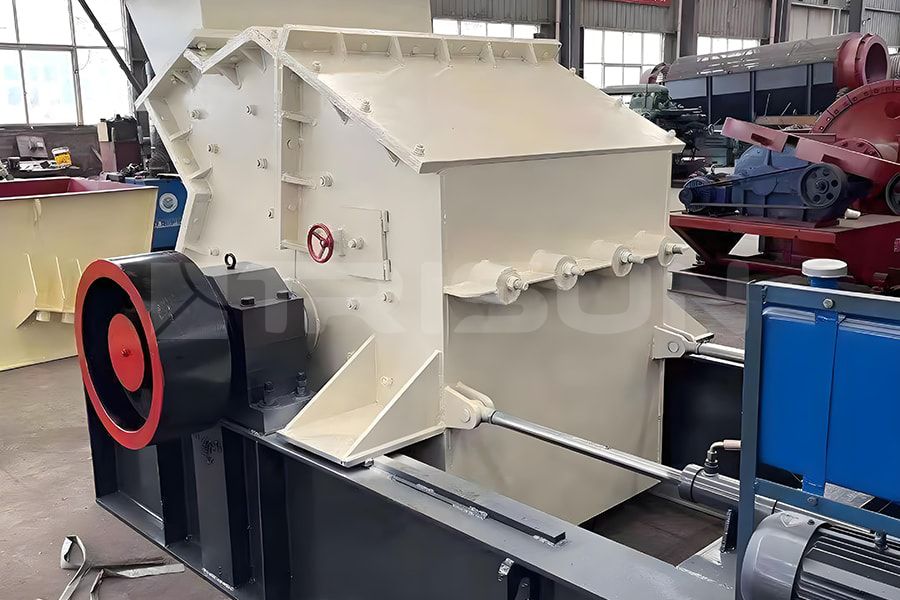
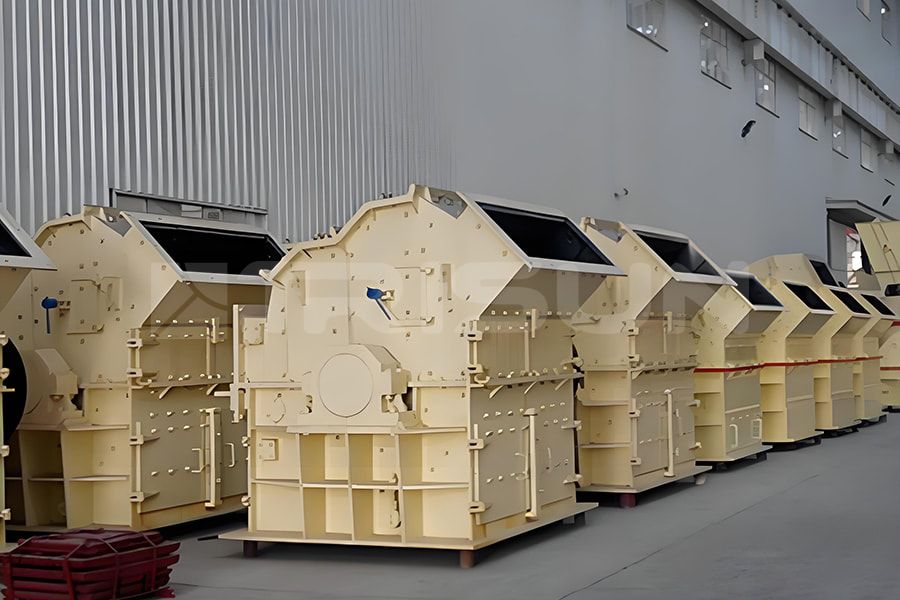
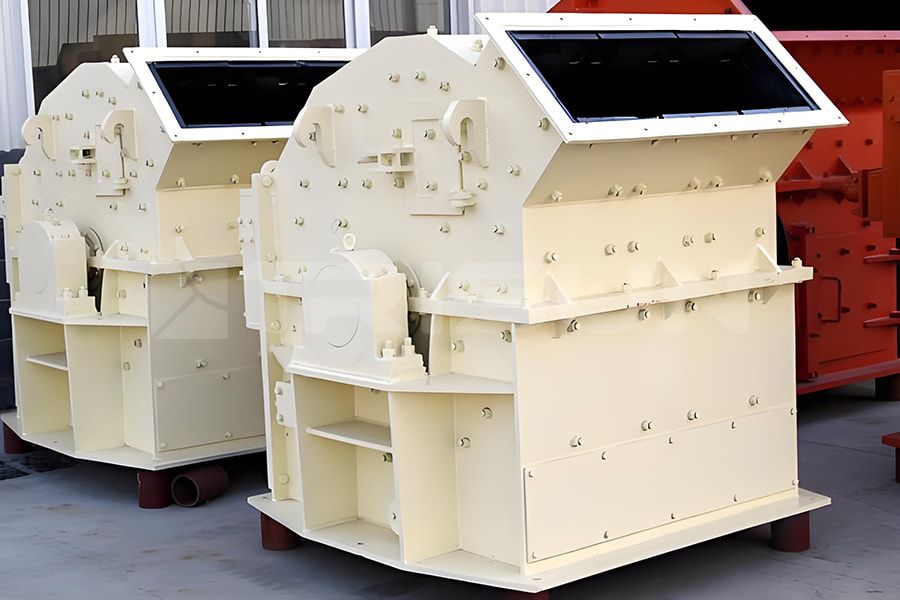
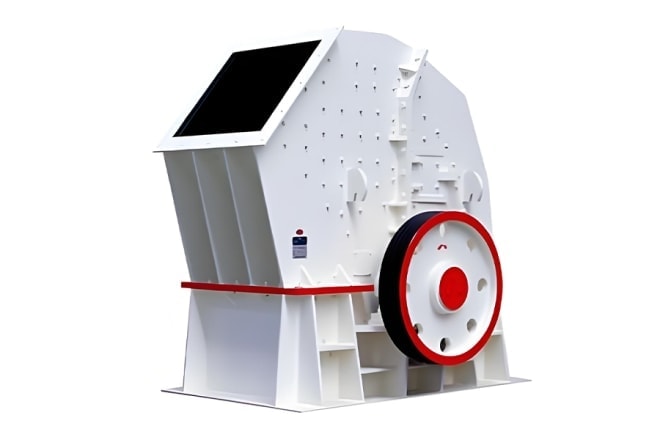
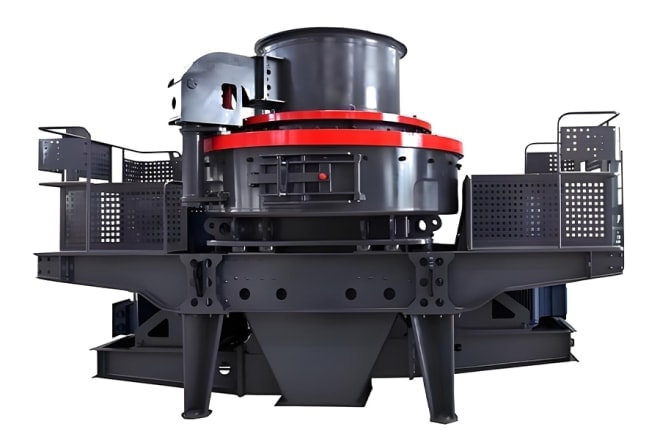
