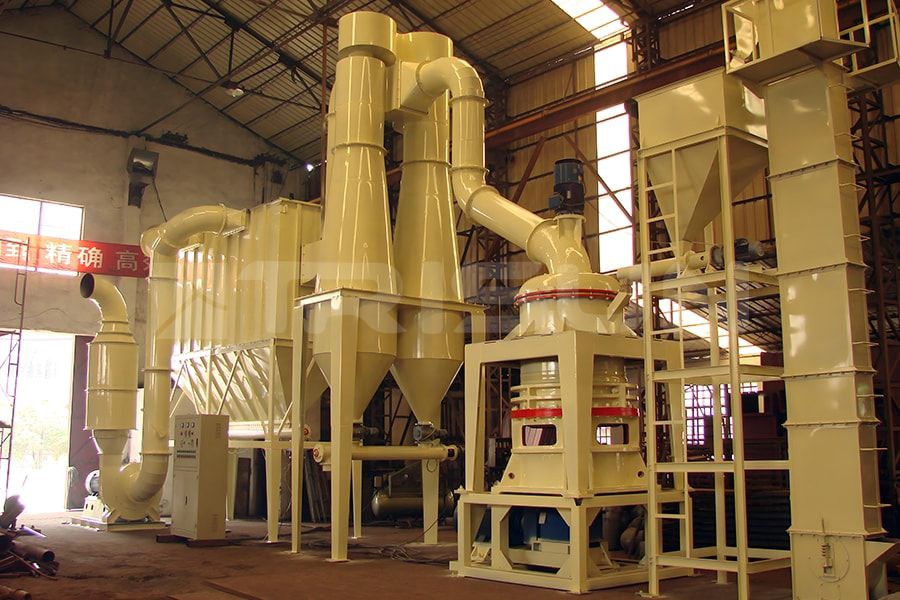
- Features & Properties
- Technical Specification
- Gallery
- Related Products
1. Efficient and energy-saving. On the premise that the fineness of the finished product and the power are the same, its capacity is more than double that of airflow mill, stirring mill and ball mill.
2. Long service life of wear parts. Its grinding rollers and grinding ring are forged from special materials, which greatly improves the utilization rate. Under the premise of the same materials and fineness of finished products, the service life of its wear parts is 2-5 times longer than that of impact mills and turbine mills, generally up to more than one year. When processing calcium carbonate, calcite, etc., the service life can even reach 2-5 years.
3. High safety and reliability. Since there are no bearings or screws in the grinding chamber, there is no problem that the bearings and their seals are easily damaged, and there is no problem that the screws are easy to loosen and damage the machine.
4. High discharge fineness. The fineness of the discharged product can reach 2500 mesh or even finer at one time.
5. Eco-friendly and clean. It uses a pulse dust collector to capture dust and a muffler to reduce noise, making it environmentally friendly and clean.
Model | Average working diameter (mm) | Ring quantity | Maximum feeding size (mm) | Discharging size (mesh) | Capacity (t/h) | Total power(kw) | Dimensions (mm) |
HGM80 | 800 | 3 | 10 | 150-3000 | 0.5-4.5 | 142 | 8605*4139x6050 |
HGM90 | 930 | 3/4 | 10 | 150-3000 | 0.6-6.5 | 180 | 11735*3952*7525 |
HGM100 | 1035 | 3 | 15 | 150-3000 | 0.7-7 | 242 | 14507*3633*7562 |
HGM100A | 1035 | 4 | 15 | 150-3000 | 1-8.5 | 380 | 16884*4019*8076 |
HGM125 | 1300 | 4 | 20 | 150-2000 | 2.5-20.5 | 401 | 19261*4406*8591 |
HGM168 | 1680 | 4 | 20 | 150-1500 | 5-45 | 665 | 25067*5414*9007 |
Note: All features, functionality and other product specifications are subject to change without notice or obligation.
