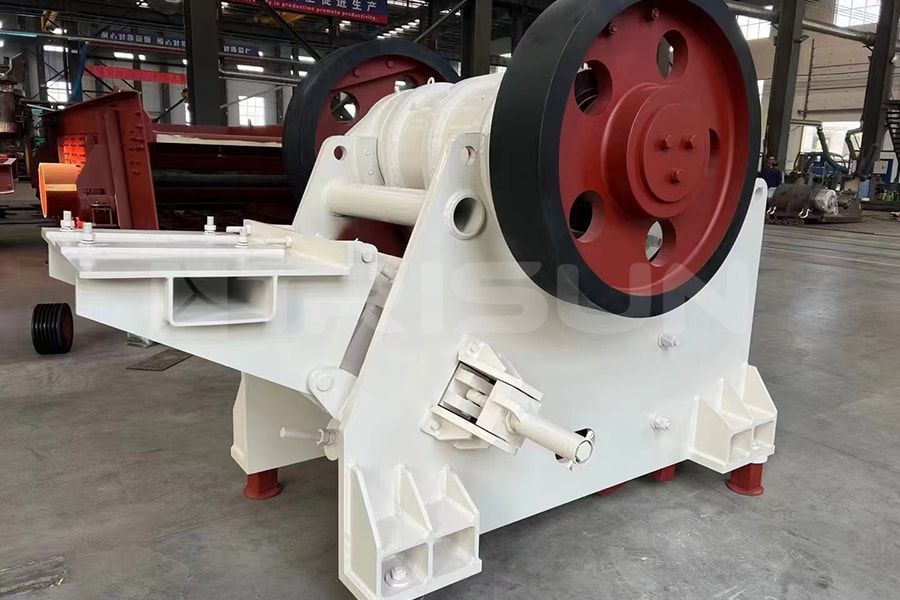
- Features & Properties
- Technical Specification
- Gallery
- Related Products
1. It has superior motion characteristics and a unique cavity shape. The jaw plates can be interchanged and turned around four times to achieve uniform wear on the surface of the jaw plates, improve material utilization and extend service life. Compared with other traditional crushers, its processing capacity is more than 15% larger and energy consumption is saved by more than 10%.
2. The tooth peaks of the jaw plates (movable jaw plate and fixed jaw plate) in the crushing cavity are opposite , which is more conducive to crushing harder materials.
3. Its structural design with adjustable transmission angle enables higher output capacity under the same discharge opening.
4. The fixed jaw plate and the movable jaw plate are universal, which can effectively reduce the number of spare parts for the user and make installation more convenient.
5. The discharge port is hydraulically adjusted by double jacks, making the adjustment faster and more labor-saving.
6. The movable jaw and the frame are detachable structures for easy transportation.
Model | Input size (mm) | Maximum feeding size (mm) | Output adjustable range (mm) | Capacity (t/h) | Power(kw) | Dimensions (mm) |
PEC58 | 520×800 | 430 | 60-150 | 80-290 | 75 | 2650×1540×1780 |
PEC69 | 580×930 | 480 | 60-175 | 105-390 | 90 | 2850×2270×1950 |
PEC710 | 700×1060 | 560 | 70-200 | 150-500 | 110 | 3280×2580×2400 |
PEC811 | 850×1100 | 680 | 70-200 | 190-625 | 160 | 3700×2790×2950 |
PEC912 | 950×1250 | 760 | 100-250 | 270-831 | 160 | 4230×2780×2960 |
PEC1112 | 1100×1250 | 850 | 100-250 | 230-760 | 160 | 4100×2750×2780 |
PEC1115 | 1070×1500 | 850 | 125-300 | 425-1195 | 200 | 4130×3000×3330 |
PEC1214 | 1200×1400 | 960 | 125-250 | 340-880 | 200 | 5030×3440×3970 |
PEC1216 | 1200×1600 | 960 | 150-300 | 430-1145 | 250 | 5780×3460×3580 |
PEC1218 | 1200×1800 | 960 | 150-300 | 490-1280 | 315/355 | 5700×4150×3550 |
PEC1315 | 1300×1500 | 1040 | 150-300 | 530-1280 | 200 | 4620×2890×4190 |
PEC1416 | 1400×1610 | 1120 | 120-300 | 470-1150 | 250 | 5780×3660×3580 |
PEC1518 | 1500×1800 | 1200 | 125-325 | 630-1300 | 355 | 6600×3830×4400 |
PEC1520 | 1500×2000 | 1200 | 175-300 | 630-1435 | 400 | 6600×4030×4400 |
Note: All features, functionality and other product specifications are subject to change without notice or obligation.
