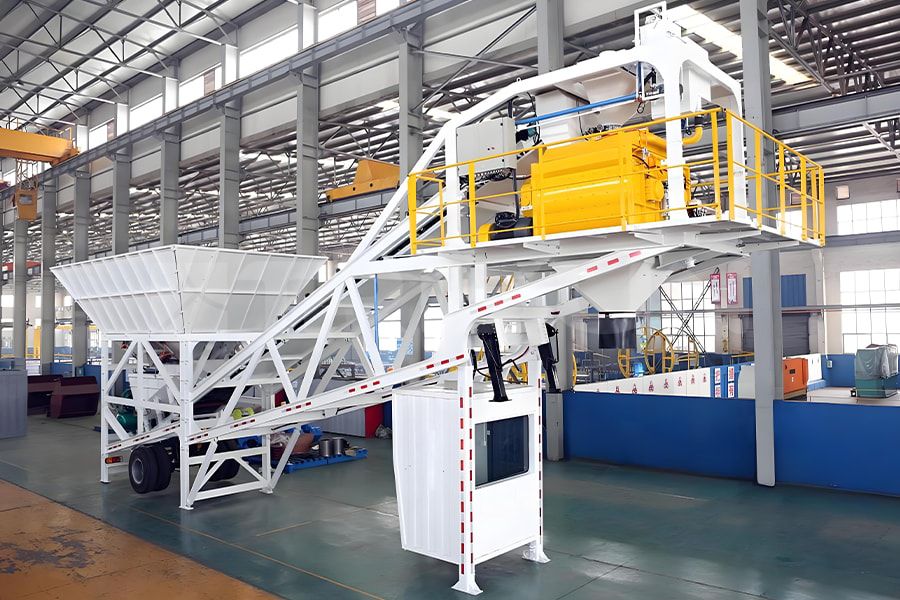
- Features & Properties
- Technical Specification
- Gallery
- Related Products
1. It is quick to disassemble and assemble, and easy to move. And is designed as a trailer, making it easy to be towed. It comes with its own generator and air compressor.
2. It takes up little space and can be installed within the project area. Less concrete foundation required and can be installed on a flat hardened concrete floor.
3. The external dimensions of all component transport units of the mobile concrete plant are smaller than the internal dimensions of the container.
4. Manual and automatic modes are available, allowing for free production control, high batching accuracy, automatic height adjustment, and user-friendly operation.
5. The quality and slump of concrete can be controlled on-site, saving waste caused by substandard quality.
Model | YHZ25/30 | YHZ35/45 | YHZ50/60 | YHZ75/90 | YHZ100/120 |
Theoretical maximum capacity | 30m³/h | 45m³/h | 60m³/h | 90m³/h | 120m³/h |
Mixer capacity | 0.5m³/batch | 0.75m³/batch | 1m³/batch | 1.5m³/batch | 2m³/batch |
Batcher | PLD800 | PLD1200 | PLD1600 | PLD2400 | PLD3200 |
Discharging height | 3800mm | 3800mm | 3800mm | 4000mm | 4000mm |
Note: All features, functionality and other product specifications are subject to change without notice or obligation.