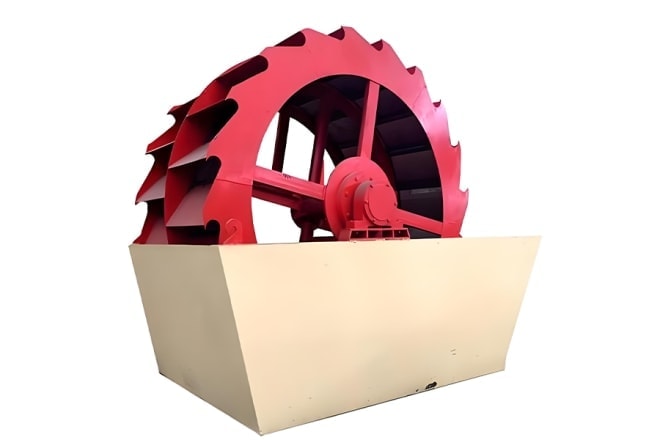
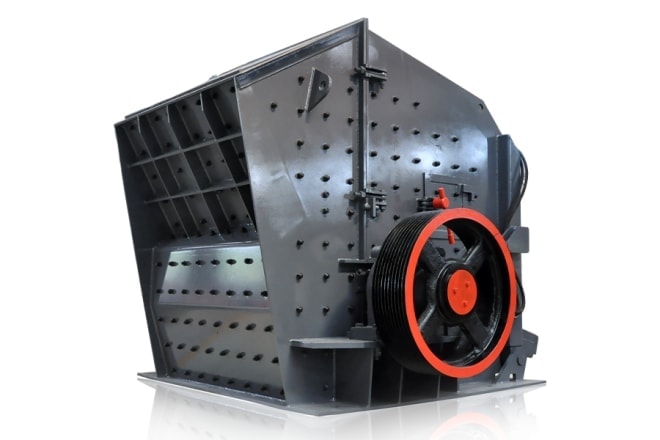
FAQ
Q: What are the advantages of fine hammer crusher compared with traditional fine crushers?