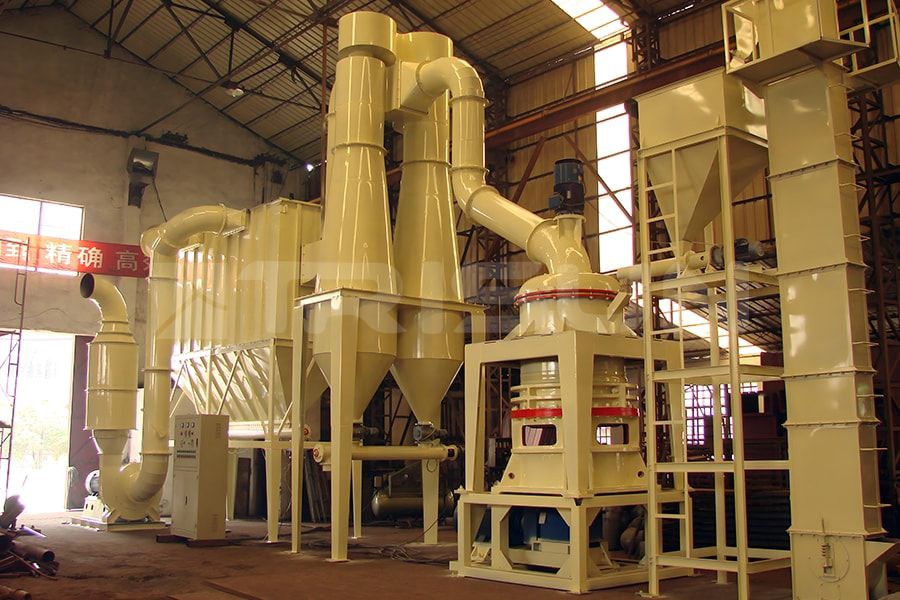
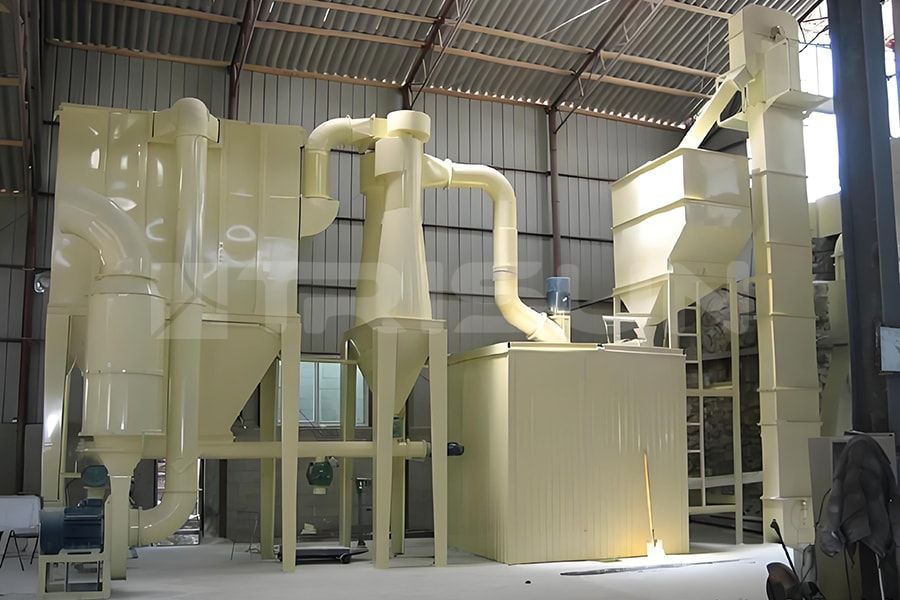
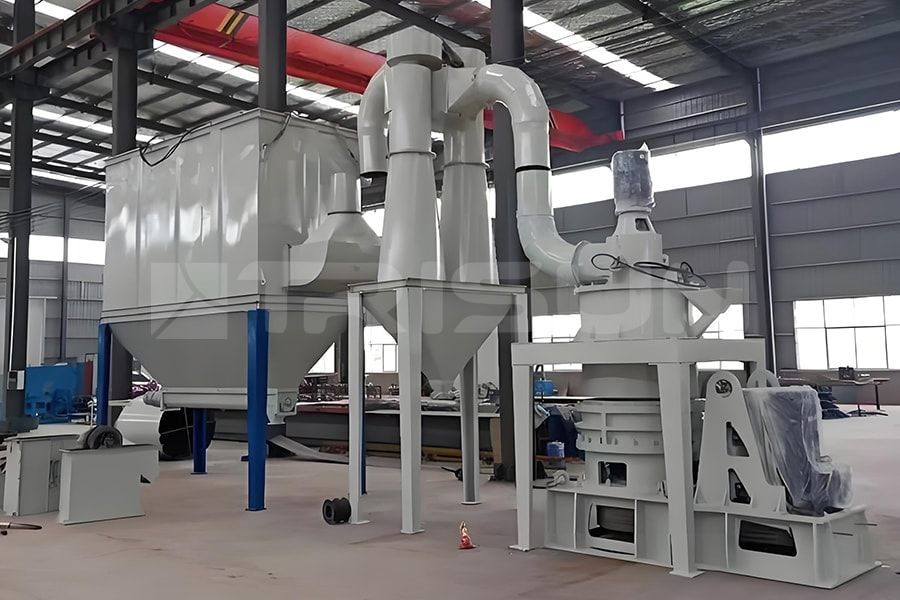
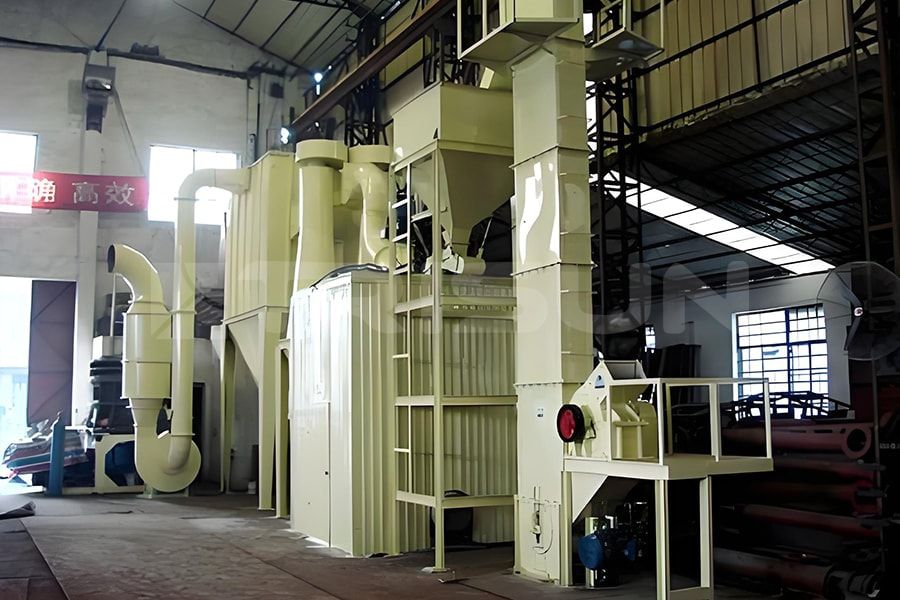
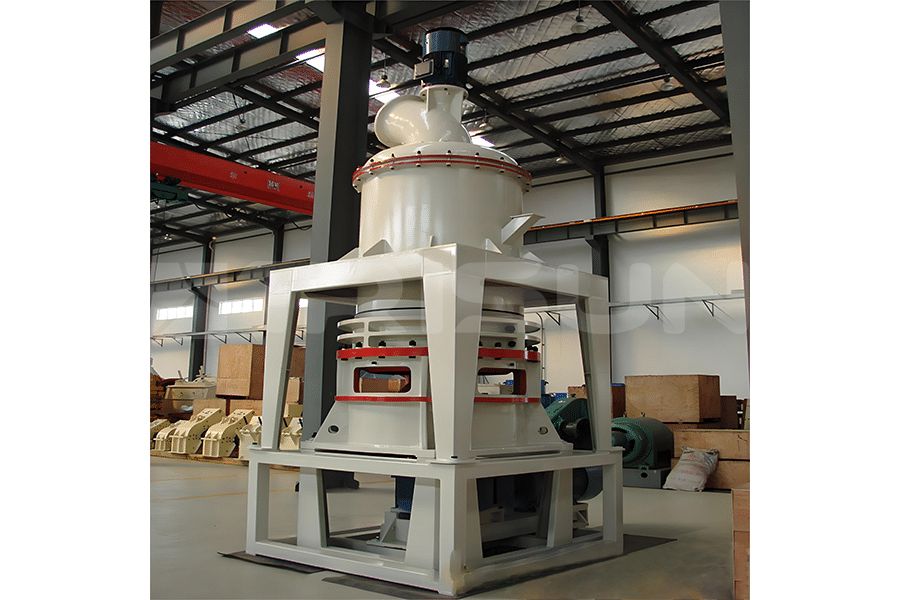

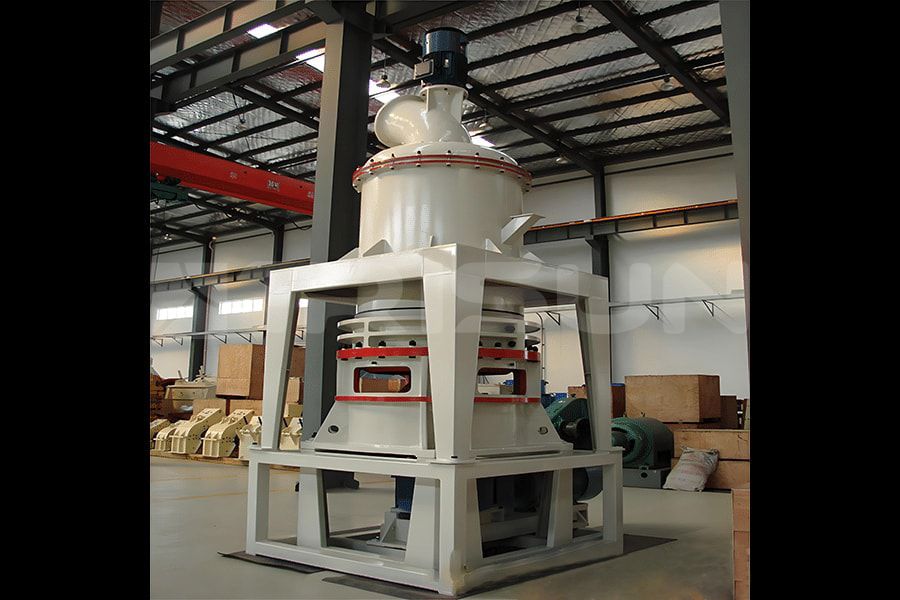
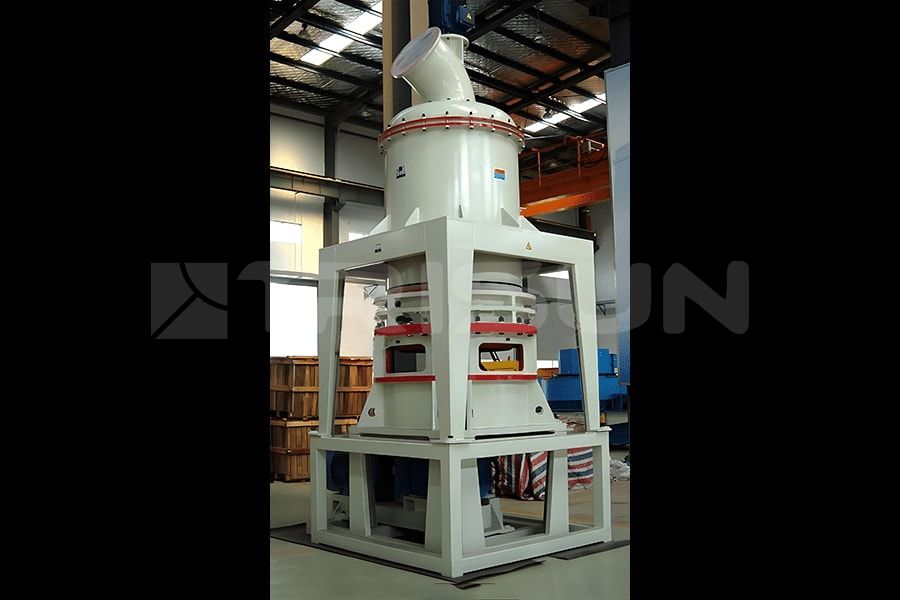
FAQ
Q: What are the differences between Raymond mill, ultra-fine mill and ball mill?
A:Raymond mill | Ultra-fine mill | Ball mill | |
Applicable materials | Dry materials with Mohs hardness below 7 | Dry materials with medium to low hardness | Dry materials, wet materials, iron-containing ores |
Maximum feeding size | 20-50mm | 10-20mm | 25mm |
Discharging size | 10-800 mesh | 150-3000 mesh | 10-300 mesh |
Capacity | 1-60 t/h | 0.5-45 t/h | 1-615 t/h |
Occupied area | Small | Large | Large |
Total power | Small | Large | Large |
Working principle | Combined effect of grinding rollers and grinding ring | Layered grinding of multiple grinding rings | Friction of materials between steel balls |