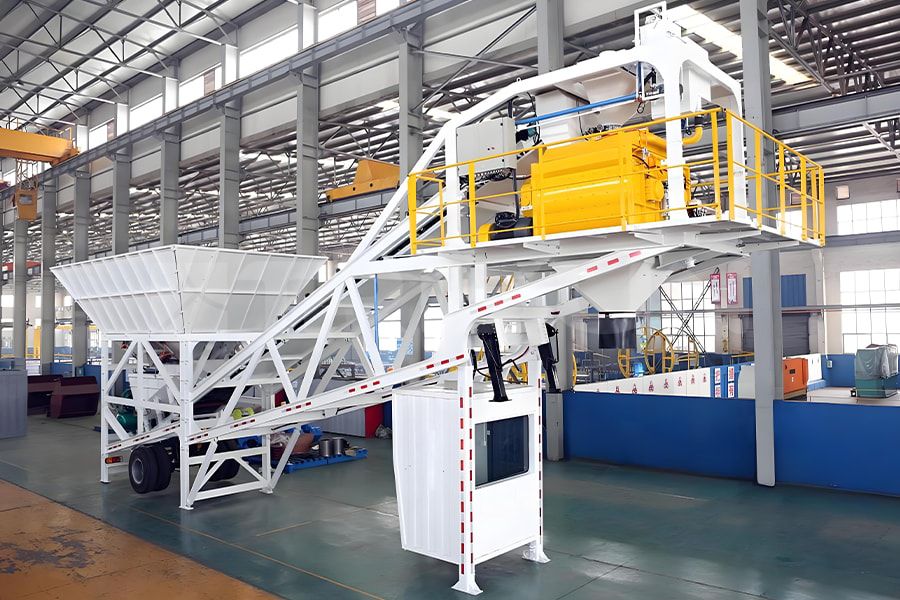
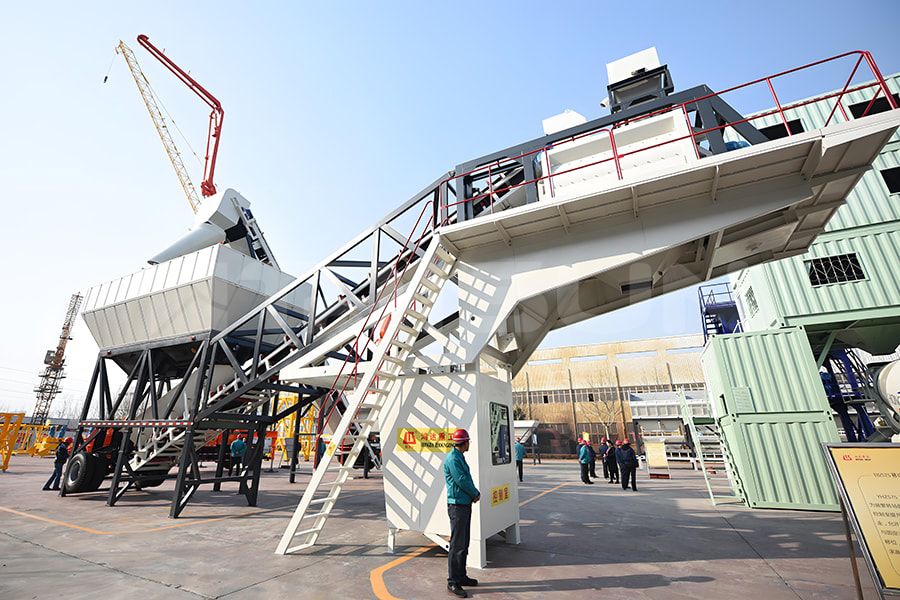
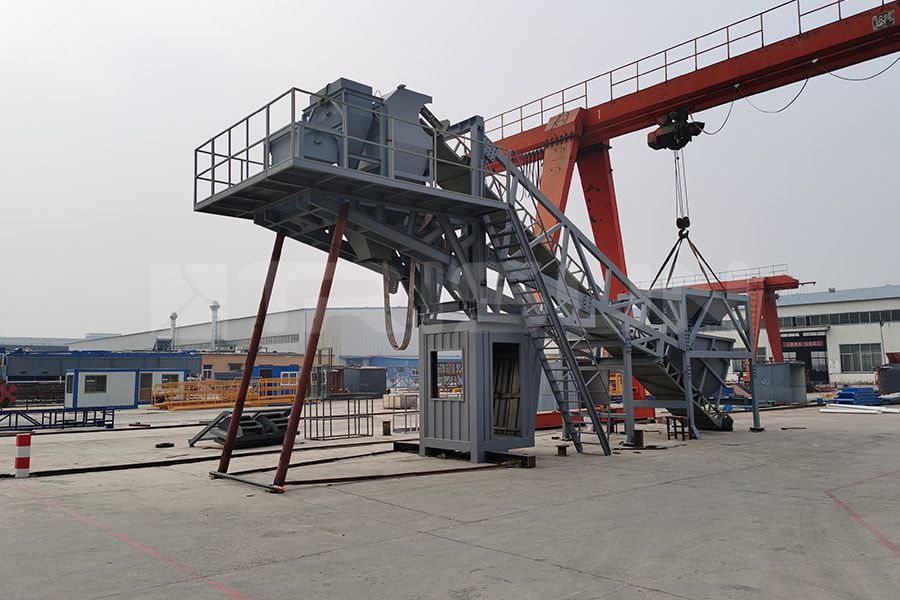
