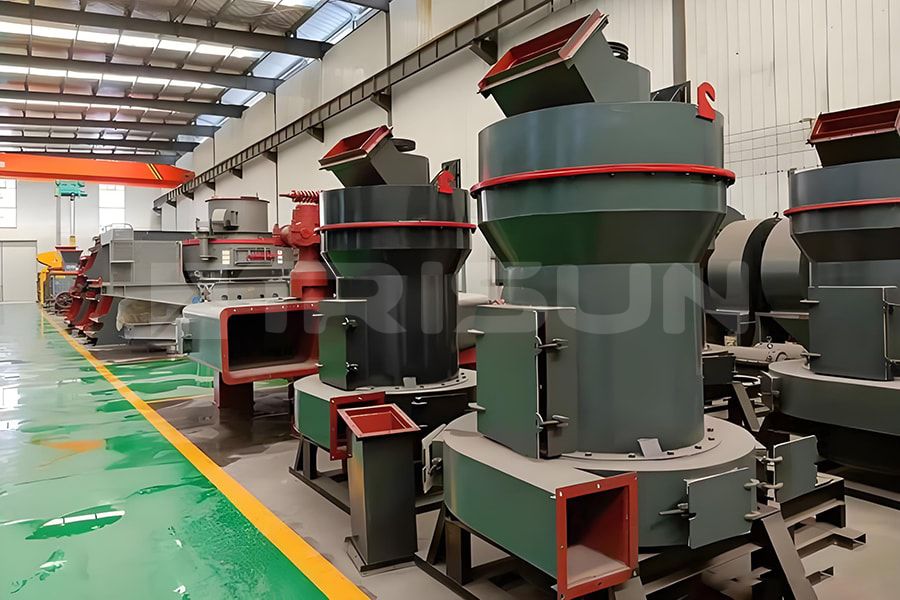
- Features & Properties
- Technical Specification
- Gallery
- Related Products
1. Reasonable structure. Vertical structure, small footprint and strong completeness, rough processing, transportation, milling, and packaging can all form an independent production system.
2. Low oversize rate. Compared with other grinding mills, the oversize rate of Raymond mill is as low as 1%, and it is also more economical to operate and use.
3. Safe and reliable. The main shaft and star-shaped hanger have been structurally modified to facilitate stability, making the transmission smoother and the operation more reliable.
4. Long service life. Made of high-quality materials and fine craftsmanship, the equipment has high operating efficiency and good wear resistance.
5. Automated operations. The electrical system adopts centralized control, and the Raymond mill workshop can basically realize unmanned operation and is easy to maintain.
Model | Roller quantity | Roller diameter (mm) | Roller height (mm) | Ring diameter (mm) | Maximum feeding size (mm) | Discharging size (mesh) | Capacity (t/h) | Power(kw) | ||
Mill | Blower | Classifier | ||||||||
3R2115 | 3 | 210 | 150 | 726 | 15 | 80-600 | 0.28-1.8 | 15 | 11 | 2.2 |
3R2615 | 3 | 260 | 150 | 865 | 15 | 0.35-2.8 | 18.5 | 15 | 2.2 | |
3R2715 | 3 | 270 | 150 | 884 | 15 | 0.40-3.4 | 22 | 15 | 2.2 | |
3R3016 | 3 | 300 | 160 | 990 | 20 | 0.6-4.5 | 30 | 22 | 2.2 | |
4R3216 | 4 | 320 | 160 | 1073 | 25 | 1.0-5.2 | 37 | 37 | 5.5 | |
5R4119 | 5 | 410 | 190 | 1400 | 25 | 1-10 | 75 | 75 | 7.5 | |
6R4525 | 6 | 450 | 250 | 1770 | 30 | 2-15 | 132 | 132 | 18.5 |
Note: All features, functionality and other product specifications are subject to change without notice or obligation.
