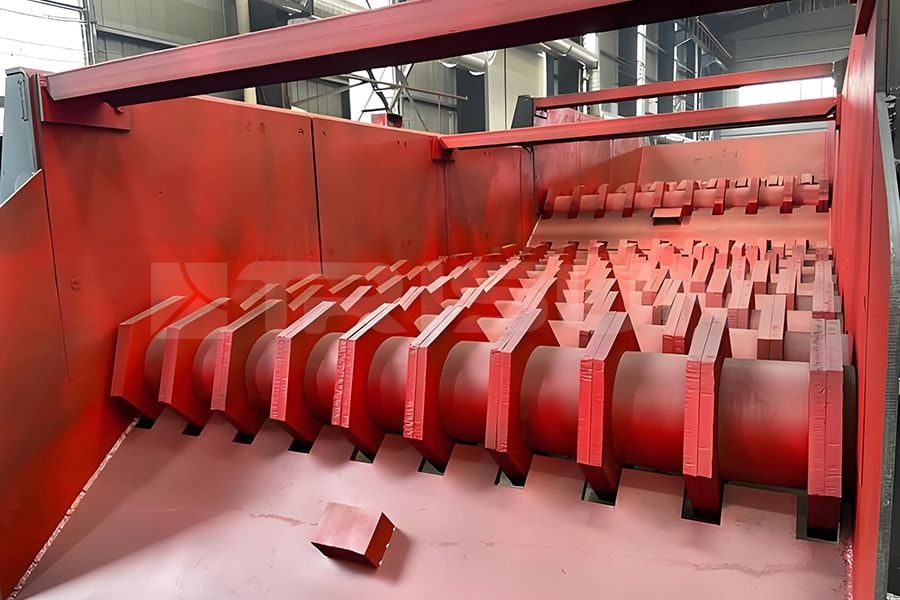
- Features & Properties
- Technical Specification
- Gallery
- Related Products
If the raw materials from the quarry have high mud content, direct use will cause problems such as clogging of the crusher, low production capacity, and poor quality. If done manually, the cost is too high and the efficiency is too low. Then the roller feeder can not only solve these problems, but also quickly separate soil and stones without adding water. It can replace traditional feeders and vibrating screens and is widely used in different working conditions. TRISUN can design different internal structures of roller feeders according to users' different materials and actual site conditions, such as multi-axis linkage or non-linkage, and the axis spacing can also be changed according to user requirements.
Model | Axis spacing(mm) | Number of axes | Maximum feeding size (mm) | Capacity (t/h) | Power(kw) | Weight (t) |
GZS0816 | 10-50 | 6-8 | 20 | 30-100 | 7.5-11 | 4 |
GZS1020 | 10-50 | 7-10 | 25 | 60-180 | 11-15 | 7 |
GZS1230 | 15-70 | 8-11 | 30 | 100-300 | 18.5-30 | 12 |
GZS1235 | 20-80 | 10-13 | 30 | 130-350 | 22-37 | 13 |
GZS1340 | 20-90 | 11-14 | 33 | 150-500 | 37-45 | 16 |
GZS1445 | 25-100 | 12-15 | 35 | 180-600 | 45-55 | 20 |
GZS1550 | 25-100 | 13-17 | 38 | 200-700 | 55-75 | 23 |
GZS1655 | 30-100 | 14-18 | 40 | 250-800 | 75-90 | 28 |
GZS1860 | 30-100 | 15-20 | 45 | 350-1000 | 90-110 | 35 |
Note: All features, functionality and other product specifications are subject to change without notice or obligation.