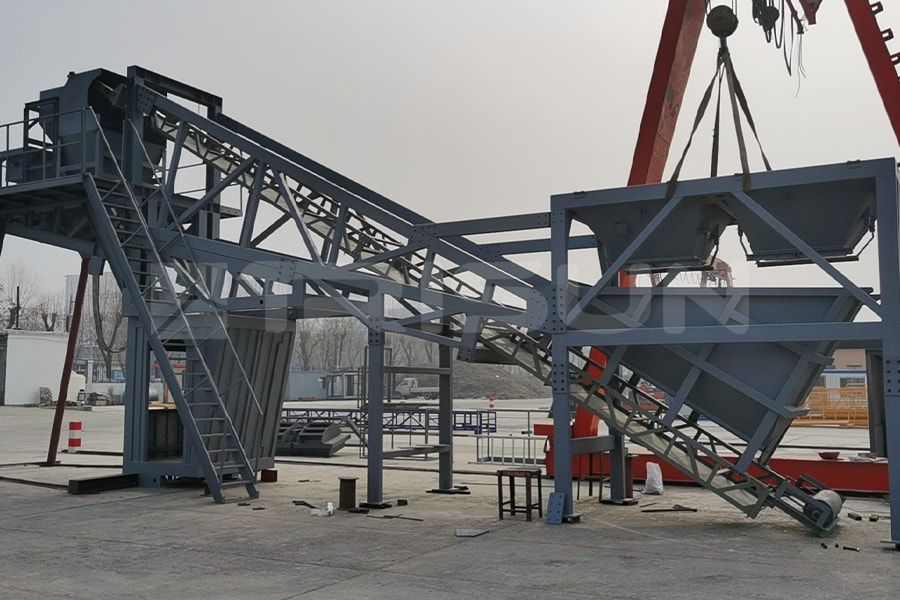
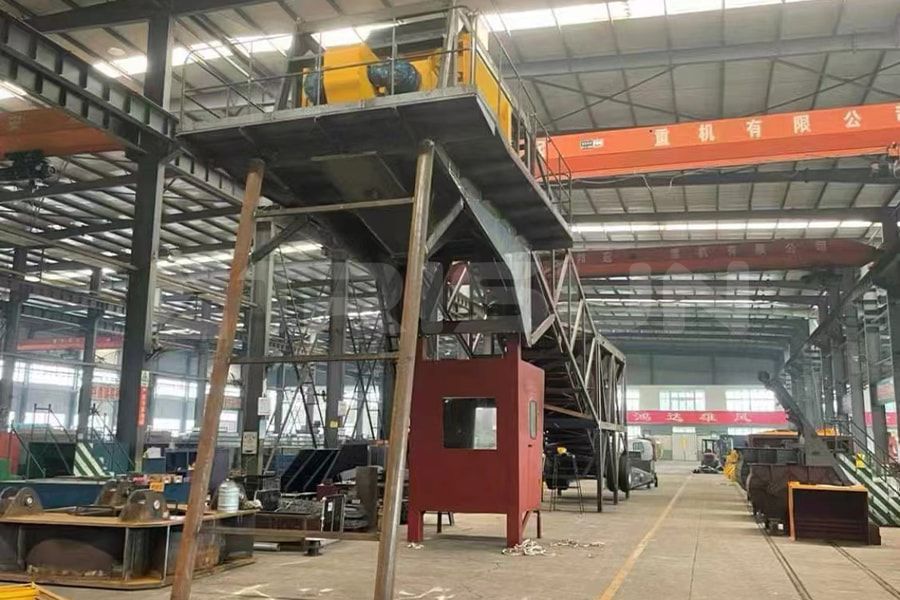
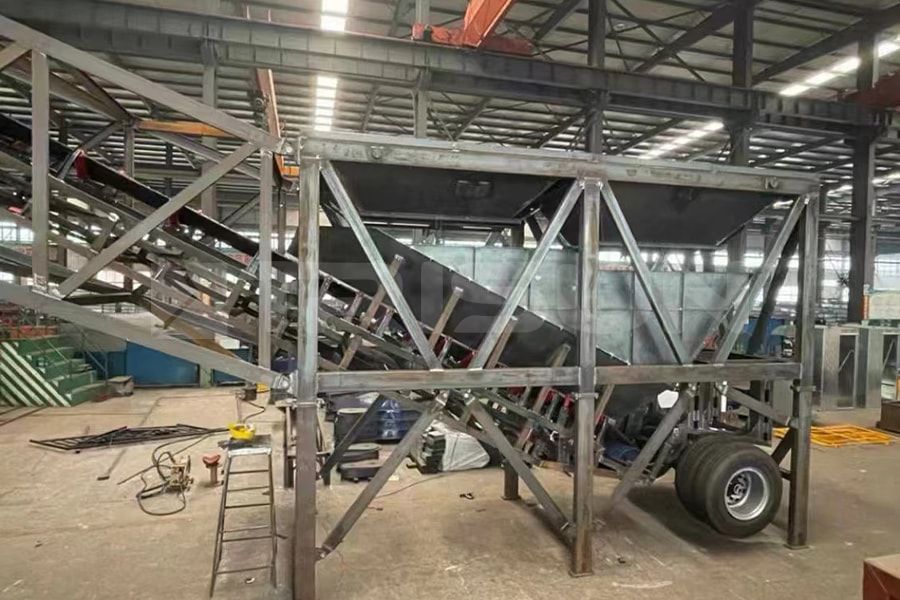
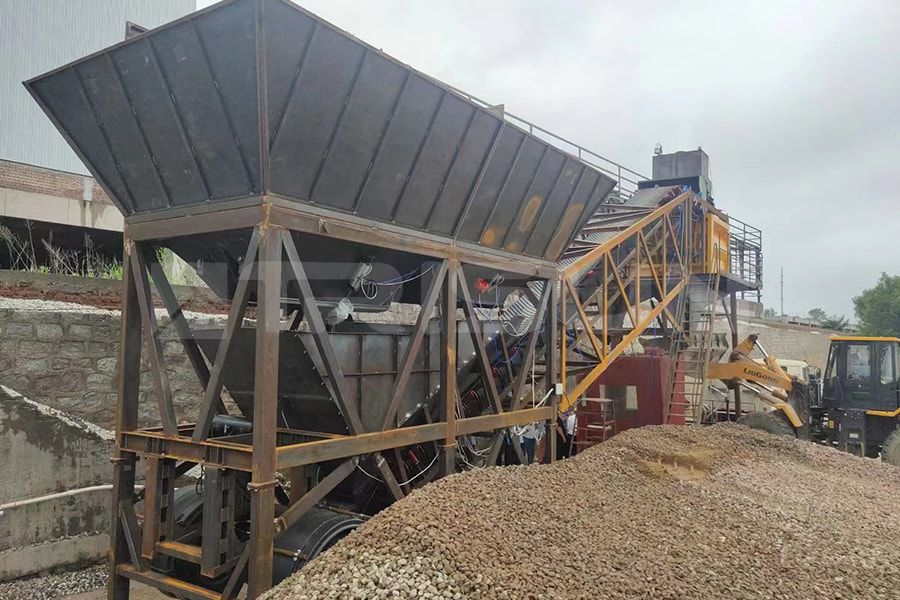