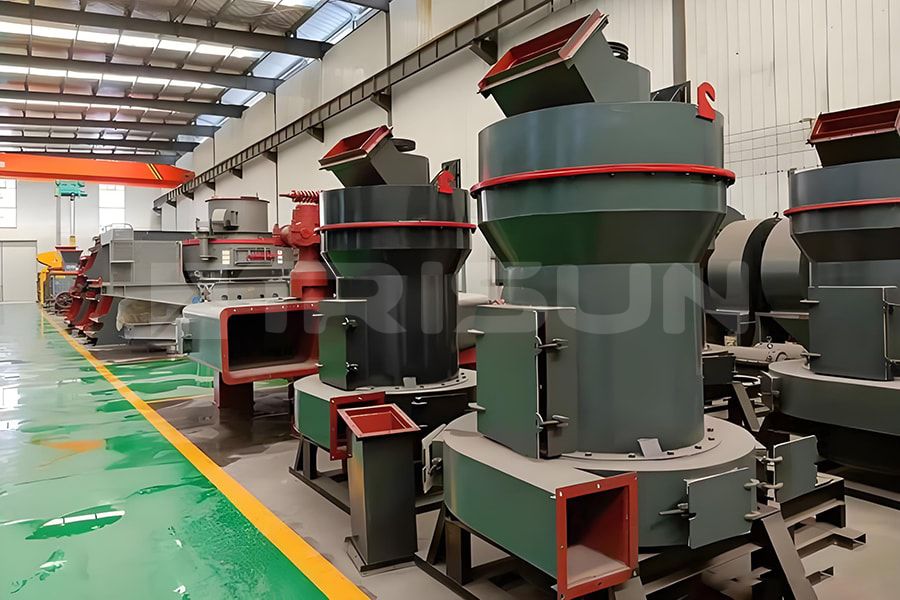
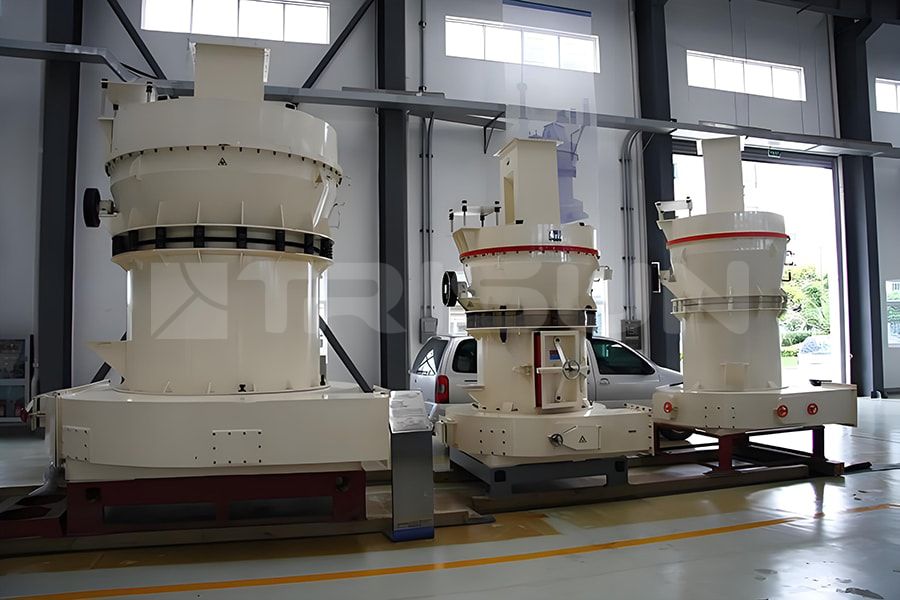
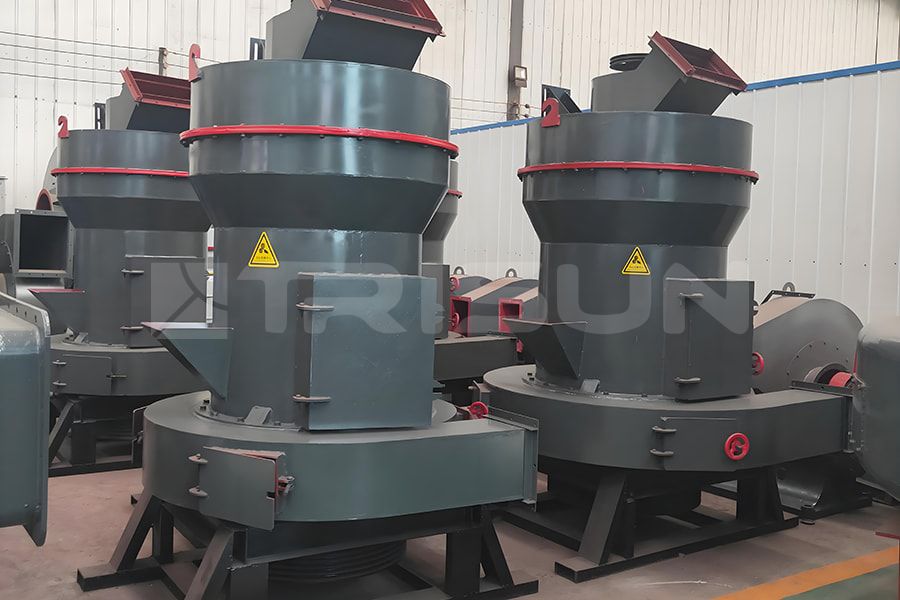