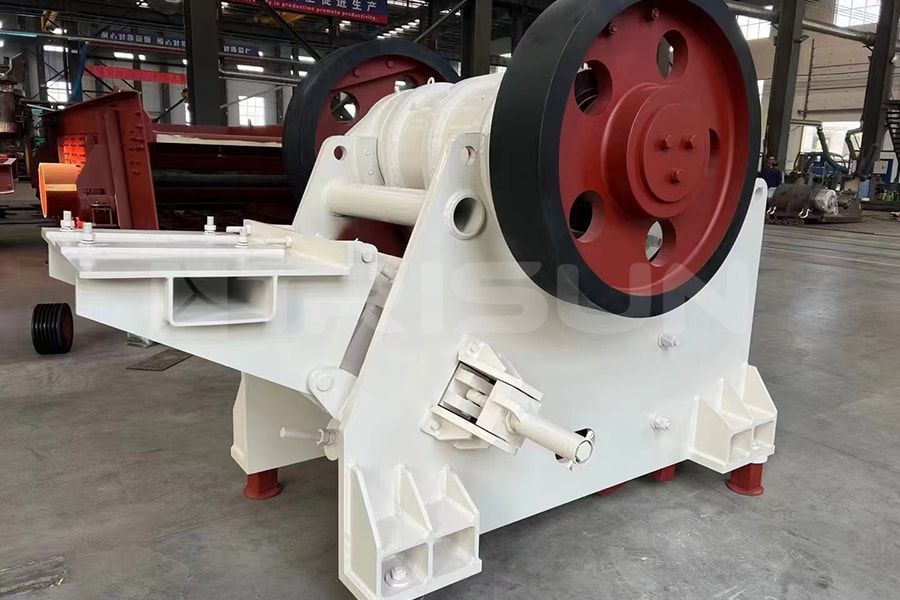
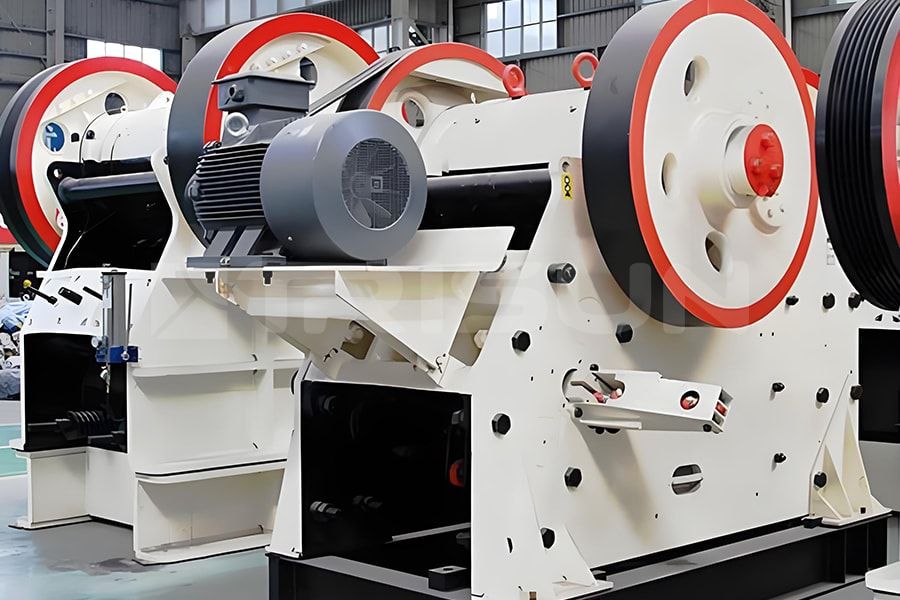
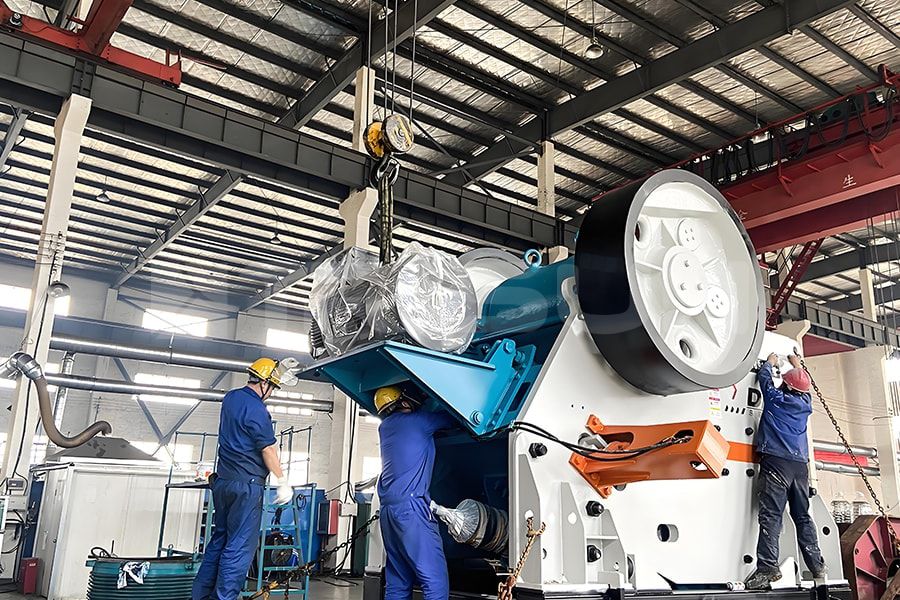
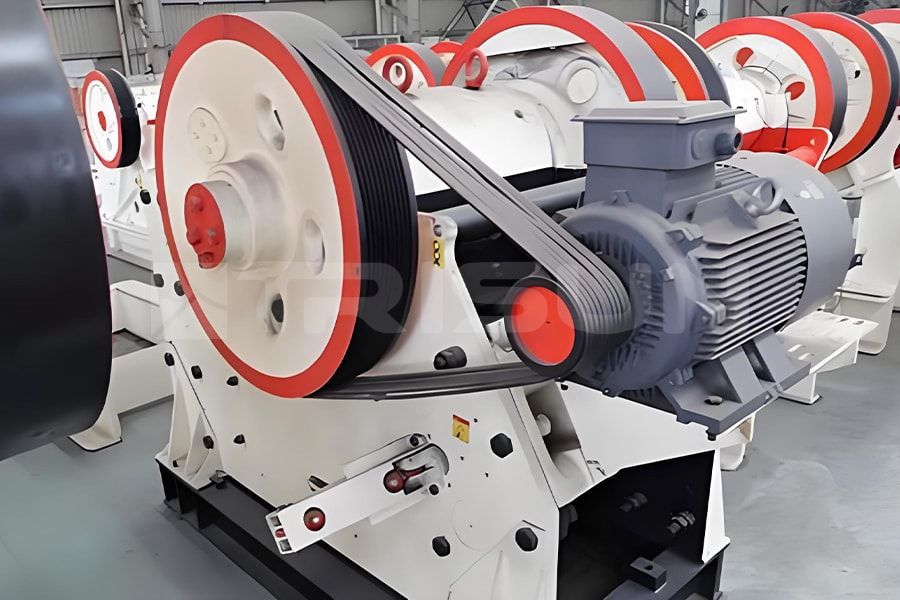
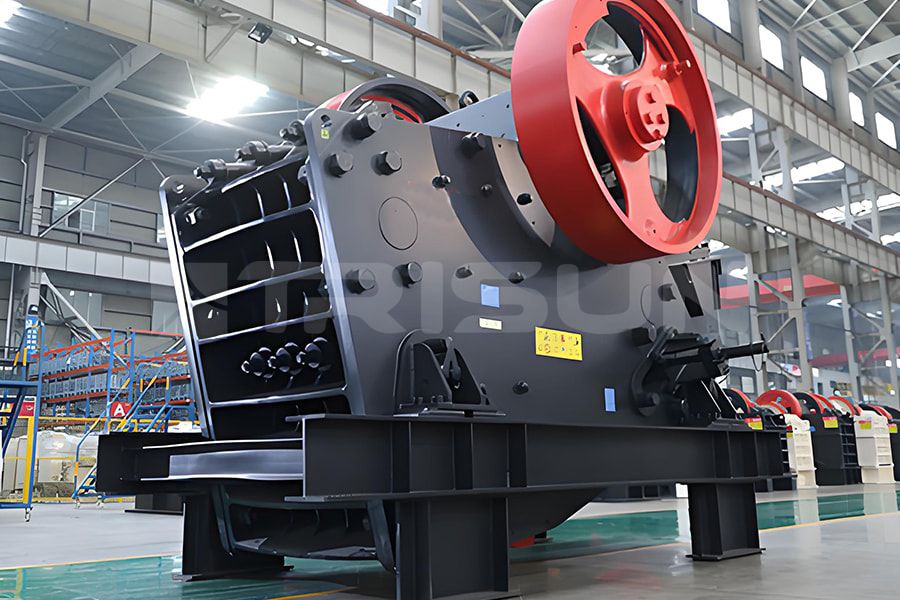
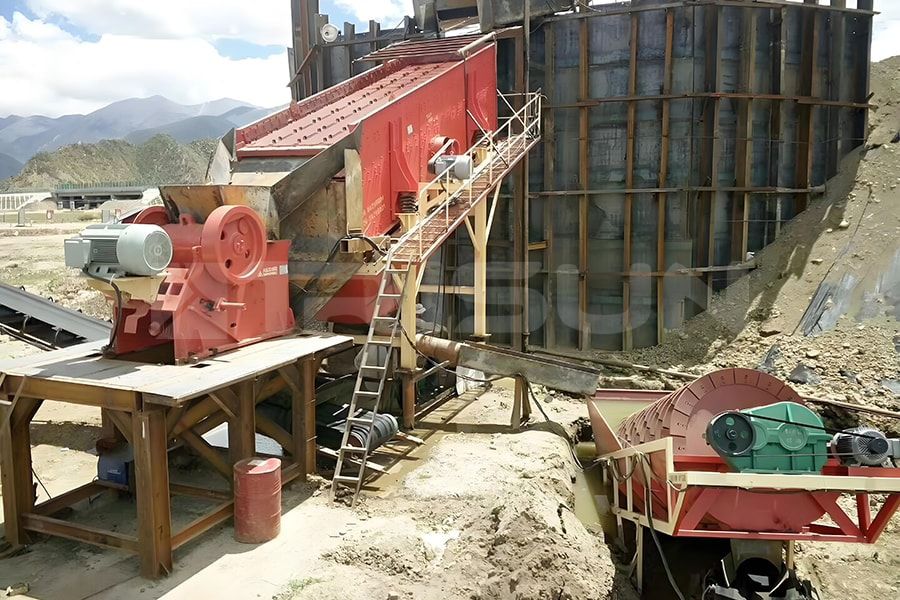
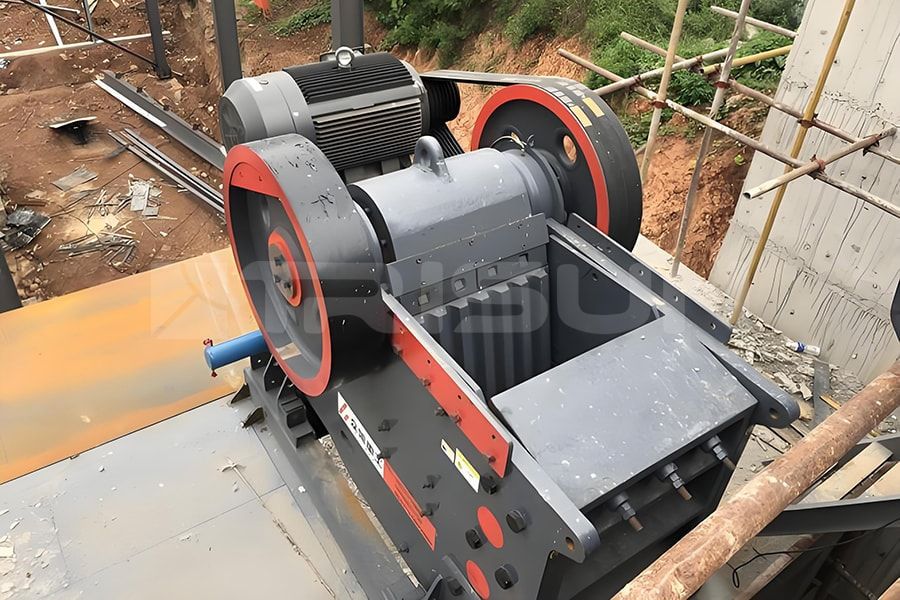
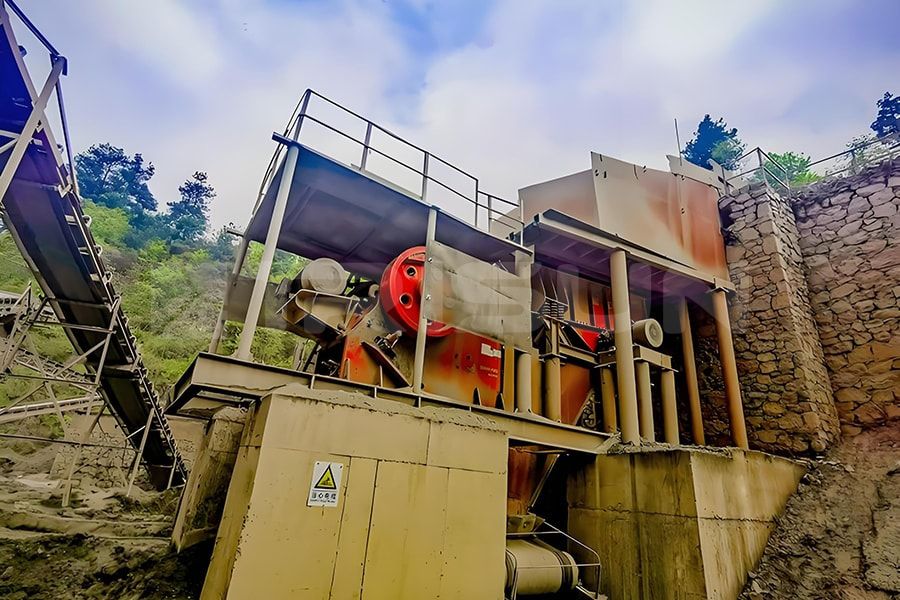
FAQ
Q: What precautions should be taken before starting, starting up, running and stopping the PEC series jaw crusher?
A: 1) Before starting.
1-1. Check whether there are materials and other debris in the crushing cavity of the crusher. If there are ores and other debris, remove them in time.
1-2. Check whether the gap between the jaw plate and the discharge port meets the usage standards. If anything is inappropriate, it should be replaced or adjusted immediately.
1-3. Check whether the screws of each part are loose. If they are loose or fallen off, tighten them in time.