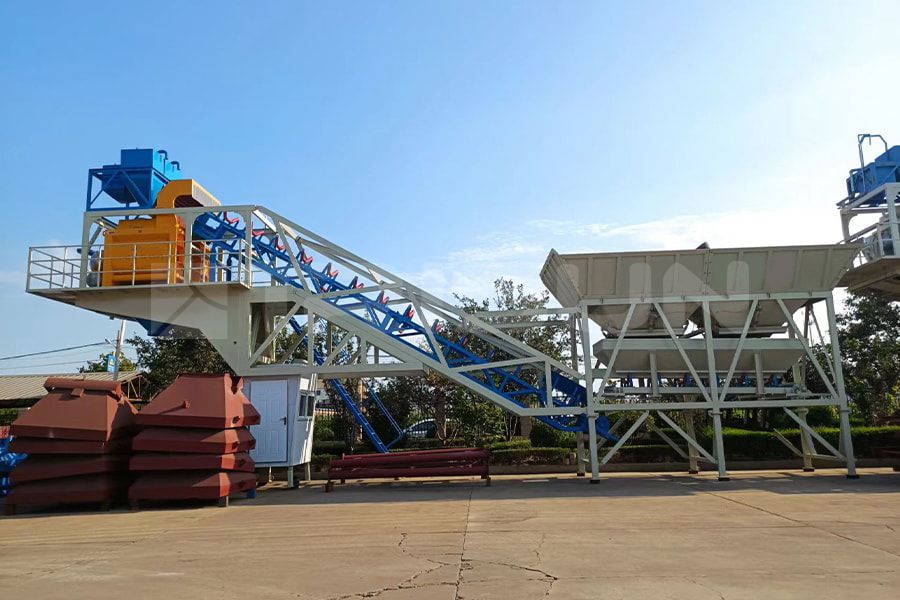
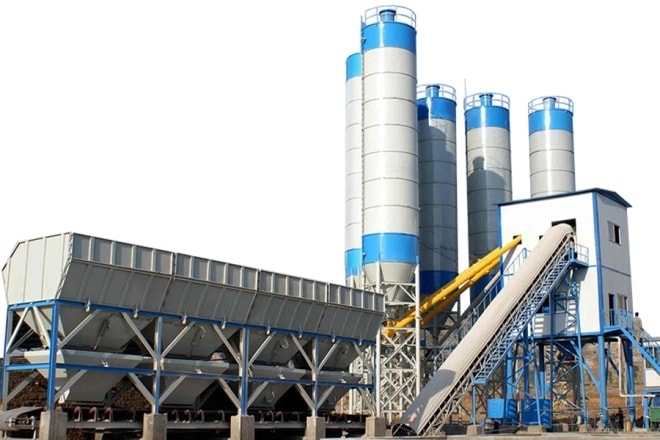
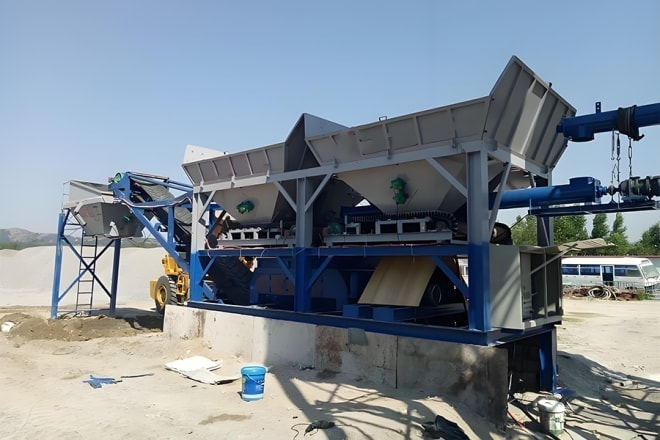