A: The fine hammer crusher is a high-efficiency fine crusher suitable for medium-hardness materials, which is developed by absorbing advanced domestic and international technologies and combined with the specific working conditions of concrete, mining, mineral processing, and building materials enterprises. Its power-saving effect is better than the roller crusher, and its overall effect is better than the cone crusher. The advantages of its design are mainly reflected in the line speed, wear-resistant parts material, machine structure, grate plate, rigid extrusion crushing effect, etc. It fully realizes the effective control of the discharge particle size and ensures the long-term stability of the discharge particle size. It has the characteristics of high fine crushing efficiency, extremely low power consumption, good dust protection, long service life, low accessory costs, high operating rate, and easy maintenance.
Q: What is the difference between impact crusher and hammer crusher?
A: There are four obvious differences between impact crushers and hammer crushers. These four points are working principle, application scope, adjustment method of discharge opening, and wear rate of consumable parts.
1) Working principle. The impact crusher relies on the hammers to impact and crush the materials put into the crushing cavity from bottom to top, and also throws the materials onto the impact lining for secondary crushing. The hammer crusher crushes the materials in the direction in which the materials fall.
2) Application scope. The impact crusher adopts a fixed rotor structure. The rotational inertia force of the rotor can bring greater power to the machine, so the impact crusher can crush larger and harder materials. The feed of the hammer crusher is generally less than 500mm, which is suitable for processing small pieces of materials with slightly lower hardness. The hammer crusher is not recommended for crushing relatively wet materials.
3) Adjustment method of discharge opening. The impact crusher can use many methods to adjust the size of the discharge opening, such as adjusting the rotor speed, adjusting the gap between the impact plate and the crushing chamber, etc. The hammer crusher uses replacement grating plates to control and adjust the discharge size.
4) Wear rate of consumable parts. The load of the impact crusher is mainly on the hammer. When the rotor speed is normal, the feed material will fall to the surface of the hammer (the crushing surface). The back and sides of the hammer are not worn, so only one surface is prone to wear. The main working part of the hammer crusher is the rotor with the hammer. The motor drives the rotor to rotate at high speed in the crushing chamber. The hammer needs to be repeatedly beaten from multiple sides and is the main wearable part, so it wears relatively quickly.
Q: What are the possible causes and solutions of common faults in the fine hammer crusher?
A:Faults | Causes | Solutions |
Excessively coarse discharge | The V-belt is too loose | Tighten the V-belt |
Excessive idling resistance | Plug material in the upper sealing cap of the bearing | Open the upper sealing cap to remove it |
Bearing overheating |
1) Lack of oil or dust 2) Bearing damage |
1) Lubricate or clean bearings 2) Replace bearings |
Metal clanking | Lining plate or rotor wearing parts fall off | Retighten them |
Significantly increased discharge particle size |
1) Excessive gap between impact plate, grate and hammer 2) Excessively worn hammer and grate |
1) Re-adjust the gaps between parts 2) Turn the hammer around and replace the grate |
Significantly reduced capacity, current exceeding rated value |
1) Uneven feeding 2) Excessive moisture content 3) Grate gaps blocked 4) Too small grate gap |
1) Adjust feeding 2) Reduce the moisture content 3) Clear blocked materials from grate 4) Adjust the grate gap |