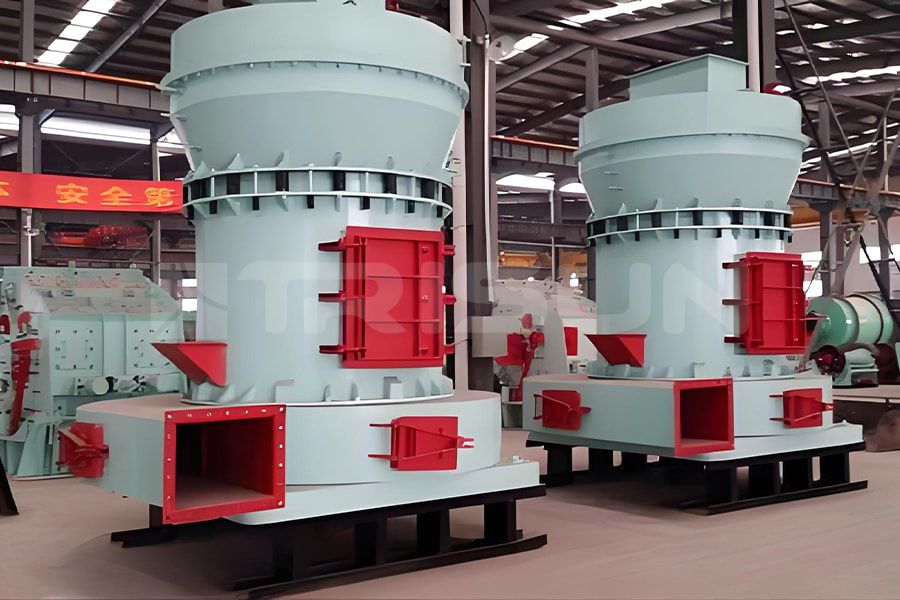
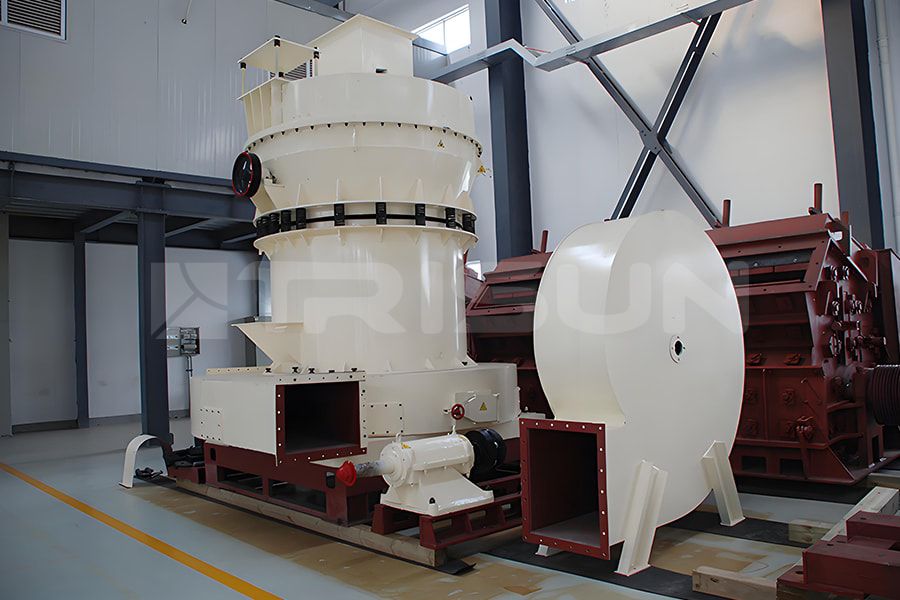
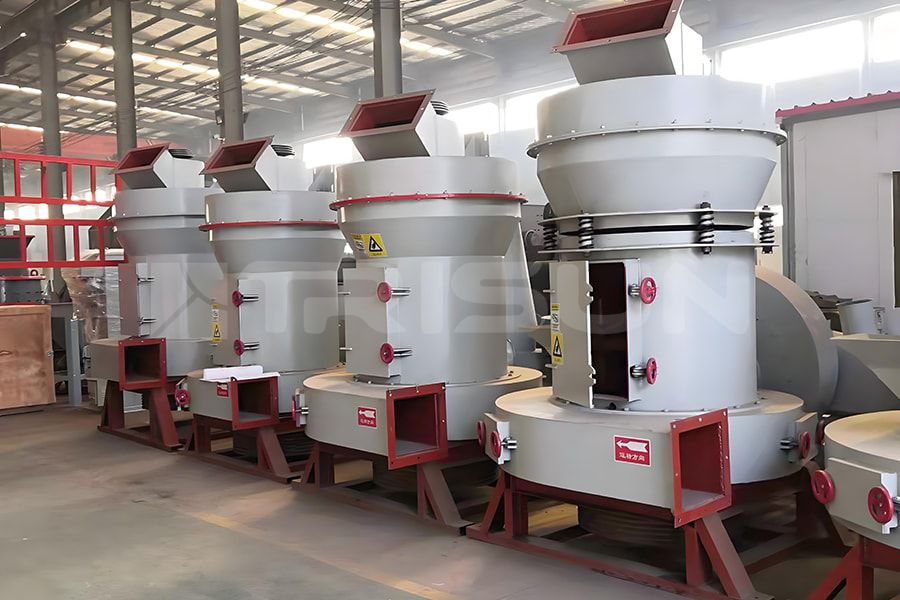
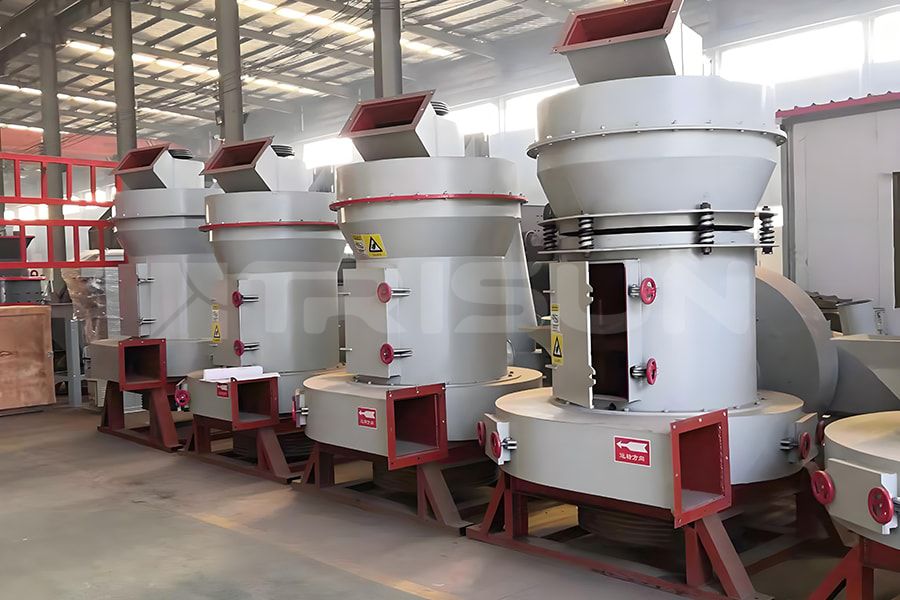