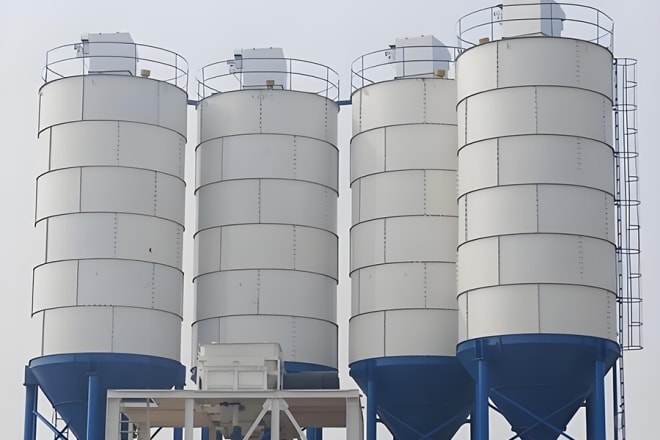
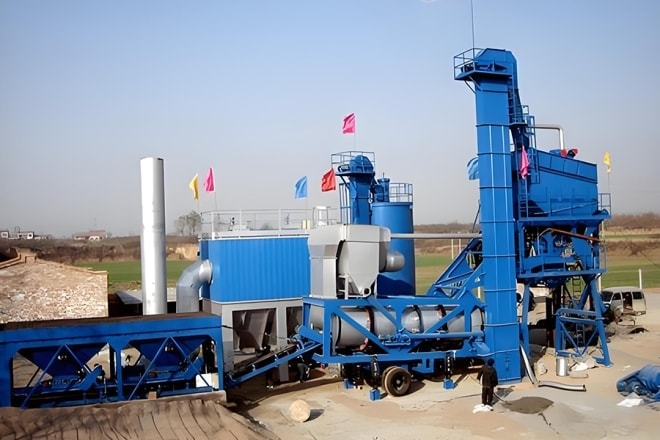
FAQ
Q: 1. What parts does a mobile concrete plant usually consist of?