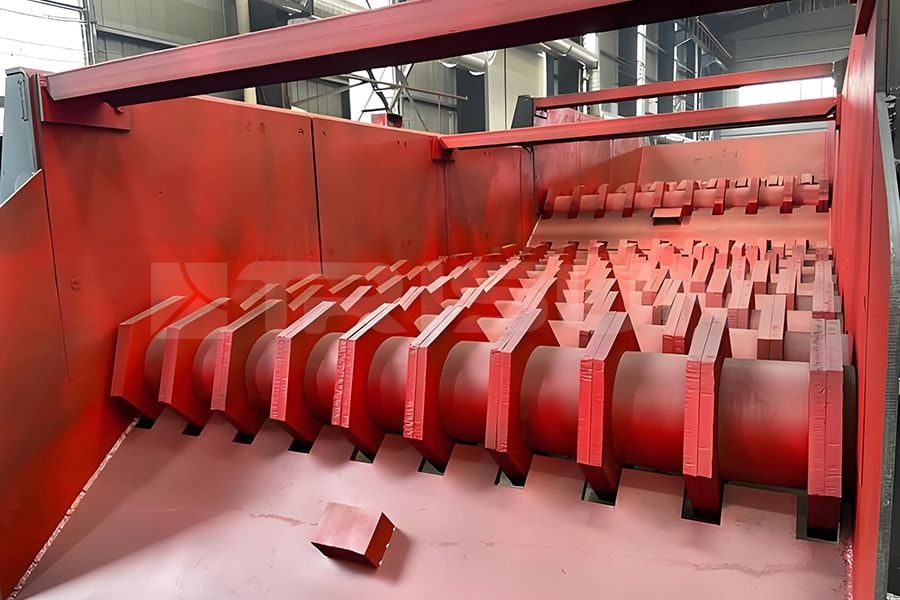
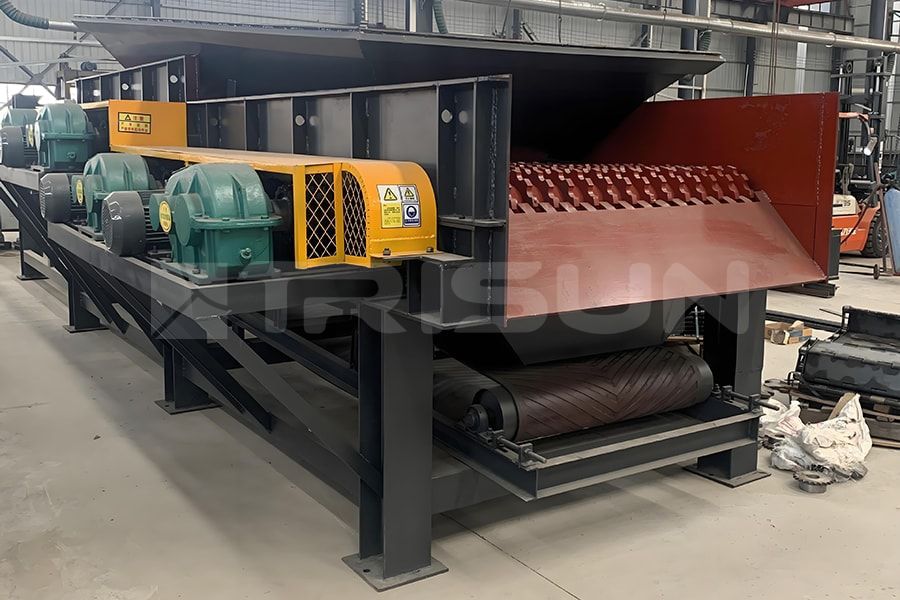
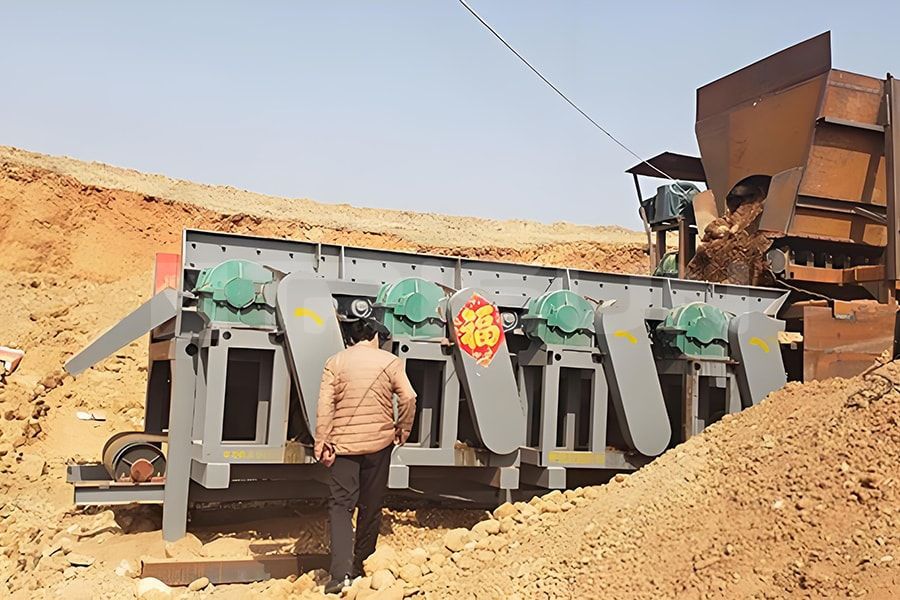
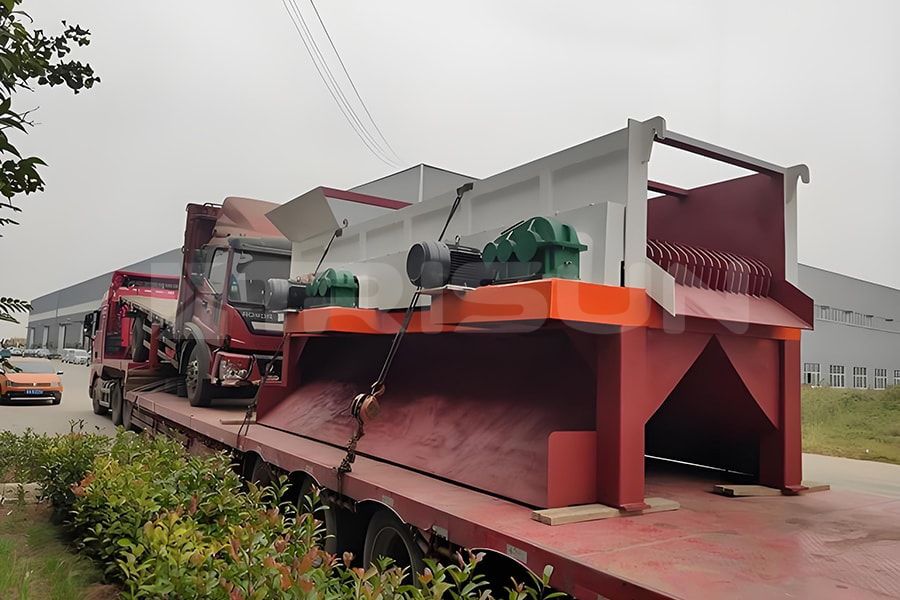
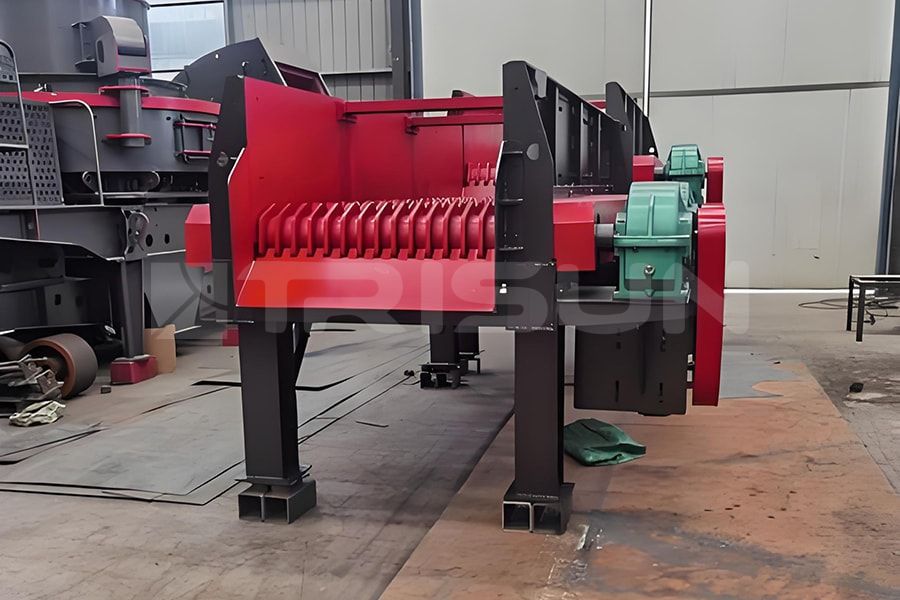
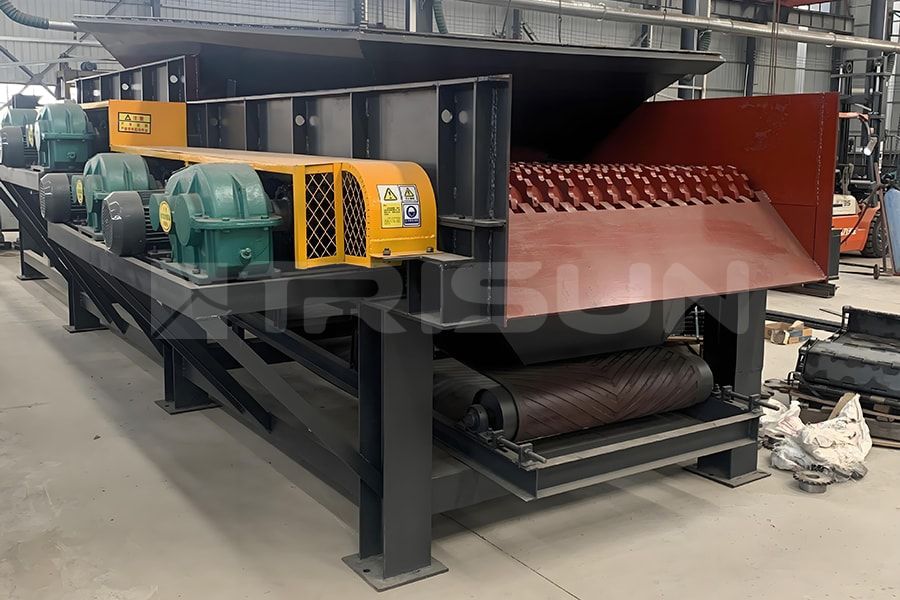
FAQ
Q: What are the advantages of roller feeders?
A: 1) High separation efficiency. Due to the rotation of the rollers and the vibration of the disc, the materials can be quickly transferred and contacted with the holes during the screening process. This high-speed movement promotes continuous collision and friction of particles on the holes, so that smaller particles can pass through the holes smoothly, while larger particles are retained on the disc, thus achieving screening.
2) High adaptability. The roller feeder can be adjusted and changed according to the characteristics and needs of the material. By replacing discs with different gaps and structures, particles in different particle size ranges can be screened. At the same time, the roller feeder can also adjust the speed of the roller and the operating parameters of the disc to adapt to the screening requirements of different materials.