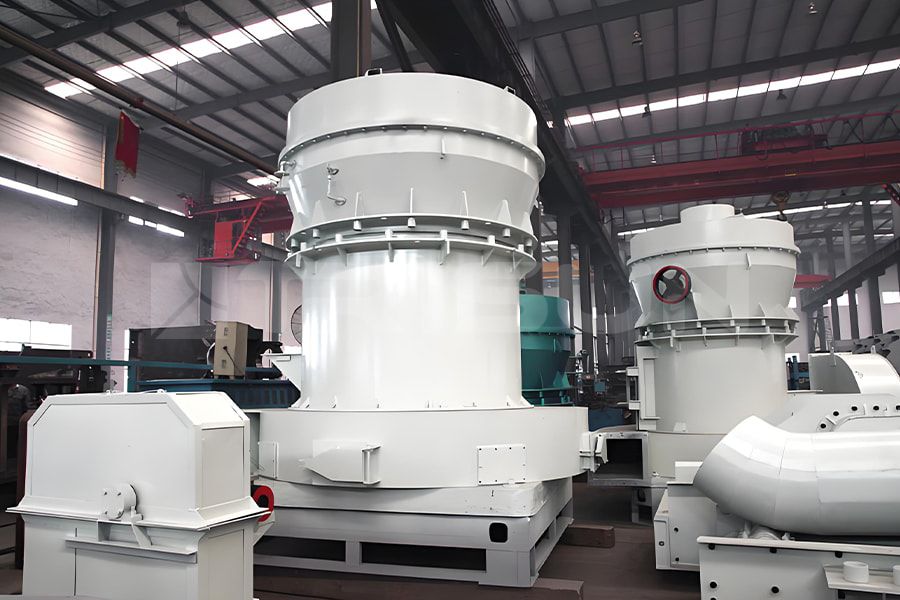
FAQ
Q: What is the working principle of the grinding and air classification of Raymond mill?