A: 1) Towable chassis: The towable chassis contains the traction pin of the trailer truck and the outriggers for parking; the mixer, cement and water additive scales are placed on the chassis; inspection platforms, railings, etc. are attached around the chassis.
2) Control room: The control room is at the bottom of the chassis and is equipped with a fully automatic control system for the concrete plant. The control system is the same as the stationary concrete plant. In the working state, the control room serves as the front support of the entire plant. During transportation, the control room is stowed away in the space inside the bracket, and all its control lines do not need to be disassembled.
3) Batching system: This system is located at the back end of the entire plant. The upper part is an aggregate (sand, gravel) storage hopper. The storage hopper can be divided into 2 or 4 compartments, and is equipped with a heightening plate to increase the storage capacity. The doors open sequentially pneumatically. Aggregate batching is a cumulative method for multiple materials. The bottom is equipped with a walking rear axle and frame legs for work.
4) Belt conveyor: The belt conveyor frame is a truss structural member that connects the host chassis and the aggregate batching system, so that they are integrated to form the main structure of the entire mobile concrete plant.
5) Peripheral components: Cement silo and screw conveyor. The peripheral components are integral components during work or transportation and do not need to be disassembled, so they can be transported as a whole.
6) Host mixer: Generally, JS type forced mixer is used, which can quickly and evenly mix fluid and dry concrete.
Q: Compared with stationary concrete plants, what are the main advantages of mobile plants?
A: 1) Easier to transport, the main body can be transported by a tractor.
2) Faster and easier installation, removal, and transfer, with great flexibility.
3) The installation site space is small and can be installed within the project area.
4) Less concrete foundation required and can be installed on a flat concrete floor.
5) Easier installation licenses, in some cases no license is even required.
Q: What should I pay attention to when operating a mobile concrete plant?
A: When operating a mobile concrete plant, strict operating procedures must be followed. After all, mobile concrete plant is the core equipment of the concrete project, and equipment failure or component damage caused by human operating errors must be avoided.
1) Before starting the mobile concrete plant, be sure to check whether there are any abnormalities in each system of the equipment. If an abnormality is found, handle it in time. Do not force the machine to start, causing greater damage to the mobile concrete plant.
2) During the normal operation of the mobile concrete plant, always check whether the motor of the host mixer is overheated, and whether there is air or oil leakage in the air pumps, oil pipes, and pipes of each system. If the above phenomena occur, be sure to shut down the machine to deal with them.
3) When production is completed, the conveying pipes of the mobile concrete plant must be cleaned to avoid concrete remaining, causing pipes blockage or concrete corrosion of the pipes. When closing the mobile concrete plant, be sure to drain the waste water first to avoid corrosion of the mobile concrete plant.
Q: What are the differences or advantages of forced mixers compared to drum mixers?
A: 1) Convenient operation. To load materials into a drum mixer, you need to first start the drum to roll it, and then manually add sand, gravel, cement, etc., which is time-consuming and labor-intensive; When using a forced mixer, only the loader is required for charging, while the sand and gravel batching and transportation, hopper raising, charging, and mixing are all completed automatically, saving time, effort, and improving work efficiency.
2) Good sealing. The drum mixer is a double-opening mixing machine, which causes a lot of dust pollution during the charging and mixing process. However, the forced mixer mixes in a sealed horizontal barrel, so cement dust does not fly out and the working environment becomes cleaner.
3) High quality concrete. The mixing principle of the drum mixer is to use the self-weight of the material to mix as it falls during the rolling of the drum, so there may be uneven mixing of the material; The forced mixer mixes materials through double mixing shafts and mixing blades. The materials are uniform, the concrete quality can be 3 times higher, and the economy is high.