3) Simple structure and easy operation. Compared with other screens, the structure of the roller feeder is relatively simple, and it is easy to assemble and maintain. The operator only needs to make simple adjustments and controls to achieve normal screening. Such characteristics make the roller feeder highly reliable and easy to use in industrial production.
Q: What are the main features of roller feeder (mud stone separator)?
A: 1) The screen shaft is driven by a single shaft of a roller motor for easy maintenance;
2) The screen shaft at the feed end is installed tilted, which can quickly separate materials and achieve high screening efficiency;
3) The screen pieces on the two screen shafts intersect, which reduces the dead angle formed by adjacent screen shafts and avoids screen jamming;
4) It is equipped with a bypass, equipped with an electric push rod and a manually operated reversing mechanism, which facilitates maintenance and cleaning;
5) The bypass reversing plate adopts a fence structure. When the material falls onto the reversing plate, some particles are first screened, which beneficially improves the screening efficiency;
6) The panels on both sides are designed with movable insert structures, which is very convenient when it is necessary to replace and repair the screen shaft, screen discs and anti-corrosion lining plates;
7) It is equipped with material blocking alarm and electrical control safety protection device to avoid equipment damage caused by abnormal operation.
Q: What are the selection principles for roller feeder (soil rock separator) ?
A: 1) Rated capacity should be slightly greater than planned capacity. If the rated capacity is lower than the planned capacity, the roller feeder will be overloaded and the service life will be reduced; on the contrary, it will cause waste and increase procurement costs.
2) Under the same conditions, try to choose a model that is easy to repair. Mining feeders basically operate in the open air, and the harsh environment can easily cause the machine to malfunction, and easy-to-maintain models can save maintenance time and costs.
3) Each part should be standardized and serialized. In this way, when replacing damaged parts, they can be replaced directly without modification and debugging.
Production safety. Safety is the prerequisite for production, and unqualified models and accessories must not be used to save purchase or maintenance costs.