A: Grinding: The materials to be ground are added into the mill from the feed hopper. The rollers suspended on the star-shaped hanger of the mill revolves around the vertical axis and rotates on its own at the same time. Due to the centrifugal force during rotation, the rollers will swing outward and press against the ring, causing the scraper to scoop up the material and send it between the rollers and the ring. The purpose of grinding the material is achieved due to the rolling of the grinding rollers.
Air classification: After the materials are ground, the blower blows the air into the mill casing and blows up the powder to place them in the classifier above the grinding chamber for classification. Materials that are too fine and too coarse will fall into the grinding chamber and be ground again. Materials that meet the specifications will enter the cyclone collector with the air flow. After collection, they will be discharged through the outlet. The air flow returns to the blower through the return duct at the upper end of the large cyclone collector. The air path is circulated and flows under negative pressure. The increased air volume in the circulating air path is discharged through the exhaust pipe between the blower and the mill, and enters the small cyclone collector for purification treatment.
Q: What precautions should be taken in the use and maintenance of Raymond mill?
A: 1) Before installing the Raymond mill, the operators must receive necessary technical training so that they can understand the principles and performance of the Raymond mill and become familiar with the operating procedures of the Raymond mill. During the use of the Raymond mill, fixed personnel should be responsible for supervising it, and the operators must have a certain technical level.
2) In order to ensure the normal operation of the Raymond mill, an Equipment Maintenance and Safety Operation System should be formulated to ensure the long-term safe operation of the mill. At the same time, necessary maintenance tools, grease and corresponding accessories must be available.
3) After the Raymond mill has been used for a period of time, it should be inspected and repaired. At the same time, wearing parts such as grinding rollers, rings, blades, etc. should be repaired and replaced. Before and after use, the connecting bolts and nuts on the grinding rollers should be carefully inspected to see if they are loose and whether the lubricating grease is sufficient.
4) When the grinding rollers of Raymond mill has been used for more than 500 hours and the are replaced, the rolling bearings in the roller sleeve should be cleaned, and the damaged parts should be replaced in time. The refueling tool can be a manual filling pump or a grease filling gun.
5) When stopping, the feeding should be stopped first. At this time, the mill continues to rotate so that the remaining materials can continue to be ground. After about one minute, the motor of the mill can be turned off to stop the grinding, and then the blower motor and classifier motor can be stopped.
Q: What is the difference between Raymond mill and ball mill?
A: 1) Mechanical structure. Raymond mill is mainly composed of grinding mill, blower, classifier, pipeline, etc. The overall structure of the ball mill is mainly divided into several parts such as the feeding part, the drum part, the discharging part, the transmission part, the temperature measurement part, and the dust removal part.
2) Working principle. Raymond mill uses relatively advanced powder production technology. Its main principle is to feed the material evenly into the mill, and then use wind to blow the material away for classification. The ball mill mixes a certain amount of steel balls with the materials in the drum and grinds them together to form the required fineness.
3) Application scope. Raymond mill is suitable for grinding various non-flammable, non-explosive and brittle non-ferrous metals and non-metallic ores. The ball mill has a wider scope of application and is suitable for grinding various hard materials such as refractory materials, quartz sand, glass, and ceramics.
4) Product characteristics. The discharged product of Raymond mill has a relatively fine particle size, and coarse particles rarely appear. The discharge product of the ball mill is relatively uniform and has a wide particle size distribution.
5) Production efficiency. Relatively speaking, the production efficiency of ball mill in grinding mineral is higher. Taking the grinding of perlite as an example, it takes 20-30 minutes to grind 1 ton using a Raymond mill, but only 1-2 minutes using a ball mill.
To sum up, although Raymond mill and ball mill are both grinding mills, they have differences in mechanical structure, working principle, application scope, etc. When purchasing, you need to select appropriate mill based on actual production needs and production processes.