1-4. Check whether there are any obstacles around the equipment that may affect the operation of the equipment.
1-5. Check whether the amount of oil in each lubricating part of the equipment is sufficient and whether the oil filling facilities are complete.
1-6. Check whether the switches of electrical ancillary equipment are in the stopping position.
2) Starting up.
2-1. After receiving the starting signal, you must strictly follow the starting sequence.
2-2. After the equipment is started, carefully check whether there are any abnormal sounds, and discover problems promptly.
2-3. When it is confirmed that the equipment is operating normally, the feeding signal is sent, and the feeding is allowed in the next process.
2-4. Use dust-proof and dust-reduction equipment carefully to maintain civilized production.
3) Running.
3-1. Check whether there is any dust leakage in the dustproof facilities of this post. If dust leakage and dust are found, they should be eliminated in time.
3-2. Check whether there is any abnormal sound from the equipment and whether the current is normal.
3-3. Check whether all the materials crushed by this machine is sent to the next process. If any leakage is found, handle and adjust it in time.
3-4. Check the equipment for oil leakage and oil shortage.
3-5. Check whether the temperature of each bearing and motor meets the operating requirements.
3-6. When it is found during normal operation that the discharged size exceeds the specified limit, adjustments must be made immediately, and materials larger than the specified size are not allowed to be sent to the next process.
3-7. When a major accident occurs, you should stop the crusher urgently and protect the scene.
4) Stopping.
4-1. When receiving the stop signal, first stop feeding, and then stop when there is no material in the crushing cavity.
4-2. When stopping, you must follow the stopping sequence and do not pull the main power switch first.
4-3. Check the wear of the jaw plate after stopping.
4-4. Handle the parts to be repaired that are found by the shift. If the shift cannot repair the parts after inspection, keep records and report to the shift leader.
4-5. Clean the post well, send all dirty items to the designated place, and close doors and windows properly.
4-6. Record the operation diary of this shift truthfully, and do not conceal equipment or personal accidents.
4-7. It is forbidden to drink alcohol, and it is forbidden to be late, leave early, leave work, sleep on duty, etc.