Investment cost | Economic investment | High investment | High cost of use |
Q: When used to make ultra-fine powder, what is the difference between a ultra-fine mill and an airflow jet mill?
A: 1) Under the premise of the same discharge fineness, the price of the ultra-fine mill is lower than that of the airflow jet mill, resulting in less investment, lower cost, and shorter recovery cycle.
2) Under the same fineness and power consumption of the discharged product, it has a higher powder yield than the airflow jet mill and the stirring mill, and the capacity is more than 45% higher.
3) All its wearing parts are made of domestic and international high-quality wear-resistant materials, which have a longer service life than the wearing parts of ordinary mills, generally more than one year.
4) There are no bearings or screws in the grinding chamber. There are no problems such as bearings, seals and vulnerable screws being easily loosened and damaging the mill, so downtime for maintenance is rare.
5) The fineness of the discharged product can reach 3000 mesh at one time.
6) It uses a high-capacity pulse dust collector. There is no dust pollution during the operation of the entire equipment. It is equipped with a silencer to reduce the noise. The production is organized in full compliance with the environmental protection standards, which plays an environmental role.
Q: What are the precautions for installation and commissioning of ultra-fine mill?
A: 1) The mill should be installed on a horizontal concrete foundation and fixed with anchor bolts.
2) Attention should be paid to the perpendicularity of the main machines to the horizontal plane.
3) After installation, check whether the bolts are loose and whether mill door is tight.
4) Be sure to configure the power cord and control switch according to the power of the equipment.
5) After the inspection is completed, a no-load test run should be carried out. If the test run is normal, formal